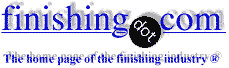
-----
Achieving class 3 chromate conversion coatings

(to hopefully help readers more easily understand the Q&A's)
Chromate Conversion Coatings (sometimes called 'Chem-Film' in the USA) are widely applied to aluminum either as a final corrosion resisting treatment or as a pretreatment for paint. The most widely used specification covering the process is MIL-DTL-5541 [⇦ this spec on DLA] (formerly called MIL-C-5541). It includes two classes, Class 1A (the more general class) and Class 3 (which is similar but sometimes thinner or less strongly colored because it has the additional requirement of meeting a specific (and somewhat complicated to measure) electrical conductivity requirement.
For the coating to o comply with the requirements of MIL-DTL-5541 / MIL-C-5541 the chemicals used for the coating must be on the 'Qualified Products List', QPL-81706 [⇦ this spec on DLA].
An issue which can make the discussions hard to follow if not understood is that there are two brands of Chromate Conversion Chemistry on the QPL that are so common that people may use their trade names generically. Thus posters may sometimes say they 'Alodined' their parts (did chromate conversion coating on the parts using 'Alodine' from Henkel), or 'Iridited' them (used Iridite from Macdermid/Enthone for the chromate conversion coating).
Avoid using the word 'type' to describe Class 3 and Class 1A coatings because 'Type' is now reserved for describing Type 1 coatings (with hexavalent chrome) and Type 2 (coatings with no hexavalent chrome).
Q. Can I presume the Alodine color uniformity for Type I Class 1a will be better than Type I Class 3? My customer is asking for uniform yellow coating, but most of the coating houses we use told me the color variation is the nature of the process, especially around the hole areas. However, my customer did show me a perfect sample they would like for me to match. I am just so curious is it even reasonable to define color variation in the spec for Alodine process?
TH Lee- Houston, Texas
May 16, 2023
A. Hi TH. There are some interesting aspects to your question. First, if your customer showed you a gold color which is 'perfect' and with no iridescence around the holes, are you absolutely sure the sample was not gold-dyed anodizing rather than chromate conversion coating?
Anodizing is clearly a decorative finish whereas most people consider chromate conversion coating a functional finish rather than a decorative one. So 'perfect' yellow anodizing probably isn't nearly as difficult as 'perfect' yellow chromate conversion coating.
Yes, a thicker conversion coating will probably be less iridescent, and a more consistent color is probably obtainable with lots of agitation than with poorer agitation. And I suppose it is also possible that Henkel has a particular Alodine process which they feel gives a more consistent, less iridescent color.
Luck & Regards,
Ted Mooney, P.E. RET
Striving to live Aloha
(Ted can offer longterm or instant help)
finishing.com - Pine Beach, New Jersey
A. Hi TH!
I love this question, because it comes up in my job so often:)
The specs for yellow chromate come right out and say that color variation is normal and acceptable... it's a FUNCTIONAL spec, rather than aesthetic!
But because we like happy customers... here are some things I've encountered that mess up the visual appeal:
Remember always that the chemfilm isn't fully "set" when it leaves the bath, the way you'd expect say.. a black anodize to be. It is fragile and easily discolored for up to 48 hours.
Holes and contours: Bleed-out from liquid in holes or tight contours will show as discoloration.
Rack drips: taking parts off the line, the first step is to blow off the flight bars and racks! Drips will show up, and if you have shared flight bars with a current-added process like anodize, that copper is BAD. It will not only discolor, but also compromise the utility of the finish.
Surface prep: one of the most combative SCARs I've ever dealt with was from a customer who milled parts, then tumbled them, then sent them to us demanding "uniform color". Spoiler, the color was not uniform, because the tumbling did not impact internal contours equally to flat surfaces. We even hacked up one of their rejected parts and had it salt-fogged at 168h ... 0 pits. Again: FUNCTIONAL specification. The surface prep also applies even to slight variations in finish quality (RA? Roughness? Microterrain? I'm not a Milling Inspector haha) on various parts of um ... the part. But seriously, if there's different tooling and different finish on different bits, of course you will see the color/sheen/iridescence varies as well.
