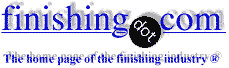
-----
Maximum Nickel Thickness for Solderability Applications
My application involves plating electroless nickel to a metallized ceramic substrate for a high-temp solderability application (300 °C). My question is: What is the maximum nickel thickness that may be applied without compromising adhesion due to the thermal expansion mismatch between the nickel and the ceramic?
Erich R [last name deleted for privacy by Editor]- Phoenix, Arizona, USA
- Is the ceramic substrate per metallized?
- Are you directly plating EN over ceramic or is there any coating / metal prior to EN?
- What is the ceramic substrate you are using Alumina / Berilya?
Basically for solderability application 3-5 micron of Nickel should be sufficient to withstand the leach test. (260"c for 1 min ). If you are building up excess thickness the metal may peel off due to internal stress. Basically for ceramic SMT components which are pre-metallized (either by thick film glass paste or epoxy pastes) you can reach a nickel thickness or 5-10 micron without any problem which should help withstand the temperature you are looking for in soldering (300'c). Good luck ..
Karthik- Singapore
...And if all else fails, use two layers of Eless Nickel Boron and sinter each one.
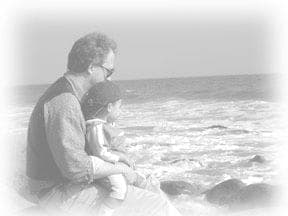
Dave Kinghorn
Chemical Engineer
SUNNYvale, California
The substrate in question is aluminum nitride, co-fired with a tungsten thick-film metallization. Two layers of NiB are applied and each layer is sintered at ~800 C. The parts then are subjected to a 1000 °C brazing operation in reducing atmosphere. Efforts to subsequently plate the substrate with electroless gold have shown poor adhesion. It is suspected that the poor adhesion is in part due to the presence of diffusion products products in the NiB deposit, therefore thicker nickel prior to brazing should result in less diffusion products at the surface. Hence the question: How thick can we go?
Erich R [last name deleted for privacy by Editor]- Phoenix, Arizona, USA
I have worked in thickfilm industry where we used to plate Nickel over thickfilm metallization and then plate solder over nickel for solderability application.
I am not very sure about the behavior of NiB at high temperatures. But I feel that 800 'c is almost the recrystallization temperature and I don't think the Ni-B will not have the same structure as they were before the heat treatment (Sintering). My assumption is that the B may get separated from the Ni at that temperature and form a layer above (I am not sure about it). Also brazing at 1000 may leave some residues on the surface of Nickel. You can do a surface analysis to check if any contaminants are present (SEM-EDX). If Boron is going to cause the problem, however thick you plate the NI-B you may get the same problem. May be a pure layer of Nickel without Boron can solve the purpose for you.
Good luck....
Karthik- Singapore
If the frit used for metallizing the ceramic is the correct one for the ceramic, and properly applied, there is no limit to the thickness of nickel. It is best to use a low stress nickel such as sulfamate with no additives, except surfactant. If electroless nickel is to be used, nickel boron would be the best suited. If pure nickel is needed, boron can be removed at 950 °C in moist atmosphere furnace. Boron hydride is formed and out gasses from the deposit. This technique is used for brazing and bonding to glass.
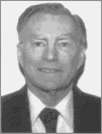
Don Baudrand
Consultant - Poulsbo, Washington
(Don is co-author of "Plating on Plastics" [on Amazon or AbeBooks affil links]
and "Plating ABS Plastics" [on Amazon or eBay or AbeBooks affil links])
Q, A, or Comment on THIS thread -or- Start a NEW Thread