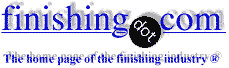
-----
Chrome plating tank doesn't work
Where did I go wrong? I am setting up a commercial chromium tank. The tank size is about 198 lits. The requirement by our customer is CrO3 :236 gm/l and H2SO4 is 2.38 gm/l. The calculation would be for the tank is CrO3 is 50.49 Kg and H2SO4 is 471.24 cc.
But after mixing and heating up to 55 deg. C and placing the cables connection correctly and leaving for a day before plating I was hit with no chrome been plated on the steel metal. I did a reverse etch in the same tank for a second before plating. The current density was 30A/dm square. The steel plate was plated for 6 hours. Where did I go wrong?
Thank you,
CHOY PETER- Singapore
One second of reverse etch sounds like too little to accomplish anything, but that's not really the problem. Did you generate a lot of hydrogen on the parts? What kind of anodes did you use and what is their condition during plating: orange, chocolate color, etc.
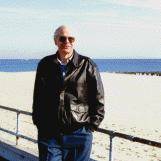
Ted Mooney, P.E.
Striving to live Aloha
(Ted can offer longterm or instant help)
finishing.com - Pine Beach, New Jersey
I have checked your calculations and do not agree with them. If your tank is 198 liters and you want 236 g/l CrO3, you need 46.728 Kg, not 50.49 Kg. Secondly, and more important, you have correctly calculated the weight of sulfuric acid, in as much as you need 471g., but you have not correctly converted it to a volume. The density of sulfuric acid is 1.84g/ml (assuming it is concentrated H2SO4), so you only need 256ml. Excess sulfuric acid can be removed by adding barium hydroxide and filtering off the precipitated barium sulphate. However, this needs to be done very carefully and strict control is needed. Other reasons for no plating can be contaminated workpieces, poor temperature control or poor electrical connections.
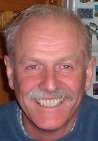
Trevor Crichton
R&D practical scientist
Chesham, Bucks, UK
Your maths are wrong . By my calculations you should only have used 47Kg. CrO3 and 238 mls (cc) of sulfuric acid. The high chrome is not a problem but the high sulfuric is . You will have to reduce the amount of SO4 in the bath by addition of either barium hydroxide or barium carbonate or dilute the bath by half ( throw half away - store for topping up at later stage) and then just add CrO3 to make up the difference.
55 it too high a temp . Lower to 40 -45 and you should also add some fluoride . Best bet is to talk to one of your local suppliers.
Plating problems are rarely one thing - its usually a combination .
Best of luck.
Jim MaguireWMF - Birmingham UK
What was the analysis of the tank? Chrome will plate over a very wide range of concentrations and voltages, so no chrome, zero, indicates that the electricity did not get to the part or the anode. Since you have amperage, you possibly have a short or used far too small wire or bar to carry the current. Voltage will give some clue. If it was under 1 volt, you have a short. Normal plating will take place at about (many variables) 4 volts.
James Watts- Navarre, Florida
Dear Ted Mooney,
To answer your question.The anodes are 7% tin and balance lead.There are 4 corrugated anodes on both sides of the process tank. The colour of the anodes on both sides are chocolate in colour. The mat'l that is to be plated is 4340 bar stock. The mat'l are new. Please explain how I can generate lots of hydrogen.
Thank you
Dear Trevor Crichton,
Thank you for the correct calculations, will correct it. There is one strange thing while I was checking through your advise. I was checking the cables from my 3000 amps recitifer at the anode which reads positive and the cathode was negative using a tong meter but along the cables after the mid way point the anode reads negative and the cathode reads positive. All terminal had been rechecked again. The cables length is 41 meters and the cable can take 280 amps. My H2SO4 is 98 % con. The specification given to make up the commercial chromium is CRO3 is 236 gm/l and H2SO4 is 2.38gm/l. What if I can't using the chemical that is out of range? What will happen?
Thank you.
CHOY PETER- Singapore
Choy,
I bet you turned over your tong meter when the ± changed. If it is a hall effect meter, it will read positive one way and negative when turned over. Try it on a vertical run.
41 meters--WOW- Your line loss will be astronomical. Cut in a voltmeter and an ammeter near the tank. PS, 280 amps at 4 volts is a lot less than your 3000 amp power supply. If this is really a total of 280 amps, the power supply better be 3 phase or your ripple will be outside of where chrome will plate, regardless of it being filtered and choked.
James Watts- Navarre, Florida
I was inferring that since 90 percent of the rectifier energy goes into liberating hydrogen rather than depositing chrome, you should see very liberal generation of hydrogen if things are working correctly. I believe the other responders were more informative than I was, i.e., the 100:1 ratio of chromic acid to sulfuric acid has to be almost exactly right for the chrome plating process to work at all--it's not just an additive it's a critical catalyst for the reaction.
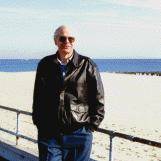
Ted Mooney, P.E.
Striving to live Aloha
(Ted can offer longterm or instant help)
finishing.com - Pine Beach, New Jersey
Dear James Watts,
Had my analysis back. The CrO3 is 278.996 and the SO4 is 2.4 g/l. I had also cut the cables shorter to 15 meters but the ± is still the same. I had plated a scrap piece of part and the colour was dull, matte finish. It took 1 hour about 21 microns thickness to plate , this was before I had the analysis results. I will proceed to adjust the solution 100:1. Should the finishing of the chrome after plating be bright shine finish or dull matt?
Thank you,
CHOY PETER- Singapore
I have had a similar problem dull finish but good coverage and no build up after an hour at 100/1 ratio, my main concern is the strength of the sulfuric acid we are using battery acid ⇦ on eBay or Amazon [affil link] which is only about 25 or 30% concentrate.
Bruce Attwater- Grafton, NSW, Australia
2006
Q, A, or Comment on THIS thread -or- Start a NEW Thread