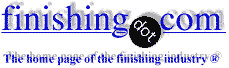
-----
Spot type seal check for black anodized aluminum
Q. Why black anodized part shows dark spot after nitric acid spot test (ASTM 136 ^ ASTM B136)? Just place a nitric acid (50% volume) drop on anodized part for 2 minutes.
- Tamilnadu [India]
September 5, 2024
Tip: This forum was created to help build camaraderie through sharing tips, opinions, pics & personalities.
The operator & those readers who want that might not engage with anonymous posters.
A. It wasn't properly sealed, and failed the test designed to indicate whether it was.
Luck & Regards,
Ted Mooney, P.E. RET
Striving to live Aloha
(Ted can offer longterm or instant help)
finishing.com - Pine Beach, New Jersey
Q. OK, But why it appears darker than anodizing colour?
vee [returning]- tamilnadu
November 13, 2024
A. Hi again,
I'm not sure why the failure of the seal test manifested as a dark spot, and don't think it matters enough to research, but I'll guess that it's because nitric acid is a very powerful oxidizing agent, and the dye, being organic, was oxidized by it.
Luck & Regards,
Ted Mooney, P.E. RET
Striving to live Aloha
(Ted can offer longterm or instant help)
finishing.com - Pine Beach, New Jersey
⇩ Related postings, oldest first ⇩
Q. I'm looking for a spot type seal check for dyed anodized aluminum. For years we have used 50% nitric acid for 2 minutes and check for any loss of color. This has proved adequate as a qualitative test. However, I can't find any references for this test and I figure I should use something that is documented somewhere as we are updating our quality system in preparation for a NADCAP audit. Any help would be appreciated.
Guy Lesterplating Co. - Ontario, California, USA
2002
![]() |
RECOMMENDED ANODIZING & CHROMATING BOOKS
for Shops, Specifiers & Engineers ![]() avail from eBay, AbeBooks, or Amazon ![]() avail from eBay, AbeBooks, or Amazon ![]() avail from eBay, AbeBooks, or Amazon ![]() avail from eBay, AbeBooks, or Amazon ![]() avail from eBay or Amazon (as an Amazon Associate & eBay Partner, we earn from qualifying purchases) A. Hi Guy (very poetic, aren't I), The test you are referring to is an ASTM test ... but for the life of me, I can't remember the test #. I'll try to remember to look it up tomorrow. Its referred to as a "dye stain test" Actually.. the test also requires (for clear anodizing) a small drop of blue dye to be applied after the nitric is rinsed off, and then to check for absorption of the blue dye. Some pumicing of the test area is also permitted. ![]() Marc Green anodizer - Boise, Idaho A. ASTM B136 is an anodize seal integrity test which the first step is using nitric acid. Get a copy of that spec from ASTM. ![]() Milt Stevenson, Jr. Plating shop technical manager - Syracuse, New York A. Your documentation lies in ASTM B136 (Re-approved 1998) Standard Method for Measurement of Stain Resistance of Anodic Coatings on Aluminum. This standard contains the Nitric Spot test and also the Dye Stain test. The specification may be ordered directly from ASTM. Best of Luck. Ira Donovan, M.S.F.Kansas City, Missouri A. It is well sealed if: (1) it will not gain weight if retreated in the seal (2) it becomes resistant to staining by dyes (3) electrical resistance is increased (4) electrical "impedance" is increased Dye Stain is covered in ASTM B136, that is what you have been doing with nitric acid Acid Dissolution is covered in ASTM B680, a phosphoric acid system. Kape Test. Sodium Sulfite Bleach - Sodium Hypochlorite ⇦ bleach/sodium hypochlorite in bulk on eBay or Amazon [affil link] Salt Spray ASTM ASTM B117, mainly for overall corrosion Impedance Test ASTM B457 (Instrumentation commercially available) Based on the fact that impedance of the anodic oxide increases with the "degree" of sealing. CASS ASTM B368, really just a corrosion test. Take two aspirin and call me in the morning. ![]() Robert H Probert Robert H Probert Technical Services ![]() Garner, North Carolina ![]() |
Multiple threads merged: please forgive chronology errors and repetition 🙂
Q. I am a quality control manager working with type II anodizing for the first time. Some of our parts, after being in the field for three months or so, get a lighter color to them going from their original black to a brownish orange color. I believe the problem to be ultra-violet bleaching and I know that it is from a problem in the anodizing process. Is there a cheap and easy to perform test that would readily find the defective anodizing?
Kenneth J. Winward- Kennewick, Washington, U.S.A.
2002
![]() |
A. The problem is more likely with the sealing than with the actual anodizing (although it is also possible that a poor quality dye was used, the sealing issue is more likely). ASTM B136 describes a dye stain test to use to check seal quality on a pass/fail basis. The test requires Nitric Acid (40%) for two minutes and blue dye for 5 minutes, if there is a color change the parts fail (check out the spec for more detailed instructions, make sure to rinse and dry the part in between steps). Jim GorsichCompton, California, USA A. Use the dye stain test on your parts.. its a very easy one. All it takes (in the case of dyed parts) is a 50% (vol) solution of nitric acid. Place a drop on the surface, and allow it to remain there for 2 min. Rinse thoroughly. If a spot remains after rinsing, the part is not sealed adequately, which is what I suspect the problem may be. In the case of clear (natural, for the purists out there) anodizing, one would follow up the nitric acid with a drop of Blue 2LW dye for a period of 5 min, followed by a rinse. If the blue spot remains..then, once again the part has failed. Abrading the spot with pumice ⇦ on eBay or Amazon [affil link] is allowed in both tests. If the spot does not show after a light pumicing, then it has passed. ![]() Marc Green anodizer - Boise, Idaho |
Multiple threads merged: please forgive chronology errors and repetition 🙂
Anodic coating sealing tests
Q. How can someone find out if anodic coating has been sealed and what kind of sealing (sodium dichromate, water, etc). Is there a method or a MIL-STD for testing the coating? I will appreciate a quick answer.
