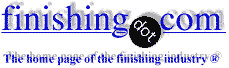
-----
Sand blasting standards: Swedish SA 1, SA 2, SA 2.5, SA 3 vs. NACE and Ra
< Prev. page (You're on the last page of this topic)
Q. I understand from reading the posts that we need to differentiate between surface cleanliness and surface profile.
An earlier post indicated that surface profile can be related to overall DFT.
Are there any guidelines as to what surface profile should be provided for differing DFT's?
Also, I see specifications from customers that stipulate different Ra ranges for carbon steel and stainless steel for the same paint system and DFT - why is this appropriate if the DFT is consistent?
- Manchester, United Kingdom
February 14, 2015
A. Hi Rob. One thing to keep in mind is that a thick coating on a very smooth surface does not stick as well, in many cases, compared to the same coating on a lightly roughened surface due to a smaller surface/contact area. Therefore, if adhesion is critical and the coating is fairly thick, 63 Ra or higher may be appropriate. On the other hand, if a given coating is very thin, perhaps a very fine finish such as 8 or less will work fine. Another example is a case where visual differences are desired. If a thin coating is placed upon a highly polished surface, the article will possibly look very different (shinier) than a case where the same coating is placed upon a mill finish or roughened article. However, if the DFT is quite high, the underlying Ra is less noticeable. After plating, the surface roughness should not change very much in most cases.
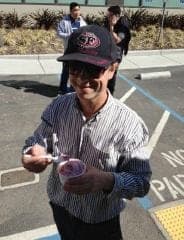
Blake Kneedler
Feather Hollow Eng. - Stockton, California
March 18, 2015
A. Hi Guys
Surface Roughness and Paint Thickness (DFT) is proportional to each other. when we paint shop primer the requirement of DFT is 20 microns. We cannot apply on 70 Micron Roughness surface. Because it gives you high paint consumption. Same thing reflects for high thickness paint. Also, the adhesive effect is not good.
- Madurai Tamilnadu India
May 23, 2015
Q. Dear sir.
I want to know about SA-2.5 & SA-3 profile of sand blasting because I don't have the SSPC standards
at present.
PES Consultants - Skardu, Pakistan
March 21, 2015
May 2015
A. Hello Ali. Bijat has told us:
- NEAR WHITE METAL, NACE No. 2/SSPC-SP10, SWEDISH Sa.2.5
- Near White Metal - Mill scale, rust and foreign particles are removed to the extent that only traces remain in the form of spots or stripes. The cleaned surface will show varying shades of grey. - WHITE METAL, NACE No. 1/SSPC-SP5, SWEDISH Sa.3
- White Metal - Visible mill scale, rust and foreign particles are entirely removed. The cleaned surface should have a uniform metallic colour but may show varying shades of grey when viewed at different angles.
Sanjay had told us:
- white metal (SP5) SA 3
1st quality
grade 1
- near white metal (SP10) SA 2.5
2nd quality
grade 2
And I have told the readers that --
HMG Paints Ltd. offers a free 24-page PDF with pictures of these surfaces at:
https://www.hmgpaint.com/knowledge-base/pdf/KNB0026.pdf
But that ISO 8501-1 is probably the best reference. Let us know if you seek something further, but clearly you can offer no certification and make no claim of compliance until you have obtained the standards.
Luck & Regards,
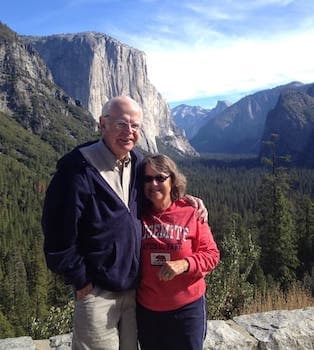
Ted Mooney, P.E. RET
Striving to live Aloha
(Ted can offer longterm or instant help)
finishing.com - Pine Beach, New Jersey
Dear Sir,
Thanks a lot for providing such informative things.
PES Consultants - Skardu Pakistan
May 26, 2015
A. As far as any blasting I have done in the past the SSPC SP 10 was considered a white blast...
As far as profile, we were always asked to get a certain average Mil reading usually about 2 mils was a 30 grit sand which is pretty fine. If we used a 16 grit we could get up to a 10 mil average profile.
