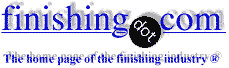
-----
Aluminum Welding issues with Iridite, Alodine, Chem-Film
Quickstart:
Aluminum is often 'chromate conversion coated' as a corrosion resistant final finish or as a pretreatment for painting or powder coating. The process actually involves many steps, usually including alkaline cleaning, etching, deox/desmut, the chromate conversion step per se, and water rinses between each step.
MIL-C-5541 / MIL-DTL-5541 / MIL PRF-5541 is the most commonly cited spec. "Alodine" and "Iridite" are proprietary trade names from two suppliers of the process chemistry. "Chem film" is a slang term for the process often used in the USA.
Q. Hello All,
I have a 5052-H32 Aluminum Chassis that is Fusion welded (TIG) together. After welding I have specified Chemical Conversion Coating (yellow) per MIL-DTL-5541 [⇦ this spec on DLA]. The areas in and around the welds becomes discolored after Chemical Conversion Coat, and actually some of the weld melted areas are a gray color. I talked to the vendor and he told me he is using Alodine for Chemical Conversion Coating. Does anyone know what is causing this? I have not seen in past.
Thanks,
Mike McLaughlin- Richardson, Texas
2001
A. The filler rod and the amount of heat used have a huge effect on the way the weld area takes the chromate.
Minor differences in the same alloy can affect the weld.
There might also be tiny differences in the platers pre-process and chromate parameters and still be well in the allowable range that could make some difference. The profit on chem film is very small. Virtually no plater can afford to do days of testing in pilot tanks to look for a slightly better look on the weld.
The filler rod is the prime suspect.
James Watts- Navarre, Florida
A. Mike,
It sounds to me that the parts were not deoxidized enough to clean up the welds properly in the cleaning process before chemical conversion. Also During the TIG welding there was enough heat put to the part that an exact color match is difficult to obtain. Their are proprietary chemicals out there that will help with this.
Lee Moss- Calgary, Alberta, Canada
Multiple threads merged: please forgive chronology errors and repetition 🙂
What does Iridite mean to welding
Q. We are TIG welding an aluminum frame, and would like an Iridite finish. What does this process entail? Will it effect our welds?
John M Gotsch IIImolding co. - Arlington, Vermont
2002
A. Hi John. Iridite is a Macdermid trade name for a brand of chemicals used for MIL-DTL-5541 [⇦ this spec on DLA] chromate conversion coating of aluminum. Protective finishes like chromate conversion coatings should ideally be applied after fabrication, not before. But you need to protect aluminum from corrosion in some fashion -- so if you don't do a chromate conversion coating, you have to do something else like anodizing or clearcoating.
Chromate conversion coating involves immersing the fabrication in a series of chemical processes, most likely: mild alkaline soak cleaner, caustic etch, desmut, and the conversion coat with intermediate rinses. Many jobshops offer this service. Good luck.
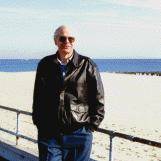
Ted Mooney, P.E.
Striving to live Aloha
(Ted can offer longterm or instant help)
finishing.com - Pine Beach, New Jersey
2002
Can't chromate spot weld marks on aluminium chassis
Q. I am experiencing difficulty in getting clean chromated surface ( yellow ) on Aluminium spot welded chassis. The spot welded points turns black color after plating. Is there any specific cleaning process / cleaning agents that could solve this issue. please help
Senthil Kumarproduct engineer - Singapore
November 30, 2008
A. Aluminum welding rod always comes out a different color from the popular alloys, some gray, some total black.
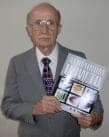
Robert H Probert
Robert H Probert Technical Services

Garner, North Carolina
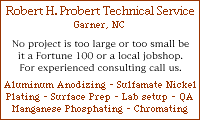
December 3, 2008
A. While welding rod material does typically contain high silicon and results in black welds, resistance or spot welding isn't done with rod material. Typically its done by holding 2 aluminum sheets in close contact under pressure and applying electrical current to copper electrodes that heat the aluminum in contact to the point where the 2 aluminums melt and fuse together. The black is typically too much electricity / heat resulting in alloying elements in the aluminum enriching in the heat affect zone OR from transfer of the copper electrode to into the aluminum due to too much pressure. You can try to abrade off the excess copper by wire brushing or sandpaper, for example, but etching it chemically will only aggravate the problem. Talk to the welder and work with them.

