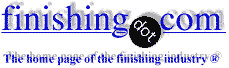
-----
Salt Spray Failure of Sulfuric Anodizing only on some alloys
Q. We're a small one-stop jobshop that deals almost strictly with aluminum from sheet stock to final product out. I am the QC for our processing room and I have a problem that I just can't seem to solve on my own:
We've received a second failing salt spray test for our 7075 alloy while our 7050 alloy barely passed it's monthly salt spray testing. 2024 and 6061 alloys are consistently passing with 0 pits on all five test panels. panels are salt sprayed in accordance withASTM B117, 5 3"x10" panels in each set. Coating weights, coating thicknesses, bath properties, cleaner properties, deoxidizer properties, and seal properties have changed significantly when graphed for the past 6 months, but for about 3 months our pits have been climbing 3-4/month until our failures. Only aluminum is processed through these baths. The pitting must be alloy specific somehow to only be attacking the 7000 series alloys, and the pits are fairly large and isolated.
I don't seem to be gaining ground thus far, so any help would be greatly appreciated!
- Ponderay, Idaho, USA
2002
A. You've got contamination, instruments are out of calibration or someone is letting you down. Do all of the following YOURSELF (don't take anyone else's word for it).
(1) Check the quality AND concentrations in your salt spray solutions OR Make them up fresh from NEW chemicals.
(2) Test the anodising, seal, rinse water and salt spray make up water for chloride/phosphate content.
(3) Check the calibration of all pH meters with NEW buffer solution(and check how the operators do so). This is especially important for seal pH and salt spray pH.
(4) Calibrate all temperature instrumentation especially for anodising, seal and salt spray.
(5) Graph the analysis figures for the anodising and seal tanks. Examine for consistency and ensure that they tally closely with the additions that were made (or written down as made).
(6) Ensure that test pieces are orientated correctly in the salt spray cabinet, that the air/water pressures are correct and that the test pieces are not being contaminated in the preparation process (e.g., cutting fluid, corrosives, contaminated bench etc).
(7) Get samples of your stock aluminium analysed for composition vs recommended composition.
(8) In the long term you badly need to introduce an SPC system (Statistical Process Control) to monitor trends in real time and tally them with additions made & historical trends (Remember, you are 'Watching' the 'Watchers').
(9) NOTE: If you haven't got SPC you need to go on a short course RIGHT NOW. It will move your function from QC to QA. The distinction between QC and QA is critically important. It will mean the difference between firefighting and forecasting. At present I work to VDA-6 and TS 16949 standards. You need to work to at least ISO-9000 in this area.
(10)Best of luck - John
- Ireland
A. Have you tried using new panels. Some places throw away panels when they get to be 6 months old.
James Watts- Navarre, Florida
2002
Q. After some testing, I've found a rather high copper content in the anodize. I believe the source is our copper rods that the racks hang off of when they are anodized. I'm looking into getting them lead plated. Is this what other job shops do? Do they plate them or could one use a simple 70/30 lead/tin solder to protect? Is the copper the problem or would it not make a difference in the anodize tank?
Benjamin J. Curto [returning]- Ponderay, Idaho, USA
2002
A. Hi Benjamin. Lots of shops nickel plate or electroless nickel plate their anode rods and it seems to work well. I'd avoid lead whenever there is a good alternative, and I think nickel is one. Don't be cheap, put it on thick to avoid porosity.
Another thing a lot of shops do is put PVC or polypropylene drip shields over the anode rods.
Luck & Regards,
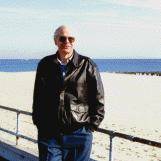
Ted Mooney, P.E.
Striving to live Aloha
(Ted can offer longterm or instant help)
finishing.com - Pine Beach, New Jersey
A. Salt spray failures may not always be processing source. But to address solution control, try maintaining your silicates at under 20-ppm when using dilute Chrome Seal.
Handling with clean gloves and holding panels by the 0.032" edges would prevent handling contamination.
You might want to inspect your panels before and after cleaning for evidence of corrosion and discard, re-lap, perform deep etch or when processed, permanently mark them prior to the salt spray and disregard them as rejectable pitting during your evaluation.
- Gardena, California
2006
A. Unfortunately, salt spray testing of aluminum alloy panels is little more than a joke. The actual parts aren't thrown out after 6 months, actual parts aren't held by the edges, actual parts aren't re-lapped, etc. :-)
The test says zero about the actual parts being processed and very little about the process line. It's mostly a test of how high quality, how new, and how carefully handled the test panels :-)
Luck & Regards,
Ted Mooney, P.E. RET
Striving to live Aloha
(Ted can offer longterm or instant help)
finishing.com - Pine Beach, New Jersey
Q, A, or Comment on THIS thread -or- Start a NEW Thread