When You are reading mil thickness on paint, however, the peaks will have less mil thickness due to paint flowing to the low spots. If you use a really rough sand, ex. 16 grit, you will get a lower average mil reading when checking the coating thickness. If you are trying to get a wet mil thickness this even makes it lower because the wet mil gauge will only measure from the highest spots. An electronic Mil Gauge is a bit more accurate but still reads less than the actual mil thickness due to peaks and valleys. I hope this helps anyone wondering about why you may not be getting the proper mil thickness after coating the blasted metal.
If you try to save time blasting by using a really coarse sand, you can actually cost yourself a lot of money later when trying to achieve a certain mil thickness with an expensive coating.
Dave FreerFreer Specialty Coatings - Great Falls, Montana, U.S.A.
June 6, 2015
Q. As I know, if we talk about roughness after blasting, we should refer to ISO 8503-1.
If we talk about surface cleanliness from rust, we should refer to ISO 8501-1.
Sometimes no tight correlation between SA and millimicron.
Is it correct?
united tractors pandu engineering - Cikarang, West Java, Indonesia
July 1, 2015
July 2015
Hi Dwitas. Yes, that is my understanding exactly.
Regards,
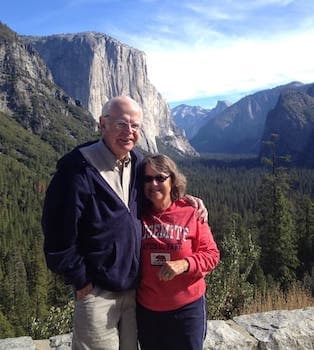
Ted Mooney, P.E. RET
Striving to live Aloha
(Ted can offer longterm or instant help)
finishing.com - Pine Beach, New Jersey
Q. Dear Sir,
Will you Please Clarify the Following Queries:
1) As a Practice and associated, can we mention DIN 55928 for Sand Blasting/Painting in the note of the Dwg.(though part of the information of ISO 8501-1 originates from the said DIN spec'n?);
a) If already mentioned in the Docs as DIN 55928, is this considered as deviation?
2) If not, any other equivalent DIN spec'n is prevailing?
Regards
Freelancing Engineer - Chennai, INDIA
November 6, 2015
Q. If I will do shot blasting with 1.2 mm dia. steel balls for 30 min in blasting machine, which SA standard I can achieve SA2 or SA 2.5?
Ankur srivastav- Jamshedpur, India
June 28, 2016
A. Hi Ankur. My guess is SA 2.5, but it's only a guess. Do you have any experience with different diameter balls or longer/shorter blasting times that would give us some basis for refining such guesses?
Regards,
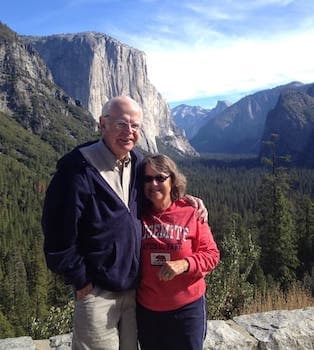
Ted Mooney, P.E. RET
Striving to live Aloha
(Ted can offer longterm or instant help)
finishing.com - Pine Beach, New Jersey
June 2016
A. If you are blasting a surface like this you get Sa 5 at least :D
Each part of the surface is only blasted for a few seconds to attain Sa3 (which decreases to Sa 2 1/2 (not Sa 2.5) within a few hours depending on climate). On usual S235 the attained roughness is medium(S), on S355 maybe less but can be optimized. In a blast machine you have surfaces depending on the parts shapes, which are not orientated optimally (low blast angle) so you have to slow down to get your Sa 2 1/2 there which means, better oriented surfaces have Sa3 by far...
corrosion protection - Dresden, Germany
August 31, 2016
Q. Dear Sirs,
I read all of the Q&A.
I understood that Sa grades are just for cleanliness.
Now, I have a question.
Is there an exact difference between Sa2 and Sa2 1/2 except optical points (like percentage difference)?
Best regards,
- Ulsan, Korea
June 29, 2016
July 15, 2016
A. Dear All;
I was reading TOTAL Company Standards for Offshore and Onshore oil Projects. Following seems to be useful in the discussion:
Apart of "Cleanliness Requirement", there is "Roughness Requirement" as below:
All surfaces shall be blast cleaned to obtain a total angular roughness Rt included :
- between 30 and 50 microns when total thickness of the coats of paint applied is less than 400 microns,
- between 50 and 80 microns when total thickness of the coats of the paint applied is greater than 400 microns.
