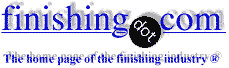
-----
Zinc content increase
I'm facing problem with the zinc content in my plating bath. It seems to increase whenever we didn't run a production. It jump from 15 g/ml to 28 g/ml. So what I have done in the past is, reducing the zinc ball@zinc plate. But I think it won't be so practical. What should I do to let the zinc content stable between 15-20 g/ml.
Shimano- Malaysia
Hi Shimano. You inadvertently omitted a critical factor by not telling us what kind of zinc plating bath this is. If it is alkaline, the zinc will dissolve into it so the concentration grows too high too quick. The most practical approach may be to use only steel anodes in the main tank and use a separate 'generation' tank where you dissolve the zinc anodes. Then you circulate however much solution you need to maintain the zinc concentration in the main tank. Good luck.
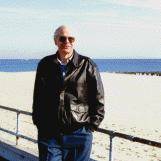
Ted Mooney, P.E.
Striving to live Aloha
(Ted can offer longterm or instant help)
finishing.com - Pine Beach, New Jersey
Mr. Shimano,
I concur with Ted Mooney's response.
Joel Garciaplating co. - Mcallen, Texas
Since the problem is in non production run time, can you take the anodes out and store them in a plastic drum full of water? Not much fun, but cheap and effective. Zinc anodes slowly dissolve in the plating solution, thus the rise.
James Watts- Navarre, Florida
The problem with big zinc lines is that they are made to run 24/7 without shutting off just for the above-stated issues. Most have more than 100 100+ pound anode baskets hanging in them which virtually precludes removing them every day. But you can try trickle reverse current sufficient to slow way down or shut down altogether the anode reaction, but this means you must leave the line running, and most lines do not have this reverse option. It also requires special danglers in the barrels or special racks to prevent contamination, and you'll still have to correct addition agents when you start again.
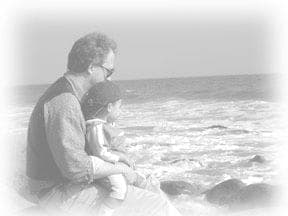
Dave Kinghorn
Chemical Engineer
SUNNYvale, California
Q, A, or Comment on THIS thread -or- Start a NEW Thread