If you can pass salt fog, you met the spec... if the PO requires visual appeal, that's a high quote or a no-quote.
Your best bet for a uniform color is an extremely well prepared surface without holes or contours, and an unracking team who know how to approach conversion coating. But it is still a really big ask to demand color uniformity on a spec that very clearly spells out that it is NOT a requirement.
One of the stupidest chromate fails I've seen involved streaking from the parts having been cut on a waterjet with mild steel supports ... they left a visible tattoo pattern on the finished parts ... 1.25" apart :)
I drove over to the source with a camera and a ruler and made a bit of a stink about the garbage in / garbage out thing.
There are a million ways to fail at a "perfect" chromate cc, and it will be a team effort between you and your customer to have them send parts that are even capable of taking a good coating, and your team to provide and protect it until it has cured.
Since the customer does not need RoHS obviously ... how's about a nice Type II anodize with sodium dichromate seal? ;)
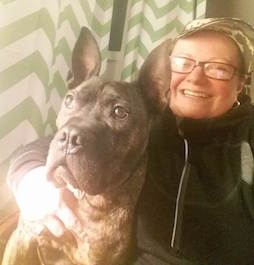
Rachel Mackintosh
lab rat - Greenfield, Vermont
June 9, 2023
⇩ Related postings, oldest first ⇩
Q. Achieving class 3 coatings using Iridite 14.2 / Alocrom (Alodine) 1200
We have been successfully using the above systems to MIL-C-5541 class 1A for some time, up until recently there has been no requirement for class 3 coatings. This is set to change as some of our new customers are requesting coatings to class 3.
My understanding of the difference between 1A and 3 is the film thickness i.e. the class 3 coating is thinner and has reduced resistivity and reduced corrosion protection. The thinner coating being achieved via reducing the immersion times. However, the manufactures details I have give no indication of concentrations vs. immersion times to give the required film thickness. Is the application of a class 3 coating simply based on experimentation and testing for a given bath concentration, or are there any guide lines i.e. concentration vs. immersion times, out there which could be applied to reduce the trial and error factor?
In addition what are the test criteria i.e. resistivity values etc to use in order to comply with the specification, considering that the only values given are in para 6 or the notes section which sates it is for info only and non mandatory. Para 3.8 states that the values and the frequency of testing are to be defined by the procuring activity. Does this not cause conflicts or contradictions. Is it possible for the 6061 panels to pass their resistivity tests for a given customer and comply with the spec but not for a.n. other customer?
Any info or insights into this would be gratefully received
Richard Mosleymetalsmiths - UK
2002
A. Hi Richard,
The one bit of help I can give is how to test for the coating weight.
Alocrom your panel rinse and blow or air dry (do not oven dry).
Then find the mass on a lab balance to 0.0001g.
Strip in 50% concentrated nitric 50% water (it will strip quick if within about 3 hours of coating) then rinse.
Swab with damp cotton wool if required to remove traces of coating.
Rinse and dry.
Then reweigh. From the area of the panel you can work out the coat weight.
Also stripping in nitric does not have a go at the base metal unlike other strips.
You will find the relationship between coating weight and time is non-linear, so you will have to test different dip times to find the best time to get the coating required.
Also you will have to put in place some testing as the time will drift a bit due to bath conc., pH, temperature etc.
As to the bit about the customer supplies the requirements you are right two customers could supply two different requirements, so go back and make sure they know what they want before you start supplying products to them. (If I was a betting man I would bet that the customer only wants what they had before of someone else and don't know really what they want)
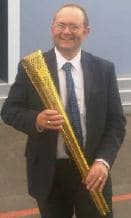
Martin Trigg-Hogarth
surface treatment shop - Stroud, Glos, England
A. There are only two requirements in MIL-C-5541E that differ between Class 1a and 3.
1) The solution used must be on the Qualified Products List (QPL) for that Class. Many products, including Iridite 14 and Alodine 1200, are listed for both classes.
