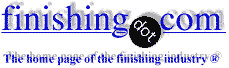
-----
Metallographic cross section of diffused Ni-Cd plating?
Can anyone tell me what I should see on a metallographic cross section of a part plated with diffused Ni-Cd? Should I see two distinct layers (cadmium over nickel) or a single alloy layer? Should I see a coating thickness approximately equal to the sum of the two original layers, or a different thickness? How else should I try to establish whether or not the plating was properly diffused? Any comments appreciated.
John E. UllmanIndiana
1998
1998
The diffusion process may consume all or both of the two original metal layers. A quick review of the Cd-Ni phase diagram will tell you what you may see in your metallographic section. You will see remaining layers of nickel and/or cadmium metal if the diffusion process has not completely diffused both coating layers together. If diffusion has occurred you may or may not see remnants of the original metal layers depending on how much the two layers have interdiffused. You may also see multiple alloyed layers, for each of the solid solutions and intermetallic phases that are stable at ambient temperature. Sorry, I don't have that diagram available to be more specific. The final thickness will depend on the relative volumes of the original metals and the phases formed.
Hope this helps.
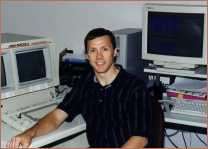
Larry Hanke
Minneapolis, Minnesota
I appreciate Mr. Hanke's well-reasoned response, but I had hoped to hear what typically occurs, rather than what might theoretically occur in the process (which I'd like to think I could dimly understand in the first place). Since I first posted, I have obtained a sample which was claimed to have been properly diffused, and which proved to have two distinct plating layers which looked very much like plain Ni and Cd, and which were about as thick as they must have been before the diffusion treatment.
I have reviewed AMS2416 and found some interesting references to the subject. The plating thicknesses are to be verified prior to subsequent processing. One could infer that this restriction must have been necessitated by the "fact" that interdiffusion alters the thicknesses of the individual layers, however, my observation of very little alteration seems to show the opposite. Also in AMS2416 is a requirement to test the diffused coating at high temperatures (700-1000 °F), looking for balling up, cracks, and blisters. This is the proof of the pudding - if significant interdiffusion has not taken place, the cadmium layer will flow.
I'd still like to hear, from anyone who has worked with this coating, about typical observations, the degree of interdiffusion which is effective, and any way to evaluate the coating without baking parts. What about SEM/EDS analyses? Any useful chemical spot test? Thanks in advance.
John E. Ullman- Indiana
1998
I, too, was hoping for a response from someone with direct experience with diffused Ni-CD, but when none came thought that my response might elicit more discussion.
Regarding your interest in a spot test - I think that you could perform a simple spot test that would detect metallic cadmium on the surface. We have done a similar test for free tin on a diffused coating of tin over copper. The objective is to find a solution that will dissolve cadmium, but not nickel or Ni-Cd intermetallics. Most intermetallics are pretty corrosion resistant, so the reagent could be pretty simple - maybe even dilute hydrochloric acid or some modification of any of the other reagents for stripping Cd plating. For the tin, we used a hydrochloric acid solution with an organic inhibitor.
Your suggestion of SEM/EDS analysis may be valid if the coating layers are thick enough. If the layers are at least a few microns thick, good metallographic cross sections examined by SEM/EDS will provide information about interdiffusion as well as layer thicknesses. Backscatteredn imaging and/or EDS line analysis would be good. SEM examination would also be a good method for verification of your spot testing.
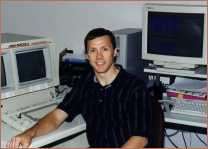
Larry Hanke
Minneapolis, Minnesota
1997
1998
I hesitated to answer because it was so long ago. Assuming you have a relatively thick nickel and cad layer, diffusion is going to be a factor of time and temperature. What we got, using crude metallographic equipment, was a layer of nickel on the substrate and a layer of cad on the top and a layer of mixed in the middle. Etch is a bitch, because most simple etches attack the cad more than the nickel.
It would follow, that a relatively thin layer of each would be totally or very nearly totally diffused.
Pratt and whitney has a spec for Ni-cad and a very qualified met lab. You might try begging them for a little history.
SEM only reads the surface. Talk to an XRF vendor to see what they have to say about their toys capabilities, since they can go to the metal surface. A toy that I could never afford.
James Watts- Navarre, Florida
The cross-section will not reveal a fine boundary between the layers after significant diffusion. However, if there is a staining method for cross-sections, it could give you an approximate idea where you stand in relation to the remaining pure metal layers. I am aware that there are staining methods for each metal.
After all the discussion above, it comes down to the question, how much are you willing to investigate and pay for the analysis. If I recall correctly, there are two techniques that will help if you are willing to spend about $1,000 to $5,000. One is Auger (pronounced O'jay) and the other is ESCA. In the Auger, the atoms are removed layer by layer and composition of elements is measured layer by layer. It will give you a composition profile vs. depth. The ESCA does it similarly, but measures compositions of compounds, etc.