Milt Stevenson, Jr.
Plating shop technical manager - Syracuse, New York
December 7, 2008
Alodine bleeding through a weld
October 13, 2010Q. Hello,
We have been recently experiencing a problem with aluminum parts that have been welded. Mainly boxes that have been welded on the outside and the back of the bead is on the inside. Excuse my knowledge of welding language or lack of.
Anyway I chem film them and they look good, but as soon as we prime them with our chrome based primer and stick them in the dryer chem film bleeds through.
I sure this is contamination, but we have rinsed and rinsed and dried the parts very well. I have even changed the chemicals in my tanks and regenerated my ion exchange system.
I am thinking the chemicals are getting trapped amongst the cracks but the welders are telling me that they are not doing anything differently.
I have enclosed pictures.
Any advice would be appreciated.
Micheline Forth
metal finisher - Rincon, Georgia, USA
A. Your reasoning is dead on. Options are blow the joints out with high pressure air (requires safety procedures) or bake it at 130 °F for several minutes to dry it out or let it set in the bright sunshine for half a day.
James Watts- Navarre, Florida
October 15, 2010
A. Be aware that chromate under ANY paint must be very very thin, as in barely iridescent. It is a water containing gel, if you bake paint over it , it will dehydrate and the paint flakes off. Furthermore, most primers are not put over chromate conversion, - use one or the other, not both. There is a Lockheed spec that disputes this out of a New York facility where they call for putting acid wash primer OVER chromate conversion (not knowing that the acid wash primer deteriorates the chromate)..
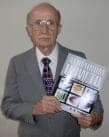
Robert H Probert
Robert H Probert Technical Services

Garner, North Carolina
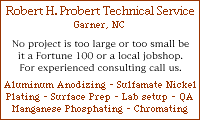
October 15, 2010
Q. Thank you for your responses - I am putting a very light coat on but it gets darker once the primer is applied. I am drying the parts in a dryer for 1/2 to one hour, then rinsing again in case some of the chemicals have made there way out of the welds. We do use an air pressure gun to dry, and I have to apply chem film prior to painting with a chrome based primer, part of the customers specs.
It looks to me like I am on the right track, maybe just longer on the drying process is required.
One more note, I am passing salt spray testing.
Any more thoughts would be appreciated.
Metal Finishing - Rincon, Georgia, USA
October 18, 2010
February 4, 2011
Q. Hello,
We are having a problem with chem film coming out of a weld when paint is applied and put into the heat room - temp at approximately 115 °F. This is only happening to aluminum boxes, which get welded from the outside.
We are rinsing and drying well. Taking several steps to ensure the welds are free from contamination but no matter what we do, the problem keeps occurring.
Does anyone have any ideas either in the welding department or in the chemical application that can help us.
I know it is contamination - there is no debate. We have tried rinsing, air drying with forced air - heat room drying prior to paint - re-rinsing and re-drying in case some contamination has come back onto the part.
Any help will be appreciated.
Sincerely,
Micheline
finishing department - Rincon, Georgia, USA
![]() |
A. What is your prep process. It is probable that the weld either will not take a chromate or the surface preparation needs to be different from what you are doing on regular non-welded work. Let us know the cleaning and deoxidation cycle, chromate pH, temp, post treatment. 115 °F is OK on chromate that is properly applied to most aluminum alloys ![]() Robert H Probert Robert H Probert Technical Services ![]() Garner, North Carolina ![]() February 7, 2011 A. Can you provide a few more details on the assembly process? Such as what is the aluminum alloy you are using to fabricate the boxes? What welding process and filler metal are you using? Are you doing any post-weld penetrant testing? Then, what is the primer and paint? Powder coat, epoxy, etc. Steve Sullivan- St. Charles, Missouri, USA February 7, 2011 A. Hi Micheline, Aerospace - Yeovil, Somerset, UK February 8, 2011 |
February 9, 2011
Q. Hello Everyone,
Thank-you so much for your responses.