2) Class 3 must pass a Electrical Contact Resistance Test per paragraph 3.8, but only when specified. I have never seen this specified.
So in most cases the specification makes no required distinctions between Class 1a and 3 coatings.
The only discussion about immersion times, coating thickness, and/or coating weights occurs in the non-mandatory Notes section of the specification. It suggests that Class 3 coatings are thinner due to lower immersion times but gives no guidance.
Chris Jurey, Past-President IHAALuke Engineering & Mfg. Co. Inc.

Wadsworth, Ohio
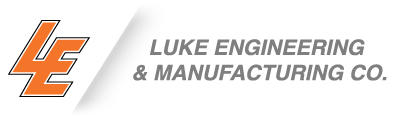
A. Richard,
What Martin said is absolutely correct. I would like to add, though, that while two classes are different, they don't have to be processed that way. Our customers only require an electrical resistance test (<5,000 micro-ohms before salt spray and <10,000 micro-ohms after) to certify to class 3, since our class 1A w/ a 3 minute immersion time satisfies this test, we can run our class 1A and 3 on the same rack. Our customers also accept one salt spray test for both classes as they are the same thickness/coating weight.
I don't believe coating weight/thickness is the difference between the classes, I believe that the electrical properties are the dividing factor as class 3 needs to be acceptable for EB (Electrical Bond) areas.
Hope this gives some more info.
Benjamin J. Curto- Ponderay, Idaho, USA
Q. Thanks to all for the info it is much appreciated !
Chris,
As to the interpretation of the spec. If a customer is requesting a class 3 coating yet not specifying values etc, how do you verify that a class 3 coating is achieved? Do you interpret the spec such that the tests default to those detailed in MIL-DTL-81706 [⇦ this spec on DLA] and described in para 6.1.2 of MIL-C-5541 i.e., <5000 & <10000 microhms under an electrode pressure of 200 psi?
Rich Mosley- UK
A. Without an electrical resistance requirement, only four conditions must be met for a Class 3 coating.
1)The product must be on the QPL for Class 3.
2)The monthly corrosion and wet tape testing must be performed.
3)The bath solution must be analysed weekly.
4)The coating must be uniform in appearance and iridescent yellow to brown.
Luke Engineering & Mfg. Co. Inc.

Wadsworth, Ohio
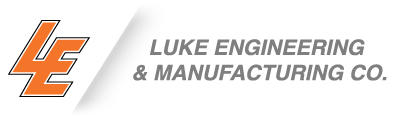
Q. Chris,
Again, thanks for the response.
Forgive me if I am missing something fundamental but I want to be as clear as possible on this issue prior to offering class 3 coatings.
If a customer requests a class 3 coating but does not specify any resistance values, and the chemical process used is capable of producing both classes. Bearing in mind that class 3 coatings are qualified under MIL-DTL-81706 [⇦ this spec on DLA] to the 5000 and 10000 values. How is it possible to certify a component as having a class 3 coating without testing ? The actual coatings resistance values may be outside the required 5000 and 10000 values and as such a class 1A coating. If resistance values are not specified & testing carried out essentially class 1A and class 3 could be one in the same.
Another question is, are the 5000 and 10000 values seen as qualification values only, i.e., could a customer legitimately ask for lower values i.e., outside those that the QPL chemicals are qualified to?
Richard Mosley- UK
A. You are correct. If electrical resistance testing is not specified, the exact same coating could meet the requirements of both Class 1a and 3. Testing per MIL-C-81706 is not the responsibility of the applicator but rather the chemical manufacturer. The applicator's responsibility to use only QPL products listed for the appropriate class and certified to MIL-DTL-81706 [⇦ this spec on DLA] .