Only dry blasting techniques are allowed. Compressed air for abrasive blasting shall not contain any trace of oil or water.
Desalination Industry - Tehran,Iran
August 31, 2016
This should give an idea of what the surface preparation grades acc. to ISO 8501 are. The complete standard ISO 8501-1 costs about 400£)
A. The surface preparation grades acc. to ISO 8501-1 / ISO 12944-4 are visual categories only. ISO 8501-1 is a collection of photographic comparison samples.
Roughness on blasted surfaces depends on the abrasive used and the material blasted. If Slag of 0 to 0.25 mm is used, a finer roughness is achieved than by using 2 mm chilled iron grit (density and size).
An angular abrasive leads to a sharp profile (grit) and a round one (steel "balls") to a profile rounded in the pits (shot). And some are less angular than others...
Needless to say, but it also depends on the strength, the ductility and the hardness of the material to be prepared. (high => low roughness, low => high roughness).
Roughness (surface profile) is judged according ISO 8503-1 to 5, yet the only real mobile method is the comparator procedure acc. to ISO 8503-2 with a sample consisting of four segments of Ry5(µm) 23-28/35-45/60-80/85-115 (shot(s)) and 23-28/50-70/85-115/130-170 (grit(g)) so there are 2 times 6 grades of surface profile (with (g or s) each): finer than fine (finer than Segment 1), fine (1-2), medium (2-3), coarse (3-4) and coarser than coarse (coarser than 4).
Usual coating materials have no special demand of roughness by themselves, but coarser leads to a larger surface and therefore to a better adhesion (That's why some Clients demand a roughness of 80 µm or more without really knowing what they demand, it is sometimes just expensive and sometimes not possible without really helping much, have a look below). Some examples for exceptions are most zinc rich primers ( Zinc(R) EP or ESI) - medium (G), some abrasion-resistant coats - up to coarse (G).
Medium(G/S)are somewhat of a trade standard.
On many materials higher grades cannot be attained, at least not by economic means:
-many stainless steels - on some not more than 20 or 30 µm,
-hardened steel surfaces (flame cut edges!)- almost none even with chilled iron grit of 1.5 mm
-cast iron - usually fine
I hope this information is of some help ;)
Greetz!
Ben
corrosion protection - Dresden, Germany
August 31, 2016
A. I just found a few question to answer, so here's a supplement...
In the technical data sheets (not the safety data sheets!) of professional coating materials there has to be a section where the demanded surface preparation grade is described, example:
http://www.international-pc.com/PDS/2561-P-eng-A4.pdf
Usually most materials need a Sa 2 1/2 to fulfill the intended protection (=> ISO 12944-5, tables annex A). Some (e.g. zinc rich alkali silicate) need Sa3, some surface tolerant primers only need a tool cleaned surface, example:
http://www.international-pc.com/PDS/2394-P-eng-A4.pdf
and so are suitable on sites where blasting is not possible. But blasting would improve the protection and therefore is the preferred method.
Silica sand causes silicosis and therefore should not be used for blasting. In most countries it is forbidden anyway... As a replacement slag tap granulate is used.
If you have a rust grade A or B (mill scale on full or parts of surface) you need "heavy" (high density) grains to hammer the hard and brittle scale off the surface. So a steel or chilled iron abrasive is the best choice. Higher pressure and less abrasive helps as well (higher speed of the single grains and as E = m/2 * v2 ... ;) )
On rust grade C or D (rust with/without scars) "lighter" abrasives like Slag (single-use) or garnet (reusable) should be used. The same goes for removing paint.
On non-ferrous surfaces (e.g. galvanized steel, stainless steel or aluminum) non-ferrous abrasives should be used because of small amounts of ferrite cause galvanic corrosion; (only white used) garnet or special "de-feritted" slag are the abrasives of choice.
There should always be finer grains in the abrasive (e.g. 0-2 mm when using 2 mm) as they make the "fine cleaning" in the pores.
Depending on climate (in particular air humidity) the preparation grade diminishes within a few hours. In 50% and above an Sa 2 2/1 lasts only maybe 4 hours or less. In 30% and below it can last 1 or two days...
