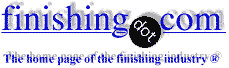
-----
Plating Problem: Blisters when Heated
Good day Sir,
Q. At present we are having problems on our products, we are encountering blister or bubbling of the plated layer after the units were subjected to Temp Cycle with approx. temp of -65 °C and 150 °C. The blister problem is not evident right after plating. One of our suspect is the stamping oil which is used as a lubricant to manufacture the frames. Result of our EDX analysis showed that the pricked blister samples has a high amount of carbon. While result of FTIR analysis showed that there was no difference in terms of carbon-chains between the blister-affected samples and those that were not affected. Signifying that the contamination from the samples are either already well spread or there were no contamination at all, since there were no difference. What do you think is causing this blister problem? Perhaps you could suggest some things that we could look into, and dig deeper on the causes of this problem.
Hopefully your staff could accommodate my inquiry. Thank you very much and best regards.
Nats Pogi- Philippines
Hi, Nats. You haven't really told us much yet, like what the substrate is, what cleaning and activation sequence you are using, or what you are plating it with! Blistering upon baking is not always due to some mysterious material leaching out, and can simply be that adhesion is marginal and heating emphasizes the fact.
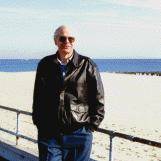
Ted Mooney, P.E.
Striving to live Aloha
(Ted can offer longterm or instant help)
finishing.com - Pine Beach, New Jersey
A. It is very important that surface is clean before you start plating. Do you anodically degrease your product? Do you rinse it well after that? Do you give any acid dip before you start plating?
If hydrogen is trapped in base metal, then also you can get blister. Do you degas product at desired temperature before you plate? Try those alternatives and see if they help.
Good luck.
Payal Mag- Charlotte, North Carolina
In order to try to answer your question the following information is needed: What type of plating. What substrate. What is the finishing cycle.
Gene Packmanprocess supplier - Great Neck, New York
Q. Attention: Ted Mooney, Payal Mag, Gene Packman
Sirs, thank you very much for replying to my inquiries. To fill in the holes in my letter here it is:
1. The substrate we're using is Cu, the material is CDA 151
2. As for the electrocleaning process, were using 30 g/l NaOH for the removal of organic contaminants and 22.5% Sulfuric Acid as our Activator Chemical. The dumping frequency for both chemicals is monthly. The effective length of cell is 1.5 m for Electroclean and 4.8 m for the Activator.
3. Yes we anodically degrease our product, and rinse it after that. We employ predip prior to plating which is MSA at a concentration of 20%.
4. The plating line is strip-to-strip, as a finishing cycle, we have drag out rinse, neutralizer and Deionized Water Rinse, Blower and Drying.
Hoping for your immediate response. Thank you.
Nats Pogi- Pasay City, Philippines
A. Dear Nats Pogi,
Blistering in spot silver plating of lead frames is almost always caused by silver immersion plating onto the copper before the rectifier is turned on. Some suggestions are to increase the amount of anti-immersion chemical in the silver bath. Decrease delay time between pump turning on and rectifier turning on. Pulse plating at 30 percent duty cycle is normal to improve silver uniformity adjacent to mask edges.
If there is any segregation of the Alloy 151 components, a copper strike helps provide a consistent surface for spot plating.
Good luck,
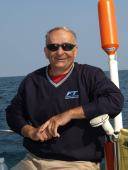
Pat Mentone
St Paul, Minnesota
A. I think Pat gave you the right answer to the problem, but if not, then if your cleaner is simply caustic soda ⇦liquid caustic soda in bulk on Amazon [affil link] , you probably should be using a proprietary cleaner with detergent in it. Also the cleaner may not be hot enough.
You must make sure that there is no silicone in the stamping area or used in the machinery as most cleaning cycles are not capable of removing it.
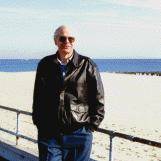
Ted Mooney, P.E.
Striving to live Aloha
(Ted can offer longterm or instant help)
finishing.com - Pine Beach, New Jersey
August 3, 2011
A. Dear Nats Pogi,
Have A Great day,
This type of blister is mainly due to insufficient bonding of zinc over the base metal,
The first cause for Blister is due to improper cleaning of base metal, according to your above specification, I don't find any problem.
I suspected on the additive you added in plating solution, basically this imbalance in this additive may cause this type of issue.
In India we use Brightener and booster as additives, in this excess won't cause that much problem practically, but less brightener and excess booster would definitely cause this issue.
For this, put hull-cell for the plating solution; after hull-cell note down the plating thickness from HCD to LCD if the distribution is 1:1.5 that would be correct. if not, some imbalance in additives or you could check it in XRF method.
- CHENNAI, India
Silver plating blisters only on inside of brass bushings
Q. Hello Everyone,
I am trying to do Silver Plating of nine microns on my brass bushing having diameter of 9 mm, length of 6 mm and hole of 5.3 mm but the problem is that after plating when I heat them at the temperature of 300 °C, bubbles are formed inside the hole. Now my customer is having problem with that he says there should be no formation of bubbles when he heats it at about 300 °C
Please help to get this plating right so that after plating, upon heating there are no bubbles in holes.
Thanks
- Jamnagar, Gujarat, India
May 18, 2013
A. Hi Gaurav. We appended your question to a thread which suggests to me that the problem may be lack of electrocleaning inside the bushing. That, of course, leaves you with trying to find a practical solution.
If these are very expensive, highly specialized parts, perhaps you can afford to run a tiny brush with powdered pumice through the hole before processing. If not, it is possible that ultrasonic agitation in your soak clean or electroclean tank will help. Good luck.
Regards,
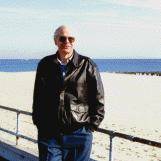
Ted Mooney, P.E.
Striving to live Aloha
(Ted can offer longterm or instant help)
finishing.com - Pine Beach, New Jersey
May 21, 2013
Q, A, or Comment on THIS thread -or- Start a NEW Thread