Chris Jurey, Past-President IHAALuke Engineering & Mfg. Co. Inc.

Wadsworth, Ohio
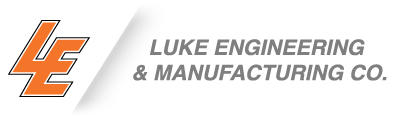
Multiple threads merged: please forgive chronology errors and repetition 🙂
Chem film color vs. electrical resistance
Q. We are a manufacturer of RF communication equipment, we design and specify but do not manufacture in house. Some of our modules are installed in an indoor situation while others are installed in a out door situation. All of the parts that are installed out doors and are exposed to the weather are die cast Aluminum, 380 grade, chem film treated and powder coated. We have begun using a new supplier of parts and are having problems with the chem film spec we have used. We have in the past spec'ed "FINISH: CLEAR CHEM FILM/ MIL-C-5541 CLASS 1" and our supplier is tell us that the class of finish determines the color and want us to change the spec to "FINISH: YELLOW CHEM FILM/MIL-C-5541 CLASS 1". The main reason we spec the chem film treatment is to maintain electrical conductivity over time as the performance of our equipment is very sensitive to maintaining an extremely low resistance to ground, (RF devices are susceptible to poor grounding) My understanding was that the color was independent of class and that the chem film is a conductive treatment. The supplier is telling us that the electrical resistance is lower for the class 1 treatment than for the class 3.
Is there some definitive reference material that I can use to resolve this, the standards don't appear to answer my questions.
Bruce CorkillManager Mechanical Design - Wellington, NZ, New Zealand
2003
A. Hello Bruce,
Per the Mil Spec, Class determines coating thickness NOT color. Class 1A coatings are thicker and as a result less conductive, gold color less conductive than clear. Chromates are thin and can easily be penetrated for electrical contact. Class 3 coatings are usually for paint prep or least electrical resistance. Class 1a for the best corrosion resistance.
Bill Grayson- Santa Cruz, California
Multiple threads merged: please forgive chronology errors and repetition 🙂
Q. I WOULD LIKE TO ASK IF THE DIFFERENCE IN TONE BETWEEN A PART WHICH HAS PLATED IN ALODINE 1200 CLASS 1A AND A PART WHICH HAS PLATED IN ALODINE 1200 CLASS 3 IS A CRITERION OF THE DETERMINATION OF THE CLASS
.
I WOULD LIKE TO KNOW BECAUSE THE SAME MATERIALS(SPECIFIED TO HAVE THE SAME CLASS ) THEY DIFFER IN TONE (SOME OF THEM HAVE DARK YELLOW COLOUR AND OTHERS LIGHT IRIDISH COLOUR),FROM DIFFERENCE SUPPLIERS.
I KNOW THAT THE MILITARY STANDARD DOES NOT SPECIFIED STANDARD COLOUR BUT A RANGE FROM LIGHT IRIDESCENT TO DARK YELLOW BUT ALSO REFERS THAT THE IMMERSION TIME IS MORE LESS IN CLASS 3 THAN CLASS 1A.
MECHANICAL ENGINNER - ATHENS, GREECE
2005
A. The difference between a class 1A coating and a class 3 coating is, a class 3 coating has customer specified electrical conductivity values to suit a given application ref para 3.8 of the specification. Essentially a class 3 coating is customer specific i.e., one customer's class 3 coating may be another's class 1A. It is worth noting however that the conversion materials are qualified to a specific set of values, ref section 6 of the MIL specification. Please also note, both class 3 and class 1A coatings (regardless of colour) have to pass the same corrosion tests i.e., 168 hours salt spray.
So, to answer your question, tone or colour does not define the class of coating. However, as a rule a thicker coating has a darker colour, more corrosion protection and higher resistance values than a lighter, thinner coating. That said, colours at both ends of the spectrum must pass the 168 hours salt spray.
- UK
Is it MIL-C-5541E, Class 1A, Class 3 if etching is skipped?
