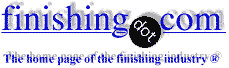
-----
Magnesium electropolishing and annealing
Q. I have a follow up question regarding the electropolishing of Mg alloy. What kind of holder design is being used if the sample wire/coil need to be completely immersed in electrolyte along with holder?
HK- Stuttgart
August 21, 2025
Tip: This forum was created to help build camaraderie through sharing tips, opinions, pics & personalities.
The operator & those readers who want that might not engage with anonymous posters.
A. Hi.
It would depend on what formulation is used for the electropolishing solution. But for the standard solutions used in electropolishing of stainless steel, copper racks are usually okay, although it's best to plastisol coat them. Platinum-clad titanium can be used on rack tips in almost any solution, with the remainder of the rack being plastisol-coated copper.
Luck & Regards,
Ted Mooney, P.E. RET
Striving to live Aloha
(Ted can offer longterm or instant help)
finishing.com - Pine Beach, New Jersey
⇩ Related postings, oldest first ⇩
by Dow Chemical Co.
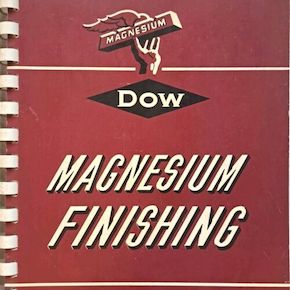
is sometimes available on
AbeBooks,
eBay, or
Amazon
... but if not, you can find libraries which have copies on WorldCat.org
(affil link)
Q. Hello,
I am studying the growth of fluoride and oxide films on magnesium and am having a few problems with surface preparation. I am using pure (99.9%) Mg foil and start the processing by cleaning and degreasing.
Two problems 1) Electropolishing seems to always leave the surface pits or undulations. I have tried several different recipes, and have had the best luck with ethanol saturated with sodium thiocyanide, electropolished at constant voltage (35 V) and done at low temp (0 °C). This is still not satisfactory, even by eye (I want a smooth mirror finish). I have good luck electropolish Al with a galvanostatic method, but cannot reproduce with Mg. Suggestions? 2) I would like to quantify the effects of annealing on the grain boundaries. I understand that one can make the boundaries visible via chemical etch but have had no luck finding specifics. Currently I am annealing under nitrogen/hydrogen at 350 ° C for around 1/2 hour.
Any Help is much appreciated!
Thank you,
Kevin Hobbs- Norman, Oklahoma
2002
A. Hello again,
I suppose I am going to partially answer my own question here but I should report that I have improved on the electropolish situation by including a sulfuric acid pickle in my preclean. I am now able to get a mirror finish by eye, although some imperfections are still visible under the optical microscope. Suggestions are still welcome. ⇐ answer?
Thanks again,
Kevin Hobbs [returning]- Norman, Oklahoma
Q. Hi,
I have problems in EBSD (electron-backscattered diffraction) analyses of as-cast (partially wrought) Mg alloys. The problem is that the surface is microscopically bumpy after chemical polishing. Mechanical polishing, finished with the OP-S solution, also doesn't work. It seems that it has to be electropolished. I am wondering if anybody has electropolished as-cast Mg alloy. If so, I'd appreciate the polishing conditions including the solution, voltage, and temperature. Thanks a lot.
Faramarz ZarandiMcGill University - Montreal, QC, Canada
2005
A. Dear Mr. F. Zarandi,
I had the same problem as you mentioned to find out the solution, time and voltage for electropolishing of twin-roll cast Mg alloys. I found the solution of 15% Nitric Acid in Ethanol, 12 V for 10-15 seconds works properly. Bear in mind that the temperature of this electropolishing stage must be as close as possible to -30 °C. This is very important issue: otherwise, due to the heat release during mixing of Acid with Ethanol, explosion might be possible. The 30% Nitric Acid in ethanol might be a good solution for Mg electropolishing but I haven't tried it before.
Good luck,
- London, United Kingdom
July 30, 2010
Q. Hello Sir,
I am doing electropolishing of Mg alloys myself. May I ask you what temperature you use? I am using -45 to -55 °C myself, with 90V using a Strueres Tenupul system.
⇐ answer?
Thank you
PhD Student, Graduate School of Pure and Applied Science, University of Tsukuba
Research Assistant, Nano-Structure Analysis Group
Magnetic Materials Center- Tsukuba, Japan
January 24, 2012
Q. Sir,
I am working on Mg alloy system. I am using orthophosphoric acid and ethanol (3:5 ratio) as electrolyte and SS cathode. I did at 3 V for 30 sec and 3 mins at 1.5V. I am not getting a surface for EBSD.
⇐ answer?
- Nagpur, Maharashtra, India
June 20, 2017
Ed. note: Our FAQ on "Finishing of Magnesium" includes an electropolishing formulation which readers may wish to review.
Q. Hi there,
I am electropolishing 0.2mm diameter magnesium wire to improve its surface properties as part of my final year university project.
I currently use aluminium cathodes, 5 parts ethanol to 3 parts 85% phosphoric acid electrolyte to polish at 2.5V. It polishes very effectively but I have no idea how to tell if the solution has aged too much.
I have read many incredibly helpful threads on this website that explain how to tell when the electrolyte needs replaced/filtered/decanted but they mostly refer to sulfuric/phosphoric acid baths for steel. As the wire is so fine and I don't have access to an SEM or an AFM, I have no way to tell quantitatively or qualitatively using the wire, when the electrolyte has aged too much or is working less effectively.
Would anyone be able to assist by suggesting ways I could measure if my electrolyte has aged too much for this particular setup? Or just any advice regarding how to preserve the solution to keep optimum polishing conditions as long as possible or even just best practices.
⇐ answer?
Kind regards
Mikey
- Glasgow, Scotland
July 6, 2021

Q, A, or Comment on THIS thread -or- Start a NEW Thread