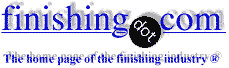
-----
Small parts coupling together in MSA Sn (Tin Plating) bath

this text gets replaced with bannerText
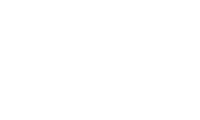
Q. I am plating small ceramic capacitors in a barrel plating process. The parts are 0.060" by 0.030" by 0.030", they look like tiny bricks. Each end of the capacitor is dipped in copper paste to about 0.012" down the length. The electroplated metals are pure Sn over Ni.
I am experiencing a coupling phenomenon in the Sn plating process that occurs at a 1-5% rate. Typically there are two parts neatly coupled together, however I do find up to six capacitors coupled together. I add SS shot to the load and it also couples together. The coupled parts separate easily without damaging the metallized surfaces. There is always Sn where the parts are separated, however the Sn structure is significantly different than the exposed faces as it is not burnished from the tumbling in the barrel. The Sn at the coupled interface is always thinner than at the exposed faces. This tells me that the coupling occurs during the Sn plating process.
This is an MSA Sn bath operated at a pH of 3.5, and room temp. Plating time is 70 minutes to achieve 200 microinches of Sn. I have tried varying rotation speed from 10 - 52 RPM's. Temp from 22-32, pH from 3 to 4. I have added plastic blocks to the load, obstruction to the inside of the barrel, different types of mesh on the barrel, high and low current density, varying levels of the wetting agent, and intermittent current. Time is definitely a factor here, however I am limited in how low I can go. At 70 minutes and the best conditions of those mentioned above and I still experience the coupling. Can someone tell me what I am missing?
Thanks and saludos,
Rich Reifenheiser- Monterrey Nuevo leon, Mexico
2002
by Almeida-Didry, Autret, & Gervais
Amazon
on AbeBooks
(affil link)
A. Rich,
I know that some surface-mounted capacitor manufacturers have invested pretty heavily in process development against this exact problem and the problem of the tin bridging across the body of the capacitor. It may be that the coating or the profile of the unplated surface is encouraging two of them to stick together through surface tension. You may need to modify the barrels or the parts to discourage this capillary attraction.
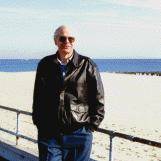
Ted Mooney, P.E.
Striving to live Aloha
(Ted can offer longterm or instant help)
finishing.com - Pine Beach, New Jersey
A. Hi Rich,
I understand the problem you are facing. I worked on similar project few years back. We were plating Chip resistors and Chip network resistors or different sizes. 1206, 0805, 0603 etc. Since they are flat they tend to get struck due to surface tension and as the plating goes on the get coupled together. This is called "coupling" in SMT components plating which particularly appears during Tin/Lead plating.
We were also using a MSA bath to attain a composition of 80/20 Sn/Pb using 8.5 ± 0.5 gpl of Tin and 1.2±0.2 gpl Lead in the solution. The important thing to maintain is the composition of the bath constituents. Prior to Tin/Lead plating we do Nickel plating and provide a thickness or 3 to 5 micron. This provides a very good barrier layer during soldering. After nickel plating we have observed that the components don't get struck with each other as nickel layer is smooth and hard. But when the same components go for solder plating, they get struck together and Couple. (i.e., softer the metal the better it couples)
First we ensured that sufficient thickness of Nickel is built up so that the barrier layer is intact. The composition of the Sn/Pb in MSA bath is very important. If the concentration is not maintained properly then you will have such problem. The problem occurs when the concentration goes on the upper end. i.e., It is not that you maintain the metal salts ratio in the bath. But the total concentration should be lower.
Try the following.
1. Maintain Sn and Pb concentration at lower end. Don't control the ratio alone. Keep check on the total metal content on the bath. (if possible operate with the lowest ratio recommended for the bath)
2. Limit the rate of plating. Try to plate at a LOW CD. We were plating at 0.3 to 0.5 ASD for 25 - 30 min to attain sufficient thickness.
3. Do not build excess thickness. Plating thickness of 5-7 micron is sufficient for good solderability.
4. Keep the bath clean (pls refer letter 15140 - Tin sludge formation in MSA solution with a tin reactor).
5. If the metal contents are high the coupling formed will be hard to break. But under lower metal content there will not be any coupling and even if it is formed it will be very soft (tends to break easily).
6. After plating in MSA bath Neutralize in a Tri Sodium Phosphate bath (10% soln) followed by rinse in Hot DI water with Ultrasonic. This will break the coupling formed. (in case if it had been formed)
Lower metal concentration in bath and Slow plating rate is the key to solve this problem. Hope this should help you.
Good luck.....
