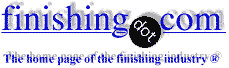
-----
Blistered Ni-P (Electroless Nickel-Phosphorous) Plating
We are experiencing problems with bubbling plating for an automotive part made from 6262 extruded. The plating is Ni-P. When the part returns from the plater we are sorting for bubbling plating on the ID. We are experiencing about an 8% fallout.
However, during our final audit, after parts sit in inventory for a short length of time, we discover more bubbled plating. Is it possible for bubbling to appear after the parts sit in inventory for a certain length of time? This is puzzling as I have checked the sorters' performance and trust they are doing a thorough job.
- St. Louis, Missouri
2002
2002
by G. G. Gawrilov
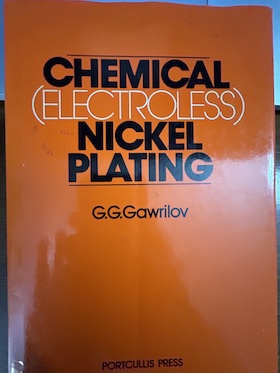
on AbeBooks
or eBay or
Amazon
(affil link)
If possible, do a low temperature bake, and catch all the bad parts the first time around.
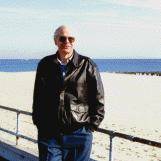
Ted Mooney, P.E.
Striving to live Aloha
(Ted can offer longterm or instant help)
finishing.com - Pine Beach, New Jersey
First of two simultaneous responses
Ken,
Yes, it is possible for bubbles to keep developing with time. Corrosion takes time to proceed and sometimes forms products that have a larger volume than the original elements (salts, gases, etc.) So, if it happens say in a pore, that was in your substrate below the impervious, thin plate, the consequence is a bubble. Remedy: Better substrate and plating quality control
Monterrey, NL, Mexico
2002
Second of two simultaneous responses
There are many parameters that control the adhesion of EN to aluminum substrates. Ignore or be unaware of just one of these parameters and you will have blisters or marginal adhesion that will lead to blistering down the road.
Todd Osmolski- Charlotte, North Carolina, USA
2002
First of two simultaneous responses2002
Adhesion testing is an imperfect science. One can sample to detect if process is flawed, however, can't inspect 100% of lot over 100% of surface of all parts to ensure lot is "blister free."
8% bubbled at receiving should be a clear signal that something with your plater's process or their chemistry or your base metal is awry. Electroless nickel, especially when it gets over a couple of tenths thick can mask poor adhesion due to the "enveloping" effect. As the EN is hard, it wraps around the part and won't lift or separate for a period of time (unless thermally or mechanically or otherwise encouraged to lift sooner!). This is what the traditional bake after EN plate is for, to induce blistering so poor or marginal adhesion becomes apparent.
There is a very good ASTM spec for preparing aluminum for plating
(either ASTM B253 or
ASTM B254 ) that has various methods. All aluminum alloys can't be treated by a single process and variations are required depending on the specific alloy you're using. In general, plating on 6000-series aluminum is less problematic than say 7000 or 2000 aluminums. Non-alkaline cleaning, minimal etching without caustic, double zincating, and barrier EN striking are some suggestions for trying.
Good luck... aluminum is at best tricky.

Milt Stevenson, Jr.
Plating shop technical manager - Syracuse, New York
Second of two simultaneous responses
You did not give info regarding your plating process but I have a feeling that you do not use a high PH EN prior to your low PH EN.
When plating on Al, it is highly recommended to use two EN solutions, a high PH one as a flash (does not attack the zincate layer) and then an ordinary EN with PH 4.8.
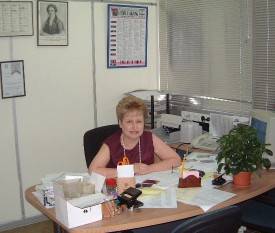

Sara Michaeli
Tel-Aviv-Yafo, Israel
2002
Q, A, or Comment on THIS thread -or- Start a NEW Thread