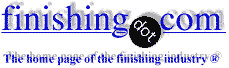
-----
Solder plating
I have the nodule problem at solder plating process. I use Methane sulfonic acid (MSA) and tin/lead ratio 60/40. After check all chemical parameter, it's under specification . The plating area is 1.2 square foot . I use 13 A, 250 amp-min to get the thickness around 400-500 microinches and this is flexible circuit. I don't know what's wrong . Even reduce the current, amp-min, more cleaning time and concentration,and more microetching , I still found nodule 2-5 % .
It would be very appreciated for your recommendation.
Miss Passawee Reaungart- Lamphun, Thailand
In MSA baths, the Tin(Stannous) usually falls under spec fast due to oxidation to Stannate. Lead does not suffer this rapid falloff. The oxidized Stannate usually can be found as a sludge on the bottom of the tank or a bit in the filters, but usually its particle size is too small for normal filters. I used to use two Tin baths. One would be in reserve in a settling tank while the Stannate settled to the bottom, while the other was in use. At the end of the day I would swap them out by decantation of the clear bath.
To compensate for this Tin falloff I used anodes of differing composition. I had anode baskets so I cut the mixture of anode pellets with a portion of pure Tin nuggets. This way the Tin(Stannous) composition remained in spec but now the Lead would dropoff very slowly. This is fine because Lead MSA is 4 times less expensive than Tin MSA and it takes very little LeadMSA to correct a bath. So the whole operation runs more economically because you now correct Tin concentration with cheap tin nuggets and cheap LeadMSA instead of expensive TinMSA.
There is another trick you may want to employ. If you use anode bags on your TinLead anodes, they will cause a high fraction of Stannate to throw off the anodes. Good plating cell design will have filtered solution flow rebounding off the workpiece then through a separating mesh and traveling directly through the unbagged anode nuggets on its way to the reservoir. This decreases the mean residence time of Tin atoms at the anode surface and can increase the fraction of Stannous throwing off the anodes. But it is probably easier to just add pure tin to the baskets.
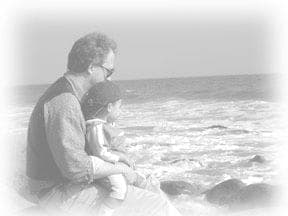
Dave Kinghorn
Chemical Engineer
SUNNYvale, California
The nodule problem may occur from many cause but for my experience found that organic contamination in plating bath, so the action we did to eliminate by do the carbon filtration 2 hours with 30% carbon filter per housing . The other action should do parallel is counter check your anode bag that all in good condition.
The other cause may I would recommend is pre-cleaning solution out of order or might be more contaminated especially is activation or pre-dip.
Raja Reddy- Bangkok, Thailand
Please bear with me on this but I've only entered this particular industry recently after having been in R&D. Would there be a better way to ensure cleanliness after the drill process, aside from simple deburring and say, compressed air 'cleaning?' I'm also curious if anyone would be able to share any potential pre-solder treatments which might reduce nodule formation. I've considered manual pre-inspection/via clearing and also the utilization of custom fixtures to clear the barrels of larger particles. Carbon treatment, continuous chemistry monitoring, etc. are already used in plating.
Henry Joseph Hopkins, III- Warrington, Pennsylvania, USA
Q, A, or Comment on THIS thread -or- Start a NEW Thread