Karthik- Singapore
A. Hi Rich,
I am actually working in the same multilayer capacitors field right now, and what I can tell you is that the coupling problem you are having is very familiar to me. I think current is one of the most important factors to consider in this case, along with the size of the media, and also the pH of the MSA tin bath. I have noticed that at pH below 2.0 this problem occurs more often, but I don't think this is your case. If you plate in 6" dia. barrels and the volume of the chips and shoots is below 1/3 of the inside volume of the barrel, I have had very good results plating at 4 Volts (No amps). Then a hot 1% TSP bath and finally a hot rinse.
Good Luck!
I hope we can talk about this problem again.
Bye,
Reynaldo Arroyo- Valencia, California
A. Hi Rich:
We have found that there are both chemical and equipment technologies that can help prevent coupling of small passive components. There are alternatives to the standard MSA process commonly used in this industry, and these alternatives are now in production and plating 0201 sized parts in barrels without any coupling.
As you know, alternative equipment to the barrel can also prevent coupling. The Gets RFT plater is such a machine, but has other issues that make it not a universal solution to this problem. A new machine called the SBE Plater (Spouted Bed Plater) has been introduced to the small parts plating industry, and this technology can be retrofitted into existing barrel lines. This equipment pumps a stream of plating solution up into the bottom of a plating chamber. The stream lifts the chips into an internal tube in the plating chamber. As the parts exit this tube, they are deflected back down to the bottom of the plating chamber. The deflection helps to eliminate the coupling problem, yet does not damage the parts because the deflection takes place under solution. Plating occurs when the parts reach the bottom of the plating chamber. Circulation of the parts throughout the chamber is quite rapid, which also reduces coupling. An added benefit is that the thickness distribution is far superior to any barrel operation.
Best regards,
George A. Federman- Plainview, New York
Coupling, chips sticking together during barrel plating
Q. I am struggling with our resistors sticking together during Au plating after Ni plating. The chips are 20 mils x 20 mils x 10 mils thick.
My potassium cyanide bath is at 140 °F. I am losing half my chips to this. I only filling the barrel to 1/3 in volume of shot and plating 2000-4000 chips at a time. I've tried lowering temp, lower/higher fill volume, changing current density. I am at a loss.
MiniSystems Inc - North Attleboro, Massachusetts
October 24, 2017
A. Instead of a traditional plating barrel, try a "vibratory plating barrel". If you google that, you will find examples. There is a well known precious metals supplier with an equipment division near you that makes them. They are designed for applications such as yours.
Peter Cox- Sweden, Maine USA
Thank You Peter, I will look into that.
MiniSystems Inc - North Attleboro
Q. Hi, I have similar problem of stick issue, what caused conductive media to stick to each other during plating of inductor
Matt Jemm- Wuhan, China
April 11, 2020
Q.
I am currently working at Plating and we're producing Inductor Chips. Problem we're experiencing is occurrence of Sn Unplated Chips. The frequency is very low (only around 1~4 chips/200,000). But since it cannot be sorted out in the visual sorting machine, high chance that there will be an outflow to our customer :-(
It usually occurs on chips sizes 25 x 20 mm. We are using barrel plating and using MSA Tin. Our Sn metal concentration is around 15 g/L , pH is 3.2 and our Sg(Be) is at 17.
We have tried also increasing Barrel rotations RPM but same problem still exist.
Employee - Laguna [Philippines]
March 22, 2023
A. Hi Arlene. With essentially five nine's satisfactory production, don't even think about tinkering with a good line by tweaking your process chemistry :-)
Obviously there is a problem here, seemingly related to larger inductors, which must be solved either by better inspection or by figuring out a way to separate the inductors better so they all plate. Perhaps either the barrels or the parts need some kind of dimples or reverse dimples to prevent capillary action from holding parts so tightly together or to the barrel wall that plating does not occur in the interspace?
Luck & Regards,
Ted Mooney, P.E. RET
Striving to live Aloha
(Ted can offer longterm or instant help)
finishing.com - Pine Beach, New Jersey
Q. Thanks Ted,
However, your recommendation of dimple or reverse dimple is not applicable since the wall of the barrel we are using is not pure solid, we use nylon mesh
Employee - Laguna [Philippines]
March 30, 2023
A. Hi again Arlene.
Your reliability results strike me as already excellent for barrel plating. Although I am not personally familiar with the specialized equipment involved in spouted bed electroplating, as mentioned by George Federman on this page, I do see that the concept of spouted bed processing of small items is widely applied these days in many diverse fields. If I were you I think I would study up on the technology so you are able to expertly discuss it with your team moving forward.
Luck & Regards,
Ted Mooney, P.E. RET
Striving to live Aloha
(Ted can offer longterm or instant help)
finishing.com - Pine Beach, New Jersey
Hello Ted,
I will read more about this Spouted Bed Plater Technology. Thanks Ted
- Laguna
April 2, 2023
Q, A, or Comment on THIS thread -or- Start a NEW Thread