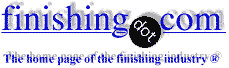
-----
Why use cadmium plated fasteners in the aeronautical field
Q. As the father of a final year mechanical engineering student, who has a thesis to write on Cadmium plated fasteners, can you please explain why Cadmium plated fasteners are used on aluminium alloy body panels in the aeronautical field? What are the advantages and disadvantages of Cadmium plating in such applications?
Harold Michael George- Selby, North Yorkshire, England
2002
A. The most significant disadvantage is environmental, Harold: cadmium is a toxic, cumulative poison like mercury and lead. There have been intensive efforts to reduce cadmium plating for a very long time now; the easiest switch-overs came decades ago, and the toughest ones aren't completed yet, and may not be for some years to come.
Asking for the advantages of cadmium is a bit like asking why wood is better than brick. It's no one single thing, it's a combination of properties that make it more fit for a particular application than other materials. And just like brick isn't wood, no other material is cadmium, so other materials offer some of the properties of cadmium, but no other material has ALL of the properties of cadmium.
The useful properties of cadmium as a fastener in aircraft manufacture include: corrosion resistance, sacrificial protection, freedom from gummy or bulky corrosion products, galvanic compatibility with aluminum, excellent lubricity and freedom from stick-slip for consistent torquing, softness and malleability, non-galling, the ability to accept chromate conversion post-treatments, good solderability, and the ability to be deposited in forms that will not trap hydrogen so baking can relieve the potential of hydrogen embrittlement. There are dozens of substitutes that offer some but not all of these properties. A coating that comes close for aircraft fasteners is Ivadizing (vacuum deposition of very pure aluminum); but depending on what's considered most important, I'm sure some people would challenge the claim that Ivadizing comes "close", while others would say it not only comes close, it's better :-)
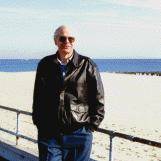
Ted Mooney, P.E.
Striving to live Aloha
finishing.com - Pine Beach, New Jersey
A. Cadmium plating is an excellent corrosion protector and has been in military and aviation specs for many years. These are controlled by Government bodies and consequently they do not like change! No one is prepared to take the plunge and come up with a good alternative, just in case it goes wrong and lots or people get killed. In real terms, it is debatable if there is anything better. You may well hear more about this one!
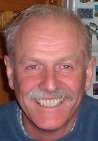
Trevor Crichton
R&D practical scientist
Chesham, Bucks, UK
A. Hello Harold!
Cadmium is used to coat fasteners for the simple reason that it works, and quite well. Cadmium is relatively easy to electroplate onto high strength steel, and for those steels whose strength is too high to tolerate the hydrogen embrittlement from electroplating, it can be vapor deposited ("vac cad" is the jargon). The cadmium does two things promoting corrosion resistance: first, it is a sacrificial coating for the steel, and readily takes a chromate conversion coating which improves the corrosion resistance many fold. Second, it's galvanic characteristics are compatible with aluminum. That means it won't form a battery enhancing the corrosion, a common problem when dissimilar metals are in intimate contact in the presence of an electrolyte (water).
Hope this helps!

Lee Gearhart
metallurgist - E. Aurora, New York
A. Cadmium has a few of very nice engineering characteristics. As a coating it has excellent corrosion resistant properties. Because of its nobility, it is sacrificial to most metals (ferrous). When it does start to corrode, the byproduct is a white corrosion which is relatively lubricious. It's corrosion actually makes assembly, or more importantly, disassembly, easier.
Tim Martinplating shop - Springfield, Massachusetts
Q. I am glad I found these discussions on cadmium plating! After the recent scares from China I found I was not as well educated as I should have been. As I began researching building my own airplane I was at first horrified that all of the fasteners were plated with this toxic substance, so I started searching and found this forum. The airplane I'm going to build uses aluminum skin and formers but steel blind rivets to hold it all together. So now I know the cadmium plating is there to keep the two different metals from corroding and weakening which would result in me being dead pretty darn quick! I'll take my chances with the cadmium plating! OK, so my questions:
1.) When handling plated materials, I should wash my hands?
2.) What should I wash them in and with?
3.) When blind rivets pop they release a good deal of energy, should I wear a mask to keep from breathing any cadmium dust released?
