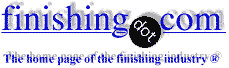
-----
Electroless Nickel Plating of Brass: Q&A, Problems & Solutions
Q. Electroless nickel plating brass? Will this contaminate the electroless nickel plating bath normally used for steel?
Robert Sachs- Morrisburg, Ont, CANADA
2001
QUICKSTART:
One way to get metal plating onto objects is to electroplate them, i.e., make them the cathode in a circuit so that the negative charge on them attracts the positively charged metal ions in solution and reduces the ions into a metal coating on the parts.
Another way is "immersion plating" of a more noble material onto a less noble substrate. This is seen in chemistry class as copper sulphate
⇦ on
eBay or
Amazon [affil link] depositing a copper layer on iron nails, or silver nitrate depositing a silver layer onto copper. These and a few other "immersion plating" processes are used in commerce and industry.
But a third way is called "electroless plating" or "autocatalytic plating". In this approach the plating solution contains a reducing agent so it is sort of spring-loaded to deposit metal on the parts. All it is waiting for is the presence of a catalyst. For electroless nickel plating baths, steel is such a catalyst, as is the nickel plating itself (hence "autocatalytic"). But copper is not a catalyst for electroless nickel, and thus must be "jump started" in one of the ways described. Once it has been started the nickel plating serves as the catalyst for ongoing plating.
A. No, but copper alloys require catalytic activation in EN bath. Otherwise, maybe, because you may see some immersion plating.
Mary Ross- Oklahoma City, Oklahoma
2001
2001
A. Copper is not catalytic in electroless nickel so it needs 'jump starting'.
Our normal method is we have an old steel anode cage (the expanded metal give high surface to volume ratio) we put in the tank first and hold the parts against to get them plating (strange this but you only have to do one wire on a bar and all the parts go).
Other methods - nickel strike in electrolytic bath like stainless steels are treated.
Use electricity like a normal plating bath to jump start the work.
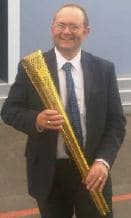
Martin Trigg-Hogarth
surface treatment shop - Stroud, Glos, England
A. Dear Robert:
If you process a large volume of parts and some of them do not start right away by any of the mentioned methods, or worse, if some parts happen to drop inadvertently in the bath (which is not unusual for large volume operations) the electroless chemistry will dissolve bronze and get contaminated. Then I would recommend another bath for these parts.
Guillermo MarrufoMonterrey, NL, Mexico
2001
Poor/inconsistent electroless nickel adhesion on leaded brass
Q. Can brass be electroless nickel plated by adding a small quantity of steel to start by galvanic. Or is DC current required, and what voltage or amperage, parts negative? Surface preparation is simply alkaline followed by acid cleaning sufficient or can a low % sulfuric acid be used. What is the best method?
Robert Sachs [returning]- Morrisburg, Ontario, Canada
2002
2002
A.
- add some aluminum or iron wires
- catalyze with a solution of palladium chloride
- electrochemical nickel strike (Watts or Wood's nickel)


Tom Pullizzi
Falls Township, Pennsylvania
2002
Q. I am attempting to electroless nickel plate low lead content Brass. The parts are small pins. The electroless nickel is a mid phosphorous.
I have had some success to date with alkaline cleaning, followed by acid clean then plating with a small quantity of steel to initiate plating. The problem is to get good plating adherence to the brass and to be ductile enough to withstand crimping of the part following plating. Would better adhesion be acquired with the use of DC current at the electroless plating to initiate the plating?
Is there a specific process that can help?
Can a Wood's nickel strike be used prior to electroless nickel and will this give better adhesion and ductility?
If the brass is nickel plated will a low temperature heat treat of say 450 °F improve adherence and ductility?
I Thank you and look forward to your comments.
Robert Sachs [returning]- Ontario, Canada
A. Mr. Robert Sachs,
To answer part of your question, may I suggest Wood's Nickel strike followed by Electroless Nickel. I have seen it done on small diameter brass tubes (0.5 mm to 1.0 mm) x 10 to 20 mm length used in the manufacture of contact probes. The parts go through some crimping process on the tubes and may exhibit much better adhesion than what you are actually doing now. Adhesion problem does crop up once in a while, though.
Good Luck!
SK Cheah- Hong Kong
2002
A. Robert:
Lead, even in very small amounts, will have a detrimental impact on the adhesion of the electroless nickel to the brass. A nickel strike is strongly recommended prior to EN plate. Use of a nickel strike would also eliminate the need to use current or other methods to initiate the EN plate. Sulfamate is preferred because it is usually more ductile and is more compatible with EN baths, but Watts or Wood's will also work. Also, avoid sulfuric acid and high current anodic electrocleaning in the pre-plate cycle.
