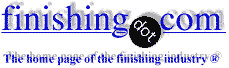
-----
Coating Process (Palladium/Ruthenium Alloy)
Q. I am looking to identify a process to apply a Palladium/Ruthenium coating to a small cylindrical part used for an in-cylinder automotive combustion application. The part will need to be uniformly coated inside and out. The length is roughly 30 mm long, I.D. 4.5 mm and O.D. 5.5mm. I need to consider two designs:
1. one end of the part capped
2. one end of part uncapped.
The part is made of Incoloy 800. Volumes could range from 20K - 100K per year. The following is a list of processes that may work: Electrolysis, Electroless, CVD (Chemical Vapour Deposition), Catalyst spray or Catalyst paint. Please help with identifying a known process that is feasible.
Thank you,
- Dearborn, Michigan
2002
by Abner Brenner
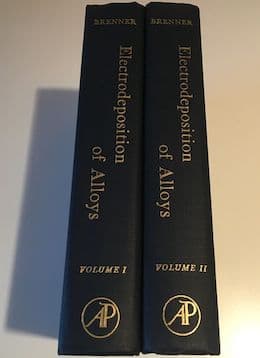
on eBay or Amazon
or AbeBooks
(affil link)
A. The part can be done by several of the methods you mentioned, but the big question would be what is the price target, how thick does the coating need to be, and what is the uniformity spec for the inside length?
Electroless for these metals would work, even in a barrel, but the inside would not be as uniform as as the outside. Barrel electroless would offer cheap labor & capital equipment per part, but low plating rate, expensive chemistries, and would require a relaxed uniformity spec on the inside. The low plating rate can be offset by large lot size in a barrel. Another electroless method that may lend better uniformity is to stand them all in a batch on end on a vibrating screen and pump the electroless up through the screen where it overflows back into the reservoir.
Electroplating would give high plating rates/part and superior uniformity on the inside but would require a higher capital equipment investment as each part would be placed over an electrode for the plating step while solution is being pumped through it. There are many more such tricks.
Hope it helps,
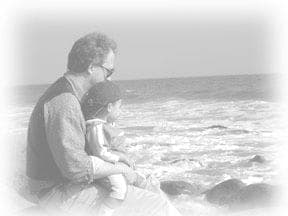
Dave Kinghorn
Chemical Engineer
SUNNYvale, California
2002
Q, A, or Comment on THIS thread -or- Start a NEW Thread