4.) Am I taking this too seriously? I am looking at potentially 3 years of working with this stuff before I can paint it and reduce exposure. Thank you in advance for your insight.
- Marietta, Georgia, USA
June 13, 2010
A. Hi, John. Indeed it is very difficult for we in the finishing industry to not be totally cynical ...
After our decades of hard work on cadmium reduction and elimination, with so many small businesses closed down from environmental pressures -- we get to watch Wal Mart sell jewelry to children with up to 70 percent pure cadmium, and MacDonalds give away children's drinking glasses with cadmium paint. And all this jewelry and these glasses, with far higher concentrations of cadmium than plating shops struggle with, is allowed to be simply dumped in the general trash rather than requiring a secure land fill, as is required for plater's far more dilute cadmium waste. And it seems the EPA couldn't even be bothered with these Walmart & MacDonalds fiascos -- I saw not one word of worry for the children from EPA in the newspapers or on TV, let alone any requirement for Walmart or Macdonalds to retrieve this stuff and get it to secure landfills. The penny-wise pound-foolishness of our environmental regulations simply boggles the mind, but as a NJ Governor once said "Toxic is a matter of statute, not opinion" :-(
Even still, cadmium is a bio-accumulative toxin just like mercury and lead! So, yes, I'd wash my hands frequently if I were you, with regular hand soap. And I'd wear an N95 painter's mask when pop riveting -- although these measures might be more as protection against the hexavalent chromate conversion coating on the fasteners than the cadmium plating. Good luck.
Regards,
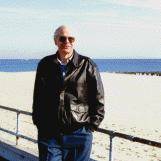
Ted Mooney, P.E.
Striving to live Aloha
finishing.com - Pine Beach, New Jersey
! I'm puzzled about a couple of things in the last response above, hope this topic is still of interest. The question was about steel pop rivet mandrels being discarded while pulling them in an aluminum aircraft structure. There is no cadmium anywhere except a very few plated nuts and bolts which are elsewhere. How can this result in any cadmium exposure? Is there in fact any significant human exposure resulting from handling cadmium plated nuts and bolts that have been barrel plated in a shop following good procedures?
Likewise, where does the hexavalent chromium come into the picture? I have not seen any kit aircraft parts using Alodine type conversion coating for a long time, it's mostly alclad aluminum or corrosion resistant alloys like 6061.
- Santa Cruz, California USA
March 21, 2012
A. Hi, David.
John implies that the rivets are cadmium plated steel; I can't see how you would put an unplated steel fastener (whether a rivet or a screw) in an aluminum aircraft skin -- so I am assuming that the rivets are cadmium plated steel, as he implies.
Cadmium plated hardware invariably receives a chromate conversion coating very similar to the "Alodine" coating for aluminum that you are familiar with.
I personally don't worry much about casual and occasional handling of cadmium plated hardware, but I don't think you will find authoritative studies on the subject, only educated guesses. And if California Prop 65 demands warning labels about this, I certainly can't claim they're wrong -- I'm no epidemiologist. If you do find such studies, please let us know, we'd like to link to them.
Regards,
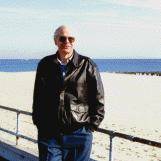
Ted Mooney, P.E.
Striving to live Aloha
finishing.com - Pine Beach, New Jersey
! This could easily drift away from finishing issues to aircraft structural issues, so I will try to focus my answer only on the materials/finishing ones.
I am not aware of any aircraft rivets for light aircraft that are cadmium plated. Solid aircraft rivets are almost always 1100 or 2117 aluminum in light aircraft construction, and may have a chromate conversion coating or be anodized. The coating is often damaged in the process of bucking the rivet, but some protection is provided. Common tubular pulled rivets ("pop" or more advanced kinds) are mostly aluminum, sometimes monel, stainless, copper, or (usually zinc plated) steel. The mandrel that's pulled through the rivet to form the "shop head" breaks off inside. Sometimes the retained mandrel forms part of the shear strength of the installed rivet while more conservative designers assume that the mandrel will fall out and do their testing accordingly. The finishing concern here is about corrosion over time of the (usually steel) mandrel, so some builders fill the open hole with something to be sure it's sealed by layers of primer and paint. When a steel (even monel or stainless) rivet is needed for strength in an aluminum part, sometimes the rivet is installed "wet" with a coating of zinc chromate paste to reduce the galvanic corrosion that can happen.