Keren Poran-Avrahamiaviation products - Gilon, Misgav, Israel
2003
A. A sodium dichromate seal imparts that characteristic amber yellow color usually associated with hexavalent chrome, and nothing else does, so you should see that by eye. But there is an ASTM "Seal Quality Test" although I don't remember the spec number off hand.
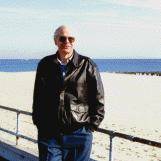
Ted Mooney, P.E.
Striving to live Aloha
(Ted can offer longterm or instant help)
finishing.com - Pine Beach, New Jersey
A. The standard that Ted mentioned is ASTM B680 Standard Test Method for Seal Quality of Anodic Coatings on Aluminum by Acid Dissolution. You can obtain this standard directly from ASTM.
Toby Padfield- Troy, Michigan
A. Acid Dissolution Test - ASTM B680
Impedance Test - ASTM B457
Dye Stain Test - ASTM B136
Just splash some different color dye onto the surface, then rinse if off. If all the color completely washes off - it is at least partially sealed.
Wipe with acetone ⇦ on eBay or Amazon [affil link] Warning! Flammable! , if the swab picks up color, then it is NOT sealed.
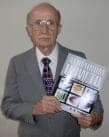
Robert H Probert
Robert H Probert Technical Services

Garner, North Carolina
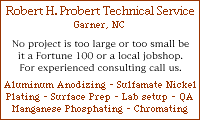
A. I believe the "dye stain" test also requires a drop of 50% nitric acid solution to be placed on the part for a period of time (2 minutes, if I recall), prior to placing dye (preferably Blue 2LW, or its equivalent, for 5 minutes) on the part. This test also allows a "pumicing" of the test area after the dye is rinsed off. This is by far the most common method of testing seal quality, as most job shops aren't going to drop $20k or more on E.I.S.(electrochemical impedance spectrography) equipment.
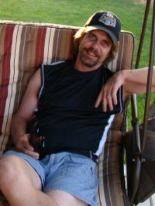
Marc Green
anodizer - Boise, Idaho
Isn't that just like Marc to go and get all practical on us :-)
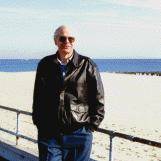
Ted Mooney, P.E.
Striving to live Aloha
(Ted can offer longterm or instant help)
finishing.com - Pine Beach, New Jersey
Multiple threads merged: please forgive chronology errors and repetition 🙂
Testing a Hardcoat Anodize Seal
Q. We have a customer that requires a sealed Type III hardcoat anodize coating. We are using boiling DI water to accomplish this, and testing the seal using ASTM B136. Our problem is that our customer is testing incoming parts using a black permanent marker. They let the permanent ink sit on the surface for 1 - 2 minutes, then use an acetone-based nail polish remover to try and rub it off. If all the ink does not come off they reject the parts. Our stance is that if it passes the ASTM test it is a good part. Does anyone have any insight into using a permanent marker for a seal test?
Jennifer MassePlating Shop Employee - Buffalo, New York
September 18, 2008
A. Jennifer
You do not say if you pass your customer's test sometimes or at all. If you pass only sometimes, you could have a process control issue. If you never pass, the test could be suspect.
However, if your customer has developed this test as acceptance criteria, you are stuck with it unless you can convince them that the B136 test is more appropriate. Even then, if I recall correctly, the test allows for variations in the test to simulate specific conditions.
- Colorado Springs Colorado
A. I have ever been asked to do the same seal test and never failed as long as it is acetone based. Even we passed a test requested by one customer using DI water.
John Hu- Singapore
Q. Thanks for the response. We have had parts that pass the ASTM test but absorb some of the permanent marker (maybe about 10% of the area being tested shows black dye). We don't have an issue with testing or certifying to any standardized test the customer wants, but I cannot find anything that backs up a magic marker test.
Jennifer Masse [returning]- Buffalo, New York
A. Hi Jennifer. I'm not familiar with that test. To the contrary, I know customers who have asked for permanent markers to be used to touch up rack marks -- precisely because it won't wash off.
A 'permanent marker / laundry maker' is not the same thing at all as a water-soluble dye, and will even permanently mark chrome and glass, let alone aluminum. I think the idea behind alcohol-based dyes is that they will never come off with water, only alcohol, and even then they're certainly not guaranteed to come off 100%. Further, acetone is not ethanol and although it may sometimes remove ethanol-based dyes, perhaps it won't always do so 100%; a test which requires removing a marking which has been placed there with a marker designed to permanently, robustly and non-removably mark it strikes me as a kludge which should be replaced by one of the standardized tests.
In fact it strikes me as a bit ridiculous because the companies making permanent markers are presumably hard at work trying to make sure all attempts at removal will fail :-)
Luck & Regards,
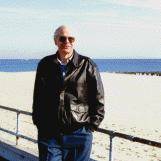
Ted Mooney, P.E.
Striving to live Aloha
(Ted can offer longterm or instant help)
finishing.com - Pine Beach, New Jersey
ASTM B136 pass or fail?
Q. Please see photos and would like to know if this is a pass or fail?
- Phoenix, Arizona
August 12, 2020
A. Looks like a fail to me. Per ASTM B136 requirements sec. 5.2 Interpretation - there shall be no visible change in the color of the coating from the action of the test.
Taylor Clarke- Minden, Nevada

Q, A, or Comment on THIS thread -or- Start a NEW Thread