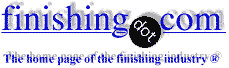
-----
Powder coating anodized aluminum
We use a chromate conversion pre-treatment on most of our aluminum parts with excellent results in adhesion quality. We are getting poor adhesion on the parts that we anodize. Is this normal?
Brian Maready1998
The anodizing section of metal-finishing.com has an excellent discussion of sealers and their effect on adhesion. I expect it would answer this problem.
Chris Jurey, Past-President IHAALuke Engineering & Mfg. Co. Inc.

Wadsworth, Ohio
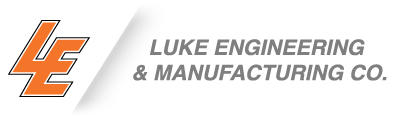
1997
Generally, the reason one would have poor paint adhesion on anodized aluminum is due to sealing the parts prior to painting. One needs to paint unsealed coatings.
Ward Barcafer, CEFaerospace - Wichita, Kansas
1998
April 26, 2010
I am curious about the last response (always paint unsealed coatings) because ASTM D1730
(prep of aluminum for painting) specifically calls out a potassium dichromate seal after anodizing.
The reason I ask: I'm having a paint adhesion issue on an AA360 die cast part and searching for options that are RoHS compliant but don't involve TCP either. All I've found is anodizing, but I'm concerned about acid entrapment (again, per a note in the ASTM spec) since this is a cast part. If I don't seal the casting will that avoid the acid entrapment? Is another step required instead of sealing to get rid of the remaining sulfuric acid?
Intended finish is powdercoat, probably polyurethane. Thanks!
- Monterey, California
Chris,
The problem is that the type of anodising mentioned has not been specified. It is normal to chromic acid anodise parts prior to paint to aid adhesion, in which case you do not seal.
It sounds as if you are doing sulfuric acid anodising, in which case it is commonly sealed prior to painting.
Your problem sounds more to do with porosity and rinsing than sealing.
Try alternate rinsing in warm (about 55-60 °C) and cold (room temperature) water, repeating the cycle two or three times. You may find that if the casting is particularly porous you will have to repeat the process even more often to try and remove the trapped acid.
Once you have carried out the rinse then seal as per your normal process, hopefully you will see a reduction in your adhesion problems.
Aerospace - Yeovil, Somerset, UK
May 5, 2010
Q, A, or Comment on THIS thread -or- Start a NEW Thread