If your pretreatment is adequate and you still experience adhesion issues during the crimping operation, you may want to try running your EN bath at a lower pH to maximize the %P in the deposit. Generally speaking high phosphorous EN deposits are a bit more ductile than those from mid phosphorous baths (check with your vendor for specific values).
Hope this helps!
Mike Barnstead- Waterbury, Connecticut
2002
Multiple threads merged: please forgive chronology errors and repetition 🙂
Electroless nickel plating on brass per ASM 2404, class 2 -- advantages/disadvantages of post plating heat treatment
I have brass parts that require electroless nickel plating for corrosion resistant. AMS2404, class 2 requires post plating heat treatment for harden the deposit. Do I actually get better adhesion of nickel by specifying class 2? What are the advantages and disadvantages between class 1 and class 2 EN on brass?
Norm Danginstrument co. - Santa Ana, California, USA
2005
2005
A. Hardening electroless nickel coatings will severely reduce their corrosion resistance and may cause the coating to crack. However, it will improve adhesion.
Ron Duncan [deceased]
- LaVergne, Tennessee
It is our sad duty to note Ron's passing on Dec. 15, 2006. A brief obituary opens
Episode 13 of our Podcast.
Preparing a brass substrate for electroless nickel plating
Q. We have to plate electroless nickel (8-12% phosphorous) over pure zinc for a coaxial switch. I want to know how I can prepare the substrate prior to electroless nickel plating. Thanks!
Teresita Molinarelays - Hawthorne, California
2005
A. Regular cleaning cycle used for plating on zinc or brass. Then, a strike of a high pH EN, then regular high phosphorous EN.
Guillermo MarrufoMonterrey, NL, Mexico
2005
2005
A. Or alternatively, you can use a copper cyanide strike prior to the high phosphorous EN.
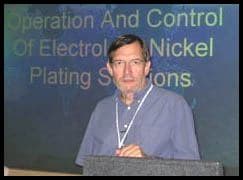
Ron Duncan [deceased]
- LaVergne, Tennessee
It is our sad duty to note Ron's passing on Dec. 15, 2006. A brief obituary opens Episode 13 of our Podcast.
A. You need to chemical polish the brass first.
- give a quick copper flash
- quick layer of watts nickel
- then into ENP
- East Sussex, England
2005
A. To be on the safe side, you need a nickel strike prior to the EN.
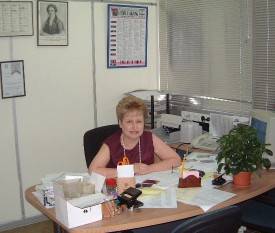

Sara Michaeli
Tel-Aviv-Yafo, Israel
2005
Low Phosphorous EN Nickel on brass
2005I am currently working on a valve mechanism made from UNS C36000 Brass. The Brass component comes into contact with some 440C bearings (~60 HRC). After some life testing we're seeing some slight wear issues....nothing to be detrimental to the use of the product yet but we're trying to minimize it just in case. The first attempt was with unplated brass...we'd like to stick to the brass to keep machining costs down (And also for compatibility reasons), so rather than moving to a harder material there I'd like to try plating it first.
I was reading here that 1-3% or 2-4% Phosphorous EN is being used sometimes as a replacement for electrolytic hard chrome. Getting to the question...what kind of thicknesses and tolerances on the thicknesses are recommended to get reasonable wear resistance with this type of EN? I'm used to doing plating's that are less than .001" thick but I doubt that will cut it in this case. Would specifying a thickness >.001" that's still held to a tolerance of a few ten-thousandths be reasonable? e.g.: .0010"-.0013" thick or .0030"-.0033" thick. Are the 1-3% Phosphorous platings significantly better or worse for wear purposes than the 2-4% platings?
The part in question does have external threads on it that I'd like to avoid masking (To keep cost down). Would any adhesion issues to the threads be anticipated? If so, is there anything I can specify to mitigate that.
Right now the callout I was thinking to try first is: Electroless Nickel per ASTM B733-04 SC3, Type II (or I?), Class 2, .0010-.0013 Thick. Then if needed maybe: Electroless Nickel per ASTM B733 -04 SC4, Type II (or I?), Class 2, .0030-.0033 Thick.