For a few years roughness is considered for DFT measurement acc. to ISO 19840 (Correction values: fine: -10 µm, medium: -25 µm, and coarse: -40 µm) due to coverage of peaks. I think there have been several cases of damage in the past and this was the conclusion... I'd say, there was just bad surface preparation - because of this no coat would "fall off". Maybe for single coat systems with 80 µm or less this is one small issue but not for 160 µm or more. This correction value has to be added to the applied thickness and can cause real problems (e.g. zinc rich ESI, NDFT 80 µm+25 µm..., zinc ESI shouldn't be applied with more than 60 µm NDFT anyway. Anyhow only 30 to 40 µm have an electrochemical effect due to the inner resistance of the binder) so this correction value should be relocated to the intermediate coat.
A roughness demand of e.g. 30 to 40 µm in specifications should never be accepted as the values spread wide and after all it is handwork and if some looks really close it could be very very expensive... . You can not blast to an exact roughness like you can machine surfaces. So the grades acc. to ISO 8503-2 should be agreed upon.
We've coated parts for Stat Oil, Petronas, Siemens and a few others and the deviations listed above (if they were) have always been accepted when the matter was explained thoroughly... Even material changes (ESI to EP) where possible.
Btw. with the right combination of abrasive and material you can reduce a primary roughness but this would never be as exact as mechanical processing and why should you when a coat of a few hundred µm is applied anyway ;)
And there's a list with the different preparation grades I got from a manufacturer. They are not exactly the same but very similar.:
Standard
SSPC NACE ISO 8501-1
12944-4
SP 5 1 SA 3
SP 10 2 SA 2 1/2
SP 6 3 SA 2
SP 7 4 SA 1
SP 1 solvent cleaning
SP 11 ST 3 with Rz = 30 µm
SP 3 PMa
corrosion protection - Dresden, Germany
Q. Dear sir,
Please advise if the blast profile or amplitude is higher than required, what is the remedy to reduce the profile?
xervon - Doha, Qatar
January 1, 2017
A. Dear Mr Arthur Donat go for centrifugal blasting with ONLY steel shots to compensate higher amplitude profile.
Rahil ShaikhProtective Coatings - Dubai, United Arab Emirates
September 6, 2017
Q. Blasting metal surface using garnet 2040, finished with rust spots. Due to contaminated garnet or technical issues?
Joanne ChinFRP Products Co Pte Ltd - Singapore
March 19, 2017
Q. Dear sir,
How can I check the cleanliness of grit+shot blasted surface... is any visual comparator available to check for the mix of both, unlike individual comparators.
- Trichy, Chennai , India
April 4, 2017
Q. Let me know about blasting profile samples. How many samples we can take? Any standard describes it? As SSPC PA2 describes area and readings; is there same like that any standard for Profile sample?
BASHIR AHMAD- Dammam Saudi Arabia
August 14, 2017
Q. Hi.
I have this question that if SA 2.5 is a standard for visual appearance of cleanliness, then why only blasting is specified in ISO 8501-1 ? We can clean rust by Zinc phosphating also. One of my customers is asking for SA 2.5 and we have Zinc phosphating process in-house, but customer is insisting on Blasting only.
Please advise.
Desmi Equipment Pvt. Ltd. - Mumbai, Maharashtra, India
September 14, 2017
Q. Sir, required profile is 40 to 70 micron but after blast clean profile is 120 micron. For reducing the profile I did sand blasting again, blasting with small size of abrasive with 45 degree angle of nozzle
Now the profile is 90 micron .. please tell me how I can achieve the requires profile. I need the answer because in an interview they asked.
- Abqaiq, saudi arabia
May 3, 2018
Q. What is the blasting type for the interior of an existing petroleum storage tank that's been unused for some period. Note. It has been blasted and primed before use. Now a little pore of corrosion exists. Thanks
UKUTAIRE LoveaceLot aura international limited - ETHIOOE west, Delta state, Nigeria
May 30, 2018
Q. Does ALL mill scale have to be removed to meet SA2.5 or is there an allowable amount permitted?
Martin Howroyd- West Yorkshire / England
January 8, 2019
Q. Dear sir what would my answer be if interviewer asks me surface roughness of SA 2 1/2? Last time in my interview interviewer asked me same question; I told the same thing that it is degree of cleanliness not the surface measurement but he wasn't satisfied.
