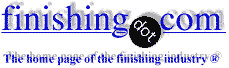
-----
High frequency pulse plating
I am trying to use high frequencies (400kHz to >1MHz) in pulse plating copper. I am trying to understand the behavior of the system under these conditions - what should I expect.
Thank you for your help.
Rahul Jairath- San Jose, California, USA
Hi Rahul. I wouldn't expect much! How far can an ion move in a half cycle of .5 to 1.25 microseconds? I think much lower frequencies will be required. Good luck.
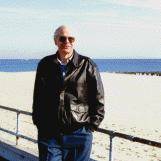
Ted Mooney, P.E.
Striving to live Aloha
(Ted is available for instant or longterm help)
finishing.com - Pine Beach, New Jersey
Consult the pulse plate literature for your answers. In particular, the Journal of the Electrochemical Society has had scores of articles published on this subject. They go back to 1909, when the first treatise on this subject was published in the Journal of Physical Chemistry.
Pulse plating bears unique results not achievable under other circumstances only when other bath conditions support the technique. Much of it depends on the quality of the power supply. Does it actually square-wave pulse, or does it just throw a lot of DC noise down the line? Even high quality supplies can end up doing that when you request the impossible. As you go higher and higher in frequency, do you loose your duty cycle? Many of these types of things are bath and workpiece dependent, because the power supply doesn't see a plating bath...it just sees an unusual load with a bit of capacitance character. This type of load doesn't usually cooperate with high frequency. And the larger the workpiece, the worse everything becomes. Lastly, molecules within the surface boundary layer move predictable distances in predictable times. We pulse plate in such a way that the gradient of metal concentration within the boundary layer never pulls down to its steady state(DC)slope. The time for this event is governed by the pulse peak current density, and the Boundary layer thickness. Therefore, at any given current density, the boundary layer thickness will determine the range of applicability of pulse frequency. To the cathode, low frequency looks like merely intermittent DC, while high frequency just looks like noisy DC. So to get anything meaningful, you must match the pulse frequency to the boundary layer thickness. This will be unique for every reactor.
There was an article published on this subject about 12-15 years ago by the Aerojet company. They reported loss of deposit at a high frequency but didn't pursue the cause. I would surmise that the most likely cause of this loss of deposit was the power supply not being able to deliver clean power at the very high frequency into that load. But if you are REALLY interested in this topic, I would recommend hooking up with ChemE Prof active in the Electrochemical Society, and discuss the project a bit. I've always been curious to find out if fundamental time constants for electrochemical reactions could be determined in this manner.
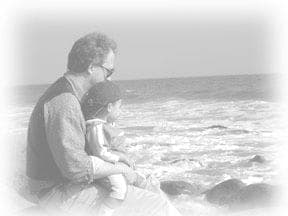
Dave Kinghorn
Chemical Engineer
SUNNYvale, California
I worked on P.R. and pulse plating with my own power supplies. For cyanide copper plating I found that the capacitance effect of the system was so big that voltage trace across the tank appeared as almost steady D.C. beyond 500 Hz.
Vijay Deval- Maharashtra, India
Q, A, or Comment on THIS thread -or- Start a NEW Thread