Q. I have an aluminium casting which is firstly anodized per MIL-A-8625 / MIL-PRF-8625
[⇦ this spec on DLA] type II class 1. Thereafter, the part is machined and then chromated to MIL-C-5541 Class 3.
The part cannot be etched as it will remove the anodize layer. Therefore the part is chromated without etching. My question is if the casting is not etched, does it still qualify as chromated per MIL-C-5541E, Class 1A, Class 3?
machine shop- Singapore
2005
A. It's nearly impossible (alright down right difficult then ) to get diecast aluminum such as 380 to pass the 168 hour salt spray REQUIREMENT of MIL-C-5541 even with a good strong etch so my guess, no my experience tells me so, that there is NO CHANCE that the resulting chem film is up to MIL-C-5541 standards without the etch. In fact, to be honest, if you're immersing the entire anodized part into the chem film bath, I'd be fairly certain that the chromating bath would eat into the anodize seal layer and disrupt it to the point where the anodize will no longer pass 336 hour salt spray. My opinion, diecast aren't capable of meeting any finishing standard that includes a corrosion resistance requirement. Good luck.

Milt Stevenson, Jr.
Plating shop technical manager - Syracuse, New York
A. MIL-C-5541E is a process specification. Per Paragraph 4.3.1, the required inspection is a process control test to prove that the chemical conversion coatings "... are acceptable as evidence of the properties being obtained with the equipment and procedures employed." That is, it is only necessary to prove monthly that the process is in control not that each part or alloy coated meets these requirements. Therefore, if parts including castings, are coated using the validated chemicals and procedures, there is no specification requirement that they individually pass or be able to pass a 168 hour corrosion resistance test. For Class 3, this requirement is only for "specimen panels" of 6061-T6 material. Lot acceptance only requires a visual inspection for appearance and workmanship. The specification for testing and listing QPL materials, MIL-C-81706, only tests Class 3 chemistries on 6061-T6.
Chris Jurey, Past-President IHAALuke Engineering & Mfg. Co. Inc.

Wadsworth, Ohio
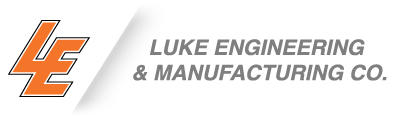
A. You may want to check into Metalast TCP-HF as a replacement for your Chem-Film coating on the cast part. Developed by the department of the Navy for coating F/A-18 Hornets. Research has showed that Metalast TCP-HF will pass salt spray tests on all cast aluminum. It can even be used to seal the anodized pores and achieve between 500-1000 hours of salt spray for the anodized layer.
Randy Fairbank- Lewiston, Idaho, USA
A. The "New" tri-chrome for aluminum that replaces the hex chrome chem films is supplied by 3 companies in the USA. All must comply with the original formulation and if followed will produce the same results.
That being said surface pretreatment is most important even with a top of the line product therefore be careful when quoting laboratory results under perfect conditions. What really is important is performance results under most "reasonable" shop conditions. I suggest having a good process/control with quality materials and available, competent, local technical help is best.
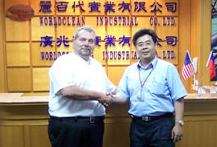
Drew Nosti, CEF
Anodize USA

Ladson, South Carolina
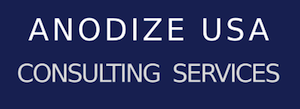
Indeed, Drew, even when inventors/developers work for the Navy, pride of ownership can lead people to exaggerate advantages and downplay disadvantages :-)
Luck & Regards,
Ted Mooney, P.E. RET
Striving to live Aloha
(Ted can offer longterm or instant help)
finishing.com - Pine Beach, New Jersey
Multiple threads merged: please forgive chronology errors and repetition 🙂
Q. How about when a class 1a finish is required for maximum corrosion protection? If there is no electrical requirement called out (because a class 1a finish is desired, not a class 3), how do you know if you are getting the class 1a? Meaning, if a class 3 is equivalent to a class 1a when no electrical resistance test is called for, does that mean the thinner, less protective class 3 can be substituted for a class 1a?
