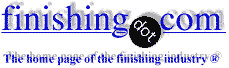
-----
Plating on TiW
Dear Sir,
If I want to plate Ni on TiW(Ti5%, W95%) what is the activation chemical. This is because the adhesion Ni on Ti is not good, there is peeling after TiW etching in H2O2. If Cu strike will be good before TiW plating without activation. If yes what is the thickness. Currently the TiW thickness about 50nm.
Thanks,
Teo Soon Cheong- Singapore
If this is Electroless Nickel plating ovet a patterned TiW Sputter/Evaporate deposit for Interconnect metallization leading to a Flip-Chip or a Wire Bond pad, forget it. It will NEVER adhere properly. You must finish the vacuum steps off with a readilly plateable metal such as Copper, Nickel, Palladium, Gold, Platinum, or some engineered alloy. Aluminum can be used if you can tolerate > 1 Micron thickness. If this is a blanket deposit such as those used in the lowK/Copper interconnect programs, you have a chance. The 95/5 W/Ti as it comes from the vacuum process is sparingly passivated as it is transported to the plating line. Place directly in a Fluoride bearing activator. There are many formulations available from plating suppliers. Next go live into a Nickel Fluoborate strike bath and build up at least another 50nM. If you have to build thickness and can't tolerate tensile stress, go live into Nickel Sulfamate after rinsing the Fluoborate electrolyte off in the Sulfamate dragout. Run the Boric at saturation, pH = 4.2, and don't exceed 10 ASF even on pulses.
Hope this helps...
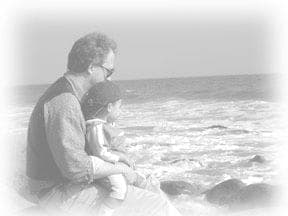
Dave Kinghorn
Chemical Engineer
SUNNYvale, California
Q, A, or Comment on THIS thread -or- Start a NEW Thread