Biomedical - Chatsworth, California, USA
by G. G. Gawrilov
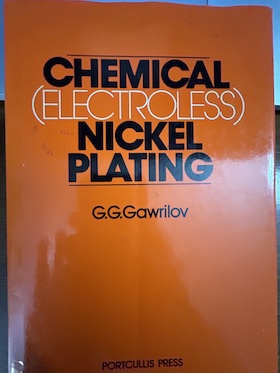
on AbeBooks
or eBay or
Amazon
(affil link)
A. The following is opinion only!
I would start by looking for a harder brass alloy.
EN is quite controllable by a good operator with good equipment and a good solution. Completely uniform plating above 0.0015 gets to be tricky as well as expensive, so I would start with that and see how well it works.
Your external threads will have to be cut undersize to accommodate the thickness on each side of the same thread. It will help if you truncate the thread a little more-say 75% vs. an 80% thread. You probably can avoid masking, but masking does not have to be expensive.
- Navarre, Florida
2005
A. Too many questions for a free ride Matthew, don't you think? But there go my two cents.
Chrome is harder and easier to adhere to brass than any EN but it's not uniform specially on threads. Three tenths is tight but feasible for EN. Now, how much wear can the mechanism tolerate before being non-useful? You said you are used to plating less than 1 mil and there must be a reason. There is no need to specify 3 or more mils if 1 or 2 mils will scrap the part.
Monterrey, NL, Mexico
2005
2005
A. Your proposed thickness of 0.0010 - 0.0013 inch should be adequate. The EN will either be successful or not in this application. If it is not successful, a higher thickness will not help.
EN with 4% Phosphorousl is slightly harder and more wear resistant than lower (or higher) phosphorus contents and would be best for your application.
Alloy C36000 contains 3% lead, which can create an adhesion problem. EN will stick to it, but only if the lead is completely removed. Plating threads increases their pitch diameter by four times the thickness of the coating.
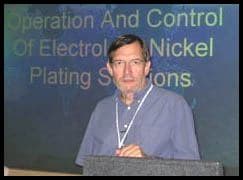
Ron Duncan [deceased]
- LaVergne, Tennessee
It is our sad duty to note Ron's passing on Dec. 15, 2006. A brief obituary opens Episode 13 of our Podcast.
Q. James-
We're actually in a bit of a stranglehold when it comes to material. Right now to guarantee we pass our validation procedures with minimal risk we either have to stick with the brass alloy we have or make the jump to a 300 or 400 series SST that we've previously validated in our media...and that would kill our machining costs. I wish we could just go with the SST but I'm right on the line for my budget as is. I think I'll try to stay below .0015 like you suggested, maybe .0012-.0015.
Guillermo-
The reason I usually plate less than .001" is because it's usually just for slight corrosion resistance and not for wear....just to avoid oxidation of the brass for aesthetic purposes. This is my first time actually using EN for wear purposes. A few thousandths of wear won't kill us, we just have to start out with tighter tolerances initially to guarantee that we'll still be in tolerance after X number of cycles...which is why I want to keep the plating tolerance fairly tight. Right now, without the plating, we *might* not run into any issues during the number of cycles expected during our warranty period, but I hope to reduce the wear rate enough with the plating that it shouldn't be an issue until well after the warranty period has expired.
- Chatsworth, California, USA
2005
Q. Let me know the process sequence with complete chemical and process details for Electroless Nickel plate of 25 microns on Copper alloy (C36000 Brass) according to ASTM B733 standard.
Karthikeyan Krishnamoorthyproduct designer - Coimbatore, India
November 1, 2014
A. Hi Karthikeyan. First step is you need to buy a copy of ASTM B733 if you don't have one; it's internationally copyrighted, and you can't specify it or certify compliance with it unless you have a copy.
Although I doubt that anyone (except a plating consultant you retain) can provide you with the right and full cycle of treatment for your situation, there's an awful lot on information on this page which people will probably be happy to clarify for you. Some things you'll need to determine are why you are applying electroless nickel, because that will help determine whether you need high, low, or mid phosphorous, and whether it needs heat treatment. You'll also have to think about this issue of reliably "jump starting" the plating, and whether an electrolytic nickel strike should precede the EN process, and as Ron Duncan warned us, what you are going to do about the lead in the C36000. Best of luck.
Regards,
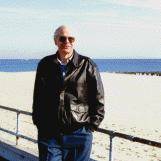
Ted Mooney, P.E.
Striving to live Aloha
(Ted can offer longterm or instant help)
finishing.com - Pine Beach, New Jersey
November 2014

Q, A, or Comment on THIS thread -or- Start a NEW Thread