Terry Bartick- Portland Maine
August 25, 2010
A. Class 3 is NOT the equivalent of class 1a, regardless of what some MFGs say or passing a minimum salt spray.
You need to fill the customers PO / spec or get him to change it. Darker chem film is a lot easier to spot a problem than pale will ever be.
- Navarre, Florida
Multiple threads merged: please forgive chronology errors and repetition 🙂
Alodine 1200s: How do I get class 1A AND class 3?
Q. Hi,
I know that I can use the product of Henkel Alodine 1200s to get the MIL-C-5541-F class 1A or 3. But I wasn't able to find how to get class 1A and how to get class 3. Which is the difference? Time? pH? Temperature?
Thanks for your answers
customer - SPAIN
April 6, 2010
A. Hi, Antonio. I have seen shops get a clear chromate by dipping for just 15 seconds into a yellow chromate, and then leaching the color out by soaking in warm water -- but some people question whether this really affords measurable protection. It is much better to install 2 tanks, one for Class 1A and one for Class 3. Please note that Alodine 1200S is a proprietary product, and Henkel will supply you with a technical data sheet for the recommended times, pH, and temperature.
Regards,
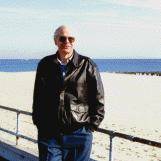
Ted Mooney, P.E.
Striving to live Aloha
(Ted can offer longterm or instant help)
finishing.com - Pine Beach, New Jersey
A. Per MIL-C-5541, a clear coating is NOT allowed for either Class 1a or 3 unless specified by the purchaser. When using products that are listed on the QPL for both classes, such as Alodine 1200, there is NO requirement to process the Classes differently. There could be an additional electrical resistance testing for Class 3 coatings, but only when required by the purchaser.
Chris Jurey, Past-President IHAALuke Engineering & Mfg. Co. Inc.

Wadsworth, Ohio
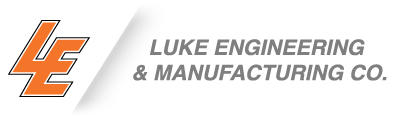
April 15, 2010
Multiple threads merged: please forgive chronology errors and repetition 🙂
Q. Good day everyone,
I too and struggling with this very topic. I understand the requirements and testing responsibilities but still struggle to understand why the electrical resistance test is not a requirement. It appears to me that the other tests within this specification were "grandfathered" as the acceptable testing criteria.
I would like to discuss this with someone that performs the electrical resistance test. Can any of you recommend a testing facility that could provide input on this subject?
I look forward to additional comments on this topic.
Thanks,
- New Hope, Minnesota
September 16, 2010
Q. Can Iridite 14-2 from MacDermid meet the requirements of ASTM B449 Class 1, that is thickness and salt spray test?
Daris Combsmotorcycles - Commack, New York, USA
November 9, 2011
Q. An engineer requires 2 classes of coating on one AL 6061 tube, MIL-DTL-5541 TYPE 1 CLASS 1A on the middle external surface and class 3 on the both tube ends where fittings will install (to get a lower electrical resistance). It is difficult in operation. The customer does not require the electrical resistance testing. So how can I know I have got class 3 coating on tube end area? If we used Alodine 600 to get class 1A coating. Can the electrical resistance test meet the class 3 coating's requirements?
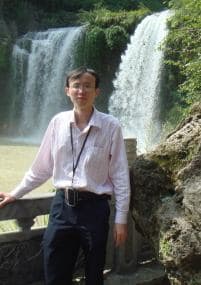
Hans Lin
- Shanghai, Pudong, China
February 21, 2013
----
Ed. note: Readers may also be interested in Letter 40382, "Electrical resistance of chromate conversion coating class 3".
Q, A, or Comment on THIS thread -or- Start a NEW Thread