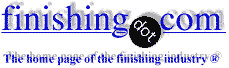
-----
Zinc corrosion resistance vs. Cadmium
I'm revisiting the issue of replacing our Cadmium coated parts. Currently the parts (about the size of a car disc brake rotor) are Cadmium plated to .0002" thick. Our main concern is corrosion resistance. All the other properties that make Cadmium superior don't really apply.
I looked into electroless nickel but the cost is excessively high and I won't get the sacrificial protection I'm looking for. So it looks as though I'm going with an electroplated Zinc.
My question lies in specifically how thick a Zinc coating I should go with. I can get a minimum .0002" thick Zinc (basically ASTM B633 Service Condition 1) or my original plan was to go with ASTM B633 Service condition 3 (approx. .00047" thk. I know Zinc is not equivalent to the corrosion protection of cadmium so that's why I planned on the Service Condition 3. But I can also get a yellow chromate finish which helps deter the formation of white corrosion longer than without.
So my question appears to be, speaking mainly for corrosion resistance, what's my best zinc spec for comparable protection to my cadmium plate?
If anyone can offer any feedback it would be greatly appreciated.
Thanks!
Brian Bukoski- Erie, Pennsylvania, USA
If your main objective is corrosion resistance, then look at using a zinc-alloy plating instead of basic zinc plating. The zinc alloys are slightly more expensive, but give improved corrosion performance. If you are using a standard hexavalent chrome passivate, then I would recommend zinc-nickel plating. If you are using the more environmentally-friendly trivalent chrome passivate, then I would suggest looking at zinc-iron.
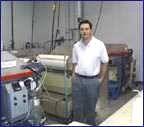
Tim Neveau
Rochester Hills, Michigan
Hi,
I am not a professional in the plating industry. However, I have a similar problem and have been researching the alternatives for cadmium plating. I have been told by a few people that a 70% tin/ 30% zinc combination, with a yellow hex chromate has very good corrosion resistance. Does anyone know how that compares to the zinc/Nickel and zinc/iron combinations in terms of corrosion protection?
Thanks,
Joe Trattner- Bartlett, Illinois, USA
I think most people will concede that zinc-nickel with hexavalent chromate offers the highest corrosion resistance. But remember that corrosion resistance was only one of the many strengths of cadmium plating. Another was lubricity, and if you are doing fasteners, I think you will find that tin-zinc offers better lubricity and freedom from stick-slip than the other zinc alloys.
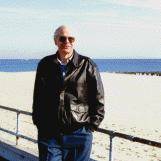
Ted Mooney, P.E.
Striving to live Aloha
(Ted can offer longterm or instant help)
finishing.com - Pine Beach, New Jersey
I think its worth pointing out here that the only cadmium replacement accepted by the U. S. military for aircraft is ion vapor deposited aluminum followed by a chromate conversion coating. This is not for its lubricity -- it really doesn't work well on fasteners. In most environments, it equals cadmium for corrosion resistance. In acidic environments, it is better.
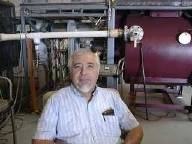
Jim Treglio - scwineryreview.com
PVD Consultant & Wine Lover
San Diego, California
The advantage of IVD is galvanic compatibility with the aluminum airframe under both aerobic and anerobic conditions (after all, IVD aluminum is aluminum). That case would not be applicable to joining steel parts on cars. As people have said here many times in the last few years, there is no such thing as an across-the-board replacement--it's individual application by individual application.
When you say, Jim, that IVD aluminum is the only replacement accepted by the U.S. Air Force, I am sure that there are fastener applications and possibly other individual applications where IVD is now used and cadmium formerly was. But I am also sure that nowhere does it say in the abstract that IVD can be substituted wherever cadmium is specified.
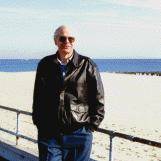
Ted Mooney, P.E.
Striving to live Aloha
(Ted can offer longterm or instant help)
finishing.com - Pine Beach, New Jersey
Sorry, Ted, but I never said that IVD aluminum could replace cadmium across the board. It's not used on fasteners to any degree (poor lubricity), contactors (which actually use nickel-cadmium), and on many high strength steel parts. The problem with the latter is hydrogen embrittlement brought about by hydrogen absorption in the environment, not during deposition. IVD aluminum is more susceptible than cadmium. I should add that the military is accepting aluminum deposition by other means, specifically sputtering and electroplating.
Jim Treglio- El Cajon, California
Ahem... getting back to Brian's original question: I would recommend the Zinc, specifically, type II, SC 3 (0.0005"thk) or SC4 (0.001" thk). As long as the thicker coating does not interfere with close tolerances (threads, etc), this will give the most corrosion protection for most situation and the zinc is rated for a slightly higher temp than Cad.
I have experience in oceanographic engineering and my passion for designing and building sports racing cars will use Zn SC4 on my disc brake rotors and suspension arms.
John C. McCannME and ace car designer - La Mesa, California
Q, A, or Comment on THIS thread -or- Start a NEW Thread