akash matthamwar- Nagpur, India
April 7, 2019
A. Hi Akash. You could add that it is possible to specify BOTH Sa 2.5 AND a surface profile. But if your interpretation of that interview is correct, I'd suggest trying to get an interview to replace him or her rather than interviewing for the jobs s/he evaluates people for :-)
Regards,
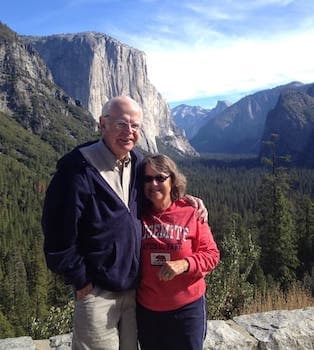
Ted Mooney, P.E. RET
Striving to live Aloha
(Ted can offer longterm or instant help)
finishing.com - Pine Beach, New Jersey
April 2019
ISO 8501-1 on Stainless Steel
Q. I am required to adhere to a coating spec that requires ISO 8501-1 be used to determine abrasive blast cleanliness on clean, new, uncoated abrasive blasted stainless steel.
The spec also calls for an SSPC SP10 on the clean abrasive blasted stainless steel.
My question is how can you apply the two standards to clean uncoated stainless steel?
- Ellenton Florida USA
August 28, 2019
A. Hi Jake. They are both cleanliness standards, and actually it's not uncommon to require compliance to two or more different specs as long as they are not contradictory. Your customer may be selling to two different customers -- for example, one of who wants compliance with SSPC (Society for Protective Coatings) standards and the other with ISO standards, and may not want to have to isolate one batch of parts from from the other.
Regards,
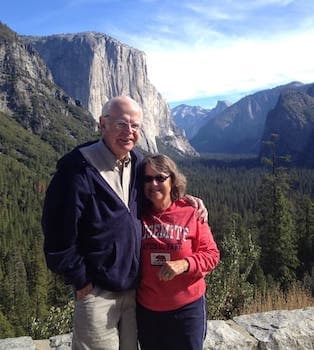
Ted Mooney, P.E. RET
Striving to live Aloha
(Ted can offer longterm or instant help)
finishing.com - Pine Beach, New Jersey
August 2019
Q. That is understandable but doesn't answer my question.
Those standards are visual inspections for carbon steel. How can they apply to new uncoated stainless steel?
- Ellenton Florida usa
August 28, 2019
A. Hi again. I don't think the spec actually says 'carbon steel' defining it in such a way as to preclude stainless; and I think I see an interpretive statement that says:
Essentially, these methods are intended for hot-rolled steel, but blast-cleaning methods, in particular, could also be used on cold-rolled steel of sufficient thickness to withstand any deformation caused by the impact of the abrasive or the effects of power tool cleaning.
Regards,
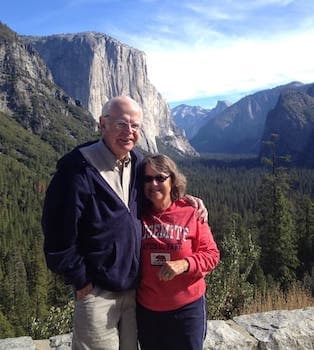
Ted Mooney, P.E. RET
Striving to live Aloha
(Ted can offer longterm or instant help)
finishing.com - Pine Beach, New Jersey
Q. I'm not very familiar with these standards. I know that I need profiles sandblasted SA2.5 and then covered with primer. The supplier confirms painting cycle SA 2-1/2 + primer.
SA2.5 is the same with 2-1/2? Thank you.
- Braila, Romania
August 7, 2019
A. Hi Mihaela. Yes, they are the same thing.
Regards,
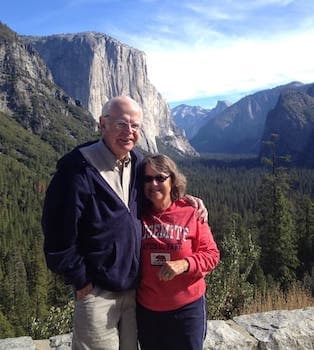
Ted Mooney, P.E. RET
Striving to live Aloha
(Ted can offer longterm or instant help)
finishing.com - Pine Beach, New Jersey
October 2019
Q, A, or Comment on THIS thread -or- Start a NEW Thread