Common aircraft fasteners that *are* cadmium plated are all the screws and bolts made of steel, which may be bright cad plate (Cad I) or might have a chromate conversion coating (Cad II) on top of that. There is a page at OSHA www.osha.gov/SLTC/cadmium/ that refers mostly to hazards associated with cadmium plating chemicals and dust of the metal.
The only aircraft-related link I found was www.osha.gov/dts/hib/hib_data/hib19890221.html ⇩ which refers to an airline shop where workers were grinding cadmium-plated landing gear parts without ventilation. The OSHA limit is 0.5 mg ^5 µg per cubic meter, and if my arithmetic is right based on 0.0003" plating thickness and 8.65 g/cc for Cd, you would need to take all the plating off a typical large bolt head and make it into dust, for every cubic meter of air in your shop to reach that level.
After some years alleged Cad I plating sometimes exhibits dusty white corrosion. It's the wrong color to be cadmium oxide, my guess was always that the parts were actually zinc plated. What else could it be? Could this be toxic?
- Santa Cruz, California USA
April 2, 2012
Ed. note: Very informative posting, David! However, even the "bright cad plate (Cad I)" probably has a chromate conversion coating on it.
Ed. update: Please see next posting regarding the 0.5mg which has been struck out and corrected to 5µg.
Ed. update Oct. 2024: The link to OSHA about grinding cadmium has broken. Thankfully, the Internet Archive preserved a copy here
Please consider a donation to The Internet Archive! -- in an age where internet pages simply disappear and the information is forever gone in "1984" Newspeak-style, this non-profit, dependent upon volunteer labor, is our principal line of defense, and they are currently under very costly attack by the scummy RIAA.
!! For clarity on personal safety I believe the post on 2 April 2012 is dangerously wide of the mark. The OHSA PEL for Cd is 5µg - not 0.5 mg - per meter cubed of air, averaged over an 8-hour period. So that amount of cadmium dust would be extremely dangerous if inhaled, even in a minute quantity.
The current (2018) WEL in the UK Is 0.025 mg per cu m averaged over an 8-hour period.
- West Mids, UK
March 8, 2019
Dementia from cadmium ingestion?
Q. My brother claims he used cad coated screws while refurbishing airplane seats back in the mid-sixties. In order to get greater productivity he held extra screws in his mouth. Now he says he "got a bit of a high" from it, but is it possible that he actually got some form of cad poisoning? He is now 69 and experiencing multiple health issues including dementia. From what I have been able to learn, it is more about inhalation or direct ingestion that toxicity occurs. Any thoughts on this?
Darleen Page- Bellingham, Washington, USA
January 20, 2015
by World Health Organization
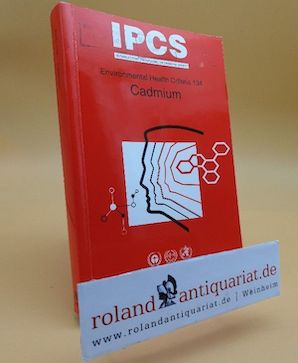
on eBay
or AbeBooks
or Amazon
(affil link)
Hi Darleen. Sorry for your brother's troubles.
I'm not aware of any psychoactive materials in cadmium plated screws, so I'm not confident that this is what he was getting a high from; maybe there were solvents in the area.
A doctor could test him for cadmium and/or chromium in his blood, but I rather doubt that it would reveal anything all these years later (speaking as a layman; I have no medical, diagnostic or lab skills).
Sadly, we don't live forever -- we all start getting sick in different ways as we age, and you don't need cadmium exposure to get dementia or other health issues. So, while it's certainly possible that the cadmium or chromium was an issue in his dementia, I don't think it's probable. Best of luck.
Regards,
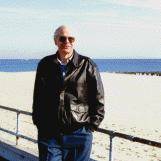
Ted Mooney, P.E.
Striving to live Aloha
finishing.com - Pine Beach, New Jersey

Q, A, or Comment on THIS thread -or- Start a NEW Thread