I will try to answer all the questions.
The boxes are made from 6061 T-6 the filler is 4043. The welding process is Tig. Penetrant testing is not called out on these boxes. A leak test is preformed after welding. The primer is a water reducible epoxy containing strontium chromate.
The process line has an alkaline clean a deoxidizer a chem film that has a pH range from 1.6 to 2.0 and a temp of 75 - 85 degrees F followed by a cold water rinse.
I hear what you are saying Brian about the hot and cold rinses - that's why I would send them to the heat room and then rinse and dry again. Should I just keep doing more of this? The welds seem to have very small cracks on the inside. The welders tell me that is the way it is done, welded on the outside and sanded smooth on the outside.
My problem with the whole thing is the parts look great prior to paint. It is hard to imagine that much chemicals can get caught in the little crevices as in box #3.
One thing more to add. I am not failing my salt spray tests. Does that mean I can rule out my Ion exchange system?
Thanks again everyone,
I hope I did not leave any questions unanswered.
Micheline
Finishing Shop - Rincon, Georgia
![]() |
A. It is the surface tension of the liquid that does not want to let all of the trapped material out. The heated room is not a substitute for a warm (not hot) bath in the warm/cold sequence. It just dries it in place for the cold to redissolve. - Navarre, Florida February 10, 2011 A. Hi Micheline, Aerospace - Yeovil, Somerset, UK February 11, 2011 |
A. Just a suggestion, and haven't tried this on this particular application. But have you considered ultrasonic rinsing? Might be a bit cost prohibitive, but thought I'd throw it out there.
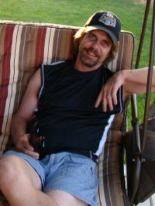
Marc Green
anodizer - Boise, Idaho
February 11, 2011
Degreasing chromated aluminum for welding
December 4, 2013Q. Hello All,
Recently I am having problems with welding. I weld Iridited Aluminium 4047 and Aluminium 6061 and am getting blow holes. I would like to reduce the number of them.
I am thinking of degreasing the Iridited Al4047 with a degreaser for a couple of minutes. Do you think it will work? Doesn't it damage Iridited surface? Please note that this part should pass salt spray test.
If it damages the coat, what else can I do?
I appreciate all of your replies.
Sincerely,
- Toronto, Ontario, Canada
December 10, 2013
A. Hi Tony. My understanding is that acetone ⇦ on eBay or Amazon [affil link] Warning! Flammable! , isopropyl alcohol, mild detergents, or very mild alkaline cleaning will not harm the conversion coating. However, in these days of highly proprietary RoHS-compliant trivalent chromating, it would be best to check with the supplier to make sure about possible exceptions. Good luck.
Regards,
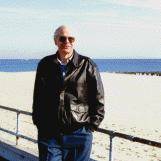
Ted Mooney, P.E.
Striving to live Aloha
(Ted can offer longterm or instant help)
finishing.com - Pine Beach, New Jersey
A. When customers ask us the question about welding aluminum here is what we tell them.
When welding aluminum prior to anodizing, use 5356 welding rod only. This rod gives the best appearance after anodize. Never use 4043! This will give you discolored welds after anodize.
Also all welding should be done prior to finishing of any kind. Welding will destroy any chromate conversion coating and the weldment will never pass salt fog testing unless the chromate is re-applied after welding. If that is the case then just wait until after welding to do all the finishing.
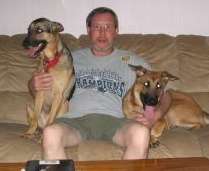
Tim Hamlett, CEF
- West Palm Beach, