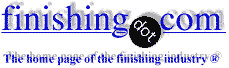
-----
Fire Protection for Powder Coating Booths, NFPA Issues
Q. We are getting ready to install a manual gun powder coating system. In doing some research, OSHA Regulation 1910.107(h)(12) states "All areas used for spraying, including the interior of the booth, shall be protected by automatic sprinklers where this protection is available. Where this protection is not available, other approved automatic extinguishing equipment shall be provided.
My questions are, is this actually required in Powder Coating booths? And does having a Powder Coating Operation require us to have automatic Fire Protection inside and outside the booth as well? Or is the powder used for powder coating considered non-flammable nor non-combustible, therefore the powder coating booth need not conform to this regulation?
Any answers would be greatly appreciated.
Mike D [last name deleted for privacy by Editor]Hydraulic Rakes - O'Neill, Nebraska, USA
2002
by NFPA
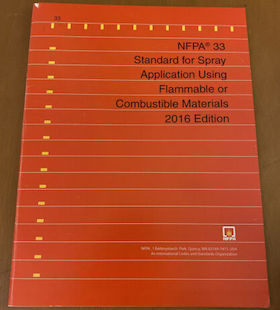
on eBay or Amazon
(affil link)
A. Mike,
Fire protection is required. See the new NFPA 33 Bulletin. Edition (2000).
Herb Ashley- Smartt, Tennessee
2002
Q. I have since obtained NFPA 33 (2000 edition), as a responder suggested. It is apparent that Fire Suppression is required in the booth. Currently, in our operation we have no fire suppression systems. So our next concern or question is what type of fire suppression is being used, water, gas, or powder type systems?
And this is probably a rhetorical question, but why are the systems not built into the booths? We are having a very well known supplier build us a booth, and had it not for my checking sources for Powder Coating Safety, we would have had no idea about Powder Coating booths requiring a fire suppression system.
Hydraulic Rakes - O'Neill, Nebraska, USA
2002
A. Mike,
My experience has been with water. Other systems are available. Check with you local fire extinguisher company. They may suggest CO2 extinguisher for the control panel.
I do not know why the fire protection system is not included. It may be the frequent change in NFPA requirements.
Also, make sure that the compressed air blow-off hoses are grounded. After purchasing compressed air hose, have maintenance check to ensure there is an internal ground wire. If it is not grounded, a spark and explosion may occur. An explosion will create a few maintenance problems.
Herb Ashley- Smartt, Tennessee
2002
A. A powder coat fire is a "Bravo" type fire. The last thing you want to put on it is water. Cheapest system would be a dry chemical BC/ABC system. Secondary would be a CO2 System. Normally paint booths do not come with a system already installed due to the number of different fire system manufacturers and their varying piping requirements or limitations.
Duane Buchanan- Greenville, South Carolina, USA
May 16, 2012
Q. Hi Duane.
I claim no expertise in fire suppression, so I'm not challenging your statement, just trying to understand it. I thought "B" fires were liquid or gas. Why would powder be considered liquid or gas? Thanks.
Regards,
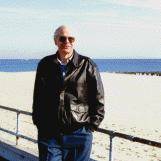
Ted Mooney, P.E.
Striving to live Aloha
(Ted can offer longterm or instant help)
finishing.com - Pine Beach, New Jersey
October 14, 2012
Q. We are presently in the start up phase of a custom powder coating shop. We have come upon some issues with the codes and compliance board and would like you input. We are installing an 8 x 8 x 8 open face booth and will be using a manual spray gun to apply the powder. Our questions are: does the booth need to exhausted to the outside? Also does the booth need a fire detection system?
Arthur S [last name deleted for privacy by Editor]- Yorktown, Virginia
2003
A. 1. Only your Air Quality folks from your local/regional area can answer that question.
2. Only your local fire department can answer that. Do not be shocked if they want a fire suppression system installed.
James Watts- Navarre, Florida
2003
A. Mr. Sparks,
The installation of your booth is required to meet the requirements of NFPA 33. It is all too common these days to see companies install equipment and neglect to perform a thorough search of all code requirements prior to installation, and the end result is, as you have found, a delay in start-up and additional cost to bring the facility and equipment to code requirements. To specifically answer your questions, yes the booth needs to be ventilated and fire protection installed. In addition, lighting and electrical connections must meet NFPA 70 requirements. Another code that may be of interest is NFPA 101, which outlines the classification of the area the booth was installed in. Pending the classification of the surrounding areas, you may be required to segregate the booth via fire rated wall structures. It is well worth the effort to talk to a consultant, as listed on this website, in advance, to assure all facility issues are addressed. One last thought: Since the booth is required to be ventilated, you will need to investigate the impacts on your existing air permit, provided you have one, or you will need to obtain one if you are above regulated de minimus levels.
Best of Luck!
Ira Donovan, M.S.F.Kansas City, Missouri
2003
A. Some powder booths have a three stage filter system allowing the air to be returned to the shop. This is the way to go from numerous standpoints. Look for 'final filters', Basically you need a plenum after your exhaust fan to hold these filters.
James Callahan- Louisville, Kentucky, USA
2003
A. Hi Arthur!
I have installed these systems before and found that most of the time, you will be required to install fire suppressing equipment if not by the local fire department, then by your insurance company. As stated earlier, the installation of your booth is required to meet the requirements of NFPA 33. You need to understand this code! It is not usual to exhaust powder to the outside. This is one the selling points when purchasing this type equipment. Why waste warm or conditioned air to the outside environment?
Some insurance companies that are not experienced in these type systems can be difficult and expensive to deal with when it comes to safety issues. I had one insurance company ask me to install a water suppression system within my oven. Go figure... In any automatic type powder application system, you are required to install safety shutdown equipment such as IR/UV detection which cuts all incoming powder, electric and air to the booth in event of a spark/fire.
Manual booths are usually not subject to this criteria because there is an operator holding the application gun trigger and it can be turned off by him/her. I have also been asked by a few insurance companies to install equipment into these booths such as yours, but after I have shown them many other similar type systems, they have understood.
Many insurance companies are still not up to speed on powder coating and its characteristics. You may need to educate them or the fire department on typical powder booth installs. I have never seen or heard of IR/UV detection equipment within an open faced-manual system. Your best bet is to ask some of the paint booth manufacturers if they have any customers that have needed to install their equipment in this fashion, then contact some insurance companies to see why. In the end, if the local fire marshall/chief or your insurance companies require you to install the equipment, you must comply ... no matter how painful it may be.
![]() Bob Utech Benson, Minnesota |
![]() Ed. note: Bob is the author of: "High Performance powder Coating" on eBay or AbeBooks or Amazon [affil link] |
A. My background - P.E. (Fire Protection) C.S.P. - 25 years field experience with variety of insurance companies.
Because of the enclosed area and 'plastic' nature of dust epoxy for the powder coating - a simple 'water spray' type of fire protection system is recommended. (A CO2 or other type of extinguishing system is not recommended due to cost or effectiveness) Piping feeding the heads should have a separate control valve (so that it can readily be turned off without impairing your building sprinklers). Heads should have a small 'paper' bag on them, secured with a rubber band to prevent them from being 'loaded' with overspray. (The bag will burn off easily in the event of fire) Housekeeping is my biggest complaint with this type of operation. Operators should be required to clean the overspray routinely from the booth. Although this operation does not have the flammable vapors associated with VOC applications, electrical equipment inside the booth should be 'dust tight'. It should also go without saying that ignition sources (open flames, heaters, etc.) should not be within the enclosure.
With regards to sprinklers in OVENS. I have seen this done when the material to be dried is highly flammable or solvents are present in significant quantities within the oven. (i.e.: Veneer dryers) The sprinklers chosen are ultra high temperature and do not activate at normal oven temperatures. I have seen buildings with complete sprinkler systems burned to the ground because of involved oven fires that have overwhelmed the ability of the ceiling sprinklers.
- Sacramento, California USA
August 22, 2013
A. Interestingly the Powder Coat Institute when asked about this for an open booth with manual gun said they did not see a reason for any fire or explosion suppress system since letting go of the trigger cuts off the powder source and any explosion of airborne dust would be so fast that any fire or explosion suppression system would be too late to do anything. You would still need to comply with any issues regarding electrical and lighting construction of the booth to eliminate ignition sources for the powder. Unfortunately this appears to be an area where insurance companies just take the belts and suspenders approach without regard to the facts. You most likely will have to install some expensive installation.
Mark GoldmanClamco - Berea, Ohio
June 30, 2017
Q. I have a basic question. I have a client with a fully enclosed powder coating booth, connected to the buildings fire sprinkler system (wet) with expired service. My client is telling me it does not need to be maintained as long as the buildings system is maintained, I am not buying it. The system is directly tied into the buildings fire sprinkler system and was serviced 5 years ago. I was thinking this needs to be done annually?
Anyone with some insight on this?
Much thanks!
Southwestern Inspection Services LLC - Las Vegas, Nevada USA
October 13, 2017
`
NFPA Powder Coating Booth Air Exhausting back into shop. Need Help!
Q. We are moving our powder coating business and are having trouble with our code enforcement inspector in getting around our powder coat booth having air recirculate into the building along with several other questions.
We have a 8 x 8 x 10 open spray booth that exhausts into the shop air after 3 stages of filtration. We have installed a Chemical Fire Suppression System, and also have a 8 x 8 x 10 oven.
I have received the following from our inspector:
- Recirculation of exhaust air from the spray booth is specifically prohibited.
- Make up air for the spray booth and oven.
- Powder recovery system
- York, Pennsylvania USA
October 13, 2017
A. IR / UV detection is not required in an open face manual booth with a gun trigger (dead man switch). Powder pattern if ignited will go out when trigger is released. IR /UV detection is required in auto gun booths to shut down powder delivery / ignited powder. Fire protection is required in both manual and auto gun booths.
A. Wet pipe sprinkler protection within a powder booth and adjacent powder recovery enclosure should be at minimum inspected annually as part of base building sprinkler system annual test, for basic exercising of sectional shut off valve(s), any physical damage to piping, pipe hangers, changes to the booth impairing sprinkler protection, etc. Remarks should be part of the base building sprinkler system test record.
IR / UV detection systems for powder booths should be at minimum inspected / certified annually by OEM authorized highly trained technicians.
A. Explosion is a concern with enclosed powder recovery systems and associated ductworks. Explosion variables include powder Kst - explosion property or Pmax, powder flow rate maximum delivery, ventilation airflow rate. These variables plug into a calculation to determine Maximum Concentration. Maximum Concentration / MEC - Maximum Explosive Concentration (a property of the powder) gives a % MEC result. <50% MEC = adequate ventilation does not require explosion suppression system. Refer to NFPA 33 Appendix C. MEC >50% requires explosion suppression system + very fast acting Isolation Gates in ductwork between booth and enclosed powder collector, mitigating a potential fireball back to the spray booth and into the room.
- Toronto, Ontario, Canada
November 13, 2017
Q, A, or Comment on THIS thread -or- Start a NEW Thread