However, there may be a simpler way without cross sectioning in which you chemically dissolve the alloy uniformly for both metals, layer by layer. Then measure the thickness, and do the x-ray/EDS. Now you will have a depth profile.
Mandar Sunthankar- Fort Collins, Colorado
1998
As a practical matter, in most instances you should see a definite two layer coating under 400 to 600 magnification.If, after polishing the layers are not distinct, etch the specimen in 15-25% HCl for 2-5 seconds. This will slightly etch the cadmium but not the nickel.If you still have difficulty viewing the interface, try directing your light source at an oblique angle to the specimen surface-often this will show the interface well.
Kent BackusFort Worth, Texas, USA
1998
July 31, 2009
Nickel-Cadmium Diffuse
There is not much mentioned online, or have to pay for papers.
Have been working to determine if the Ni-Cd diffuse process leaves one, two or three layers.
I have been working on microsection samples and then followed with SEM-EDS to map.
So far this process depends on the type of plating equipment used,
"Rack vs Barrel" plating. Plating thickness from rack vs barrel can confuse the diffuse process , if plating thicknesses are not consistent.
So far analysis shows two layers after diffusion process but cadmium can become brittle due to the heat applied during the diffusion process.
However, I am finding a third layer between the cadmium and nickel layer after etching samples. The layer can vary in thickness from less than 5 microinches to 35 microinches.
- Tucson, Arizona
My name is Armando. I been working on this process to determine what nickel-cadmium diffuse deposit looks like in a cross-section. Does anyone have a photo of this to share? I have googled this to death with no luck!
Armando
Plating guy - Tucson, Arizona USA
August 15, 2009
September 30, 2009
This question appears to have languished for some time without a complete answer. Working with Ni-Cd coatings on a regular basis, I thought the following post might help rectify the situation.
In x-section, Ni-Cd typically looks to be a 2-layer coating before or after diffusion. Post-diffusion SEM and microprobe analyses will show that the underlying nickel layer remains essentially pure nickel while the outer cadmium layer has become a nickel cadmium alloy.
The cause of this is that Cd diffusivity into nickel is near zero while the diffusivity of Ni into Cd is relatively high. Essentially, Ni-Cd diffusion (30 minutes at 630 °F per AMS2416) entails movement of nickel atoms into the cadmium layer and little or no reciprocal movement by cadmium atoms into the nickel layer.
Once diffused, the outer cadmium layer can withstand temperatures to
1000degF and above without melting because it has been infused with nickel -- check the nickel-cadmium phase diagram to see how little nickel is need to significantly elevate the melting point.
Standard mount & polish methods are adequate to create suitable x-sectioned Ni-Cd samples -- in my experience, etching is never required. Typical Ni-Cd coatings are ~0.5 mil (~12 um) nickel overplated with ~0.2 mil (~5 um) Cd -- a typical call-out would be
0.4-0.7 mil Ni followed by 0.1-0.3 mil Cd. Coatings in this thickness range are easily imaged at 500x.
I could post a whole set of picture here if I knew how...surprised to find that Google falls short....
For now -- hope this helps,
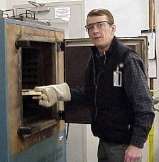
Thomas Hanlon, Materials Engineer
aerospace finishing - East Hartford, Connecticut, USA
September 30, 2009
Regarding Armando's 3-layer coating: I think what is being seen is a layer of nickel next to the substrate, then a layer of interdiffused Ni-Cd and then on/at the surface is a layer of cad-oxide. How does this occur?
If the plated cadmium layer is over a certain thickness (>~0.4 mil), the extreme outer portion of the cad layer has a tendancy to oxidize during diffusion leaving a thin, (sometimes) poorly adherent layer of (primarily) CdO at the surface. I have received samples that appear to have layer of "rice paper" spalling from the surface but once x-sectioned & mounted, the standard 2-layer morphology was revealed.
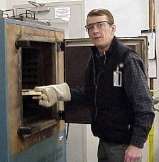
Thomas Hanlon, Materials Engineer
aerospace finishing - East Hartford, Connecticut, USA
September 20, 2010
Mr. Hanlon,
Does chromating, as a conversion coating, after Nickel-Cadmium plating make a difference in corrosion protection on Alloy steel such as H11 material or CRES such as 17-4PH material?
Thanks,
Aerospace Engineer - Seattle, Washington USA
I assume you refer to nickel plating followed by cadmium plating then heat diffusion. Chromating the cadmium before heat-treat is required. After heat treating, clean the surface and re-chromate to add a little more corrosion protection.
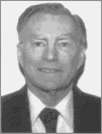
Don Baudrand
Consultant - Poulsbo, Washington
(Don is co-author of "Plating on Plastics" [on Amazon or AbeBooks affil links]
and "Plating ABS Plastics" [on Amazon or eBay or AbeBooks affil links])
September 25, 2010
Q, A, or Comment on THIS thread -or- Start a NEW Thread