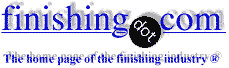
-----
Thickness Problem
Hi there guys,
WE have plating thickness problem on our products, low plating thickness problem to be exact. Here's a brief detail so you can have an idea what we have done so far, and what is the nature of our problem.
Problem Infos:
* Thickness problem is encountered on the top left portion of the strip only. ( near the belt area, we use strip-to-strip plating machine) We use XRF to measure our thickness, and we measure the strips diagonally in 3 points. First point is the top left portion, then the middle portion and third is the right bottom portion of the strip. Our sample size is three strips, and for all three strips, the thickness measurement the reading at the top left portion is below our requirement of 300 microinches. Most of the readings at the top left portion are simply 250 or less, while for the middle and right bottom portion is around 450 microinches. Our specs is 300 - 800 microinches.
* We are using High Speed Plating Machine, and MSA based plating solution.
* The problem is encountered not only on single PDIP units but as well as on Matrix type product.
* We have already checked the following items and no problems were found
- Amount of Anode - - Actual Current/Voltage reading
- Calibration of our XRF Machine
- Amount of MSA in the solution
- Solution Agitation
So far this is what we've checked hopefully you could help us determine the problem.
Thanks,
Nats Grandeza- Parañaque, Philippines
You should check efficiency of bath regularly. Busbar contacts play a role. What is the conductivity of solution? What pH do you plate? Have you callibrated your Ampere Hour meter? The speed of plating may be higher and the actual surface area might be more than your calculated. Check if any unwanted area is also getting plated. Do you keep good concentration of salts? Is temperature correct?
Payal Mag- Charlotte, North Carolina
I understand that the three measured points are on a diagonal, but there seems to be no physical significance to the 'left' in your 'top left' terminology, so I am having a hard time understanding what "top left" really means. In a continuous plating application: if the strip is vertical, I understand 'top' but don't undertand 'left'; if the strip is horizontal, I understand 'left', but don't understand 'top'.
Anyway, I doubt that the problem is solution composition. It seems geometrical, but I don't understand the geometry. Something about anode placement or solution level seems to be the problem.
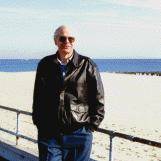
Ted Mooney, P.E.
Striving to live Aloha
(Ted is available for instant or longterm help)
finishing.com - Pine Beach, New Jersey
Kumusta kayo pare! (Ilocana asawa)
All of these high-speed leadframe Tin-Lead platers require plating cell tuning. The problem is that you mentioned you have a revolving belt type and these have very little space inside to tune them. By tuning I mean you must adjust the way the plating cell throws the current inside the belt assembly, and the way the solution emits onto the strip. For current distribution tuning, I used to do this by gluing in a Mylar or G10 sheet as an anode shield in front of the anodes but behind the apertures where the plating solution shoots out to provide agitation. Then begin punching holes in the sheet nearest to the thin section of the electroplate, and analyze results. After a bit of trial-and-error hole-punching you will have that electroplate perfectly flat. This whole procedure will depend upon you being able to get the sheet as close as possible to the plating. The farther back toward the anode, the less resolution it will offer. Also you must be careful not to block the return path of the plating solution. For agitation tuning, realize that these strip platers may have dead zones even though the pump is working. Generally, blocking the flow a bit to the thick-plated areas doesn't work well because you will lower the overall current density allowed in this way. So you must provide additional jetting of the solution to the dead zones. But before you do this, check for dead zones after the anode current has been tuned by turning the rectifier up until areas start to burn. These are the areas that "might" need additional solution jetting. If you burn way above your current density spec, then no more work on the cell is required. A well designed and tuned cell can provide in-spec plating at reaction rates approaching 70-80 microinches per second, but most store-bought strip platers can't do that.
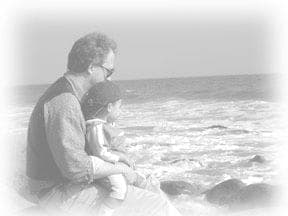
Dave Kinghorn
Chemical Engineer
SUNNYvale, California
Hi,
Do you have any shield bar between the Anode ball and belt in the plating cell? It seems that the bottom leads have HCD meanwhile the top leads LCD. I think you can try to use the shield bar to get the throwing power evenly. Hope you to can solve the problem.
Regards,
Devis Lu- China
I think that your solution or the material of your solution is not suitable. Also check the distance between anode and cathode if the conductivity or generally throwing power of solution is low the distance is very critical but you can solve this problem by adding surfectant agents for example washing agents. If you describe more about your system and your solution I can better help you.
Good wishes,
Shapour Abd Sharif Abadi- Tehran, Iran
Thickness problem may come from the distance from anode and cathode. Is there any mistakes when you put the parts on the plating bath which makes the top left part is a little bit further from anode than other sections of part? You have to check also the hanger of the anode,is the electrical current flow well for each anode?You may check it by using the portable thermometer and see whether the hanger is hot or not,if it's hot,it means that the current not flow really well.Have you done the Hull Cell ⇦ huh? test analysis?I am sure you do, Maybe you should add the substance that can increase the throwing power,in France we called it "la base",I don't know how it called in English..
Reynald- Batam Island, Indonesia
October 22, 2008
Q, A, or Comment on THIS thread -or- Start a NEW Thread