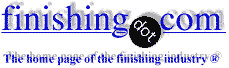
-----
Economics of zinc electroplating and hot dip galvanizing
I have recently reviewed a demonstration of a new very rapid surface diffusion treatment process to enhance the corrosion resistance of low carbon steel screws used for household appliance assembly applications. The treatment also provided high hardness to the screws for self drilling capabilities (no need for pilot holes in multiple layers of sheet metal, such as white goods, refrigerator and washer / dryer assemblies.) I perceive that this new process could possibly be used for enhancing the corrosion resistance of common nails (collated brads, finishing nails, framing, deck, siding and roofing nails and construction staples, etc.) These types of fasteners are currently sold either bright (untreated) finish, zinc electroplated or hot dipped galvanized. Alternatively these products are made from stainless steel (usually 304 or 316) or aluminum (or if you will aluminium). The wholesale price of electroplated zinc nails is typically about 20% to 25% greater than bright untreated nails, double hot dipped nails are priced about 35 to 40% higher than bright nails, stainless steel nails can be 250 to 350% greater than plain bright nails, so there is considerable "market value" derived from the enhanced corrosion resistance properties. Hardened nails for enhanced penetration in hard substrates such as green concrete and steel studs also have considerable added market value.
I would like to evaluate the economics of this new treatment process versus the traditional zinc coating processes. We are making arrangements for independent testing utilizing several cyclic corrosion tests primarily for seaside corrosion and acid rain exposures. Also we are testing for comparative exposures to difficult real world products such as redwood, cedar (tannin acids) and preservative treated woods (corrosive salts).
I would like to understand the primary cost factors or economics of zinc electroplating and hot dip galvanizing (HDG) for nails and small hardware goods. What are the primary costs involved in the two processes (labor, equipment capital costs (allocated via depreciation accounting), utilities, raw materials (zinc sources, cleansers, acids baths), environmental remediation processing, etc. on a per pound or ton basis. I would like to know what would be a typical range of costs per pound for high volume automated processing for zinc electroplating small fasteners and hardware goods, and specifically small and large nails (brads and finishing nails which are zinc electroplated and decking / siding / roofing nails which are usually hot dip galvanized).
Thank you for your input in this process comparison. Obviously the new process needs to "score well" both in product physical attributes as well as be suitable to the bottom line ($/lb.) if it is to have any chance in competing with the well established zinc coating processes.
- Polson, Montana, USA
2002
2002
"Surface diffusion" is a term that is vague to me. So not knowing the surface properties imparted by such a process, it is hard to compare them to the properties imparted by other processes, Dan.
Although it is usually not considered smart or logical for platers and galvanizers to quote "by the pound" because of the many other factors you allude to, many shops do it all the time. So it seems that what you could do is get a couple of quotes on the shapes you are interested in, combined with the retail prices you already have.
Despite the significant detail of the question you've posed, for which we thank you, you haven't told us what your interest is
(finishing your own parts using this process, manufacturing the equipment for the process, licensing the process out to others or from others, etc). You've told us none of the economic properties of this process while asking for the economic properties of the competitive processes. What are the primary costs involved in
your process (labor, capital costs), utilities, raw materials (zinc sources, cleansers, acids baths), environmental remediation processing, etc. on a per pound or ton basis please? Thanks, and good luck with the undertaking.
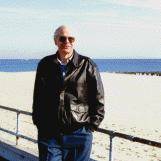
Ted Mooney, P.E.
Striving to live Aloha
(Ted is available for instant or longterm help)
finishing.com - Pine Beach, New Jersey
November 12, 2010
I am employed as the Senior Roof Technician at my company. I have 26 1/2 years on-hand experience in all phases of roofing. I am also a Master Roofing Tinsmith and Sheet Metal Mechanic. I work on the roof six days a week, sometimes in the rain.
I have extensive experience in the use of stainless, hot dipped galvanized, and electroplated roofing nails.
Our company does not use electroplated roofing nails (coil nails). We primarily work on several barrier islands and the immediate inland areas on the southeast coast of North Carolina. We constantly have high winds (20 to 60+ mph).
It has been my personal observation that gun installed electroplated roofing nails (EP Nails) deteriorate prematurely in the salt environments of the coastal regions, and other extremely wet areas of the Southeastern US, as used in the application of roofing shingles.
All roofers in this area use these nails, except my employer.
I have personally observed properly installed 5 year old 30 year warranty shingles, with a wind rating of 110 MPH, blow off roofs at less than 40 MPH after the EP nails had completely disintegrated in less than 5 years. I have personally inspected thousands of attics of homes with these nails in the roof. The nails were even rusted INSIDE the attic from the exterior moisture circulating in attics.
As a result, our company adopted a policy to only use hot dipped galvanized nails on inland homes, and only stainless on ocean front homes.
EP Nails cost around $30 per box (will install approximately 1500 square feet of shingles at six nails per shingle).
A box of hot dipped galvanized is $60, and only if you purchase a pallet--40 boxes--from an out of state distributor, and pay to ship the nails. This is what we have to do as no one locally carries these nails.
Stainless roofing nails are $150 per box, which will cover 1500 square feet. We purchase these from a distributor in South Carolina and pay shipping.
The average roof is 3000 square feet. So for an addition $60 total cost, one can install a 30 year shingle using hot dipped galvanized roofing nails and have a nail which will actually last as long as the shingles.
Roof Tech. - Leland, North Carolina, USA
Hi, Kent.
Glad to hear of your dedication and your employers dedication to using the proper nails. We have a number of threads involving complaints with roofs installed with non-galvanized nails, and it sounds like it would be a good idea for galvanized nails to be "required code" for some areas to minimize wind damage.
Regards,
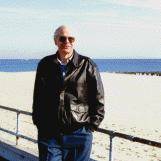
Ted Mooney, P.E.
Striving to live Aloha
(Ted is available for instant or longterm help)
finishing.com - Pine Beach, New Jersey
November 12, 2010
When I started installing roofing in the 1970's the roofing nails were exclusively hot dipped if my visual memories are correct. In 1979 I became a roofing contractor and somewhere in the early 1980's there was some talk of cheap Chinese nails. Soon it seemed that was all that was available.
Most roofers could care less as their sales pitch is limited to one word:cheap.
But you can still get double hot dipped galvanized nails loose or for coil-ated from Maze Nails. We only hand nail but offer the better nail as an upgrade. The better nail adds about $75.00 to $150.00 to the cost of most residential roofs and some people don't want it.
The reason I mention Maze is that I believe it to be the last and only manufacturer of nails from the USA. Trying to get my wholesaler to bring them in was a real effort.
Jon Wright Roofing and Siding - Irving, Texas, USA
April 2, 2011
We recently bought a house that was built 8 years ago. After strong winds, we lost a few shingles on the cedar shingle roof. A roofing contractor tells us he will have to reinstall all of the shingles and and replace all of the nails - at an estimated price of $17,000!! The roofer claims the original roofing company (now out of business) unknowingly used defective galvanized nails made in China and that they are rusting and corroding. They also claim they have seen this issue with several roofs in our area. Has anyone heard of this? Can you shed some light on it? Is there anyway I can check the nails myself to ensure replacing the nails is necessary?
Buyer - Villanova, Pennsylvania, USA
October 28, 2011
For want of a nail, a shoe was lost....
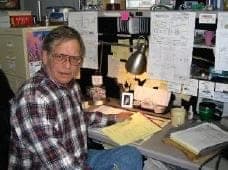
Jeffrey Holmes, CEF
Spartanburg, South Carolina
November 2, 2011
Q, A, or Comment on THIS thread -or- Start a NEW Thread