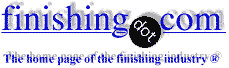
-----
Stressing problems with watts nickel solution
2002
Q. I would appreciate any thoughts regarding a problem we are having with our watts nickel solution. We are plating heavy deposits (.010" to 0.060) generally prior to hard chrome plating. The problem we are experiencing is that the nickel is very hard and peels off the job. We treat the solution with peroxide and activated carbon etc to remove organics and metallics. The first 2 jobs plated are OK but the 3rd and 4th jobs the nickel is stressed and does not adhere to the job. This has been an ongoing problem for some months and in an attempt to remove possible causes of the this stressing we have
1: fitted a polyethylene liner in the tank
2: replaced the anode bags
3: regularly replace filter pads (the solution is continuously filtered using pads type filters with activated carbon)
4: fitted a filter to remove any possibility of oil contamination
5: bought guaranteed clean sulfuric to adjust the pH (we commence plating at pH of 4.2 which generally rises to approx. 4.6 after 12 hours)
6: the nickel solution is within spec in relation to nickel sulphate, nickel chloride, boric acid etc.
Our chemical supplier can only suggest to add a stress relieving agent at a rate of 20 ml/litre of solution. The stress reliever offered is based on saccharin. Does anyone use such a product and have any experience when plating heavy deposits?
Any thoughts would be more than appreciated.
Thanks,
Chris Riley- Newcastle, NSW Australia
A. Chris,
Saccharin will indeed reduce stress but many reports show that hardness will also increase. Also, sulfur will be included in the deposit with the consequent loss of high temperature properties, and you probably don-t want that. Your problem seems more like a cumulative consequence of previous steps or operation. Are you using baskets with pellets, or solid bar anodes? How do they look? What about your substrate? Could it be leaving contaminants? And your carbon and H2O2 purification? If excessive could include more carbon and Oxygen than desired in the plate. Also, I noticed no mention to dummying, it-s the most effective cleaning procedure. Are you doing it?.
Guillermo MarrufoMonterrey, NL, Mexico
2002
A. Chris:
For this heavy deposits I think the best way is nickel sulfamate. With sulfamate you reduce the hardness and the stress. We do this heavy deposits (1 to 5 mm)with nickel sulfamate. I think that your could have also a cleaning or and activation problem of the substrate. As an example, we experienced a problem like this plating 5 mm of nickel over copper and the reason was a small quantity of Zirconium alloy with the copper. We solve it changing the activation procedure.
To check your plating solution, make adherence tests with a well-known substrate and well-known surface preparation procedures.
Angel Vidal- Spain
2002
A. Chris,
I read your problem in nickel tank for stressing and peel off. I think you have too much brightener in the tank or brightener feed rate is too high , you need to dummy nickel bath with 5-10 asf ( amps per square foot) for few hours without brightener feed. Check the carrier type of the brightener in your nickel tank to help for stressing, make sure carrier is not suppose too low.
Check the current in your nickel tank , Make sure the current not break down during the plating.
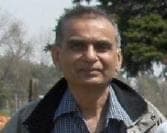
Popatbhai B. Patel
electroplating consultant - Roseville, Michigan
2002
![]() |
A. I agree with the other responders, but would like to add a few comments. Firstly, there is very little detail as to the actual process being carried out. What is the volume of your electroforming tank and what are your deposition conditions? How hard is "very hard"? What is your mandrel made from and is it adequately cleaned and activated? Is there any possibility of drag-in from the upstream stages? You also say the problem has been ongoing for some months, but is it since you began this job or has it always been there and with other jobs? You do not give details of your present additives; some organic additives, such as naphthalene trisulphonic acid (NTS), are extremely difficult to remove from plating baths and peroxide treatments will not shift them. Why did you fit a polyethylene liner to the tank - did you suspect contamination from the tank lining? Using an activated carbon filter all the time can result in the continual removal of organic additives, so perhaps you have been taking out your stress relievers. Personally, I like to run electroforming tanks at filtration rates of about 9-10 turnovers per hour with a 1 µm or less filter; I only use a carbon filter as a by-pass and use experience of the job and tank to judge if it is on the whole time or only some of the time. I would suggest you limit the flow through the carbon to about 10% of the total flow through the filter; this helps keep the bath in spec. I also wonder why you have not tried a low current dummy, as this can often take out unwanted contaminants. Watts nickel baths are usually tensile stressed, so to begin with you are not giving yourself much leeway. Your description definitely infers tensile stress in the deposit. I would also agree with the idea of using a sulphamate based bath, and even go as far as suggesting a Hi-Speed bath, which uses a nickel sulphamate concentration of about 600-650 g/l. This was originally developed by INCO and has been marketed by at least one international supply house. I like to run sulphamate baths at between pH 3.8 and 4.2, which is lower than a Watts bath, but I see no major problem with your present pH range; however, I am not sure whether you feel a pH shift from 4.2 to 4.6 in 12 hours is expected or not. This could be symptomatic of a too heavy workload for you tank volume. Personally I like to run nickel baths at the top end of the boric acid range as this buffers the pH; however, everyone to their own! Your symptoms tend to suggest there is a drag-in of an impurity as the first electroforms after your treatments are OK, but then deteriorate; hence, changing the bath composition may not solve the long term problem. I would suggest you carry out Hull Cell ⇦ huh? tests to verify the performance and composition of the bath; you should also do some stress tests to determine exactly when the bath starts to fail. Are you using the bath for this dedicated job or are you running other jobs in parallel? If you are, this could increase the drag-in situation. The addition of saccharin, preferably as sodium saccharin as it is more soluble, will reduce stress, but it will also harden and brighten the nickel. I believe the addition of more than 0.3 g/l sodium saccharin will make the Watts bath slightly compressive, but this addition has other problems. Firstly it will harden your deposit even more and secondly it will put sulfur into the electroform. This can have problems as if the nickel electroform is heated to over about 170 °C it will become brittle. This may or may not be a problem to the finished electroform. If you need a hard deposit, try adding cobalt to the solution; this has the advantage that it will increase the hardness to about 550-600 Hv with no detrimental affects to use at high temperatures. I would seriously consider changing to a sulphamate bath and run with about 0.2-0.5 g/l sodium saccharin, but there are other alternative stress relievers such as coumarin, p-toluene sulfonamide and if you can live with a slight tensile stress (ca 140 MN/m2), you could consider glycine. One benefit of a sulphamate bath is that, if you use S-nickel rounds, you don't need any chloride in the solution, so this will further reduce the stress; however, many electroformers still continue to use about 10 g/l chloride just to be on the safe side. I think you should also be aware that trying to coat electrodeposited nickel that has come from a bath that is heavily loaded with a lot of organics can be problematical and needs good activation. This is being discussed elsewhere on this site. I hope these ramblings are of some use and I apologize to anyone for the length of this reply, but with the shortage of original problem details, one can only speculate on causes and make suggestions based on these speculations. ![]() Trevor Crichton R&D practical scientist Chesham, Bucks, UK 2002 A. Hi Chris, you do not remove metallic contamination with carbon treatment or H2O2. You could have a metallic contamination. We run a modified Watts bath with Pulse Reverse without problems. Layer thickness up to 5 mm. Have you considered using Pulse Reverse? Lars B. Andersen- Denmark 2002 |
A. Watts nickel is inherently stressed. You may be seeing de-lamination (separation within nickel layers). Send a sample of a good deposit and a peeled deposit out for metallographic examination. You may see a difference in grain structure, which would be an effect of bad bath chemistry. Perhaps by the time you get to the 3rd or 4th load, you have lowered a bath component to below it's lower limit.
Steve Delaney- Ontario
2002
Q. Hi my name is ASAD Iqbal and I have a electroforming plant we manufacture rotary screens in PAKISTAN I'm using watts solution in my plant but from few days I'm noticing problems of hardness in my rotary screens I did dummying I had also treated my solution from activated carbon but problem of hardness is there I had checked my watts solution every thing is ok in solution I don't know what to do, few days back I added nickel sulphate in solution for make up do you think if the quality of nickel sulphate is not proper problem of hardness can occur ? please help me I'm in gr88 trouble thanks.
Asad Iqbalmanager - Pakistan
July 27, 2008
A. What is your problem with the hardness - is it too high or too low? What are your plating conditions and bath composition? Without this important information, no-one can give you a sensible answer, but can only guess at what you are trying to sort out. What you are telling us is like asking someone why your car doesn't go after you put some water in it....
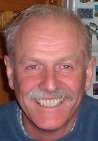
Trevor Crichton
R&D practical scientist
Chesham, Bucks, UK
July 30, 2008
Well you're right my brother. Okay, let me tell you first condition of my bath I keep temperature up to 68 degrees and its pH is 4.0 to 4.2 nickel sulphate is up to 300 grms/liter boric acid is 50 grm/liter NiCl is 8 gms/liter I want to reduce stress in my product I'm using META-BENZENEDISULFONIC ACID as stress reducer can you please let me know what should be its concentration in my bath and other measures I can take to reduce stress of my product to zero thanks.
Asad Iqbaldirector - Karachi, Pakistan [returning]
August 10, 2008
Q, A, or Comment on THIS thread -or- Start a NEW Thread