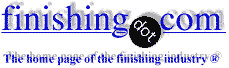
-----
Current, outdated & obsolete specs -- Better to specify revision level or say "current revision"?
How to find which MIL specs are obsolete or superceded
(2002)
Q. IS THERE A WEB SITE THAT I CAN GO TO THAT WILL SHOW ALL OBSOLETE MIL SPECS WITH THE SUPERCEDED MIL SPEC?
KAREN AGUIRRE- LAVERNE, California, USA
A. Karen -
Check the Global Engineering site. You can type in the old designation, it will tell you if it's obsolete and, if there is a replacement, that will also be indicated. They are also very helpful over the phone.
Cynthia L. Meade- Sylvania, Ohio, USA
2002
A. Give this link a shot: stinet.dtic.mil/str/dodiss4_fields.html. It is a search page that you can look up Mil standards. It will show when a document is obsolete and there are also links to the actual document.
- Redwood Falls, Minnesota, USA
2002
----
Ed. note: That site is still active (Dec. 2014), but the referenced page is now a broken link. We're not confident that it is a good site for the purpose of identifying current vs. obsolete plating specs anymore.
Finishing.com uses Techstreet for specs, and it identifies whether specs are current or obsolete. But, being a commercial site, military specs are not free like they are at quicksearch.dla.mil/
Regards,
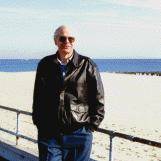
Ted Mooney, P.E.
Striving to live Aloha
(Ted can offer longterm or instant help)
finishing.com - Pine Beach, New Jersey
December 2014
What info should you expect on certs from plating shops?
baQ. When requesting material certifications from plating suppliers, specifically zinc plating w/ chromate w/ sealer, what information would you expect to see and is there a standard form that is used in the industry.
Peter Woodworthconsumer security containers - Rochester, New York, USA
2003
A. This answer may not help you too much, Peter, but the thing is, it's the product designer's job to specify the plating; it's not the plating shop's job. The plating shop simply certifies that it has done the plating that was requested.
Here is a real-world example of what I am talking about, and it happens all the time: a part is plated and it fails because it was not given a hydrogen embrittlement relief baking. The designer says "you didn't bake it and you were supposed to". The shop says "no, soft steel doesn't need baking and we don't bake most parts; if this was hardened steel, you should have specified baking and we would have charged you to do it".
Aerospace manufacturers, automobile manufacturers, and medical instrument manufacturers tell the plating shop exactly what to do--the plating shop doesn't tell them what they're going to provide. Smaller manufacturers, working with less critical parts, are less familiar with plating and tend to rely on the expertise of the plating shop. But this can be dangerous because the shop knows the customer will often go with the cheapest source, so they are not going to volunteer themselves into the cost of complying with a spec that their competitors won't be including in their bid :-(
Another thing that can happen is the customer specifies something vague like "commercial zinc plate" expecting this to mean a minimum of .0002" because one shop tells them that's what it means; and another shop then plates .0001" and claims "commercial zinc plate" just means "complete coverage" :-)
The sad news is that you have to specify the coatings and the performance criteria. If you don't have enough experience with plating to do that, you have to call in a finishing consultant to sit down with the product designer and educate him/her sufficiently to get a good spec written, or at least work with multiple plating shops to write a spec. Then the certs that the shop supplies will certify compliance with the spec you told them to plate to.
Good luck!
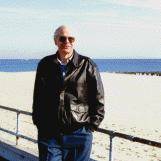
Ted Mooney, P.E.
Striving to live Aloha
(Ted can offer longterm or instant help)
finishing.com - Pine Beach, New Jersey
2003
Q. In regards to corrosion resistance. Is there a good guide book or reference manual, that could be used as a guide for understanding corrosion and subsequent plating alternatives with performance specifications such as hours of salt spray resistance or high alkalinity resistance.
Peter Woodworth [returning]- Rochester, New York, USA
2003
A. Between your first question and the second, it truly sounds like your organization is really in need of someone who knows the surface finishing field. For a start, you might try searching on this website for some education/training outfits, or at least look at the library recommendations here.
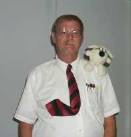
James Totter, CEF
- Tallahassee, Florida
2003
A. Zinc finishes are specified in ASTM B633 Types I-IV. Check out this cool link which lists free of charge most common surface finishing specs: http://www.engineersedge.com/finishing.htm
Process suppliers of Zinc Chemistries and many plating shops have established recipes that pass a multitude of accelerated life tests such as salt spray, etc., and will certify to it.
These certifications are generally traceable to an independent testing lab.
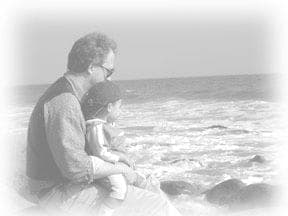
Dave Kinghorn
Chemical Engineer
SUNNYvale, California
2003
That's a great link, Dave--thanks! But I have to disagree with its preface that "Often MIL, AMS, and other controlled specifications are not required...". Metal finishing should always be done to a specification. Poorly specified metal finishing requirements like "commercial zinc plate and yellow" are meaningless, and constantly lead to trouble.
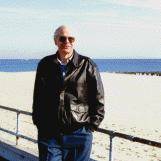
Ted Mooney, P.E.
Striving to live Aloha
(Ted can offer longterm or instant help)
finishing.com - Pine Beach, New Jersey
2003
December 10, 2014
Q. I am trying to indicate a standard that dictates how a plating or coating specification is called out within the notes.
Example:
Finish: "Anodize, Black, per MIL-A-8625F, Type II, Class 2"
Versus "Anodize, Black per latest revision of MIL-A-8625, Type II, Class 2".
My opinion is to call out the standard with the revision that was used in the creation of the finish, plating or coating so there is no ambiguity on the intent or purpose to the coating. My fear is the plater may not have the "latest revision" or even worse, the intent changes at a later revision.
Some within my organization that placing "latest revision" will fix any errors or future changes similar to changes resulting from RoHS compliance.
Any thoughts would be greatly appreciated.
- Bedford, Massachusetts USA
A. Hi Brian. I personally believe your approach is the better one, both for the reasons you mentioned, and because the alternate approach causes more problems than it cures.
For example, suppose you had specified Chromate Conversion Coating per "latest revision of MIL-C-5541". is MIL-DTL-5541 the latest revision of MIL-C-5541 or is it not? While most might say yes, some might say no, and now you don't have uniformity.
Similarly, many MIL specs were superceded by AMS specs -- what then? And in a couple of cases, the supersede was later rescinded. If someone followed the path to the AMS spec as superseding the MIL spec, and the AMS spec mentions no further updates or reversion to MIL spec, how can we fault them for sticking to the AMS spec? Way too many potential pitfalls to "latest revision" in my opinion :-)
Regards,
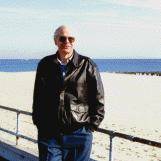
Ted Mooney, P.E.
Striving to live Aloha
(Ted can offer longterm or instant help)
finishing.com - Pine Beach, New Jersey
December 2014
![]() |
December 10, 2014 Q. Hi Ted, - Bedford, Massachusetts USA A. Hi Brian ![]() Geoff Smith Hampshire, England December 11, 2014 |
The problem here is we want to have our cake and eat it too.
If the future revision fixes a problem, we want the producer to automatically use the revision.
If the future revision removes or ruins the very thing that we are actually using, we want the producer to keep the old version. (Note: if this happens you should notify the source of the standard, oftentimes they will accommodate you and restore it in the next revision.)
If the producer only has an older/newer copy but the revision didn't affect the section we are using, we want them to be able to use what they have. (I bet a lot of them do this anyway.)
If the future revision provides a BETTER method (cheaper, less hazardous, etc.) with equal/better results to the process originally asked for, then we want the producer to... (???)
Probably the ideal thing would be to provide a range, acceptable to use revisions X through Y, and then review it regularly and keep that callout up to date as new revisions are released.
I think what actually happens 99.9% of the time is the part drawing lists whatever the current revision was at the time (better the devil you know than the devil you don't), and ten or twenty years later when somebody says "it would be a lot better if we can use the up to date version of this", they are usually told changing the drawing is not possible because it would take six months of red tape to approve and we don't really care just make the damn part to what the drawing says.
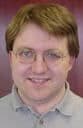
Ray Kremer
Stellar Solutions, Inc.

McHenry, Illinois
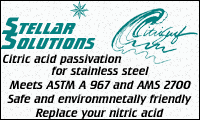
Q, A, or Comment on THIS thread -or- Start a NEW Thread