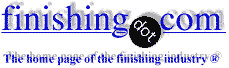
-----
Polishing of tool steel punches
Dear all,
I am looking for the following advice: -how to polish tool steel (punches and dies) having the following composition: AISI M3 (C=1.28%, Cr=4.2%, Mo=5%, W=6.4%, V=3.2%) -which method do you suggest: electropolishing, chemical polishing or other.
Thank you in advance,
- Cape Town, South Africa
Other. I am biased because we make small vibratory equipment; however, we have sold a number of systems to companies who need to primarily polish drill and end mills.

AF Kenton
retired business owner - Hatboro, Pennsylvania
Mira:
I understand Mr. Kenton's opinion, but I have my doubts about the suitability of any of the mentioned methods, specially if the volumes are low and the diversity is high. This will probably sound third-world-like, but polishing by hand or hand tools by professionals is still a dominant technique for molds, stamping dies, etc., even in first world countries (obviously expensive due to salaries). As long as you can maintain sharp edges and afford the initial investment in equipment, you can go to vibratory, otherwise find a good mold polisher in town.
Monterrey, NL, Mexico
This is a little more info for both Guillermo and the originator of the question. Wood media is the secret to the finish.

AF Kenton
retired business owner - Hatboro, Pennsylvania
Mr. Kenton:
Punches, dies or mold components can be very irregular and somewhat big (sometimes up to 20-30 lbs and up to 6-8 inches or more). I am under the impression that vibratory is for small items. Am I wrong? Can parts this big be run in vibratory equipment, or what are the size and weight limits? Also, what level of geometry precision and roughness can be achieved? Can you stay within say
0.0002" tolerance and attain 2 microinch RMS. What about metal loss in sharp edges, how is sharpness related versus surface removal?
Thanks in advance for your patience and kindly enlighten us all a little more about your specialty.
Monterrey, NL, Mexico
Part size or drill bit is determined by the size of the machine; however, look at the channel width of a vibratory bowl to determine your proper length. Length of part should not exceed channel width. Our 1 cu.ft. machine can take a part up to 7.5" properly but will work parts up to 15"+ -, but at that length part will be touching ID or OD as it is being worked.
As your parts get heavier, you do need to use a larger proportion of media to parts. Also the larger the size of the media the better. For polishing, you want to use at least 80% media to parts by volume. I can not give you any info on measurable differences that result from working drill bits with wood shapes and organic compound. All I can tell you is that we have sold this equipment and processing to at least 2 or 3 companies for this purpose. Test samples I ran showed no signs of dulling sharpness, but did achieve jewelry like appearance.

AF Kenton
retired business owner - Hatboro, Pennsylvania
March 12, 2009
Hello,
I am currently working on a project to achieve a high polish (5 Ra or better) on small surfaces (.500" or smaller) of tool steel similar to A2.
The surface is machined to a Ra of about 15 in the hardened state. I have tried using several mass finishing techniques to achieve the 5 Ra. These techniques were unable to completely remove the machining marks, but came close to the finish needed.
Questions:
- Are there any recommended processes other than hand polishing that would remove the machine lines prior to mass finishing?
- Would it be more beneficial to machine in the soft state and work with the machine lines prior to heat treatment?
I appreciate any advice.
Engineer - St. Paul, Minnesota
If you are still getting machine marks and line prior to polishing then you need more cut down. The faster method is via ceramic media in a wet process using mass finishing equipment. To achieve the finish you are looking for, I'd recommend a 2 step dry process after the lines or marks are gone. There is a dry organic abrasive mix we sell called 6A. It does a good job of improving the surface finish and leaves the part with a glass bead appearance without the dimples. Follow this with a treated material, our 6E, for a long enough period of time and you can get close to a 12 RMS.

AF Kenton
retired business owner - Hatboro, Pennsylvania
March 16, 2009
Q, A, or Comment on THIS thread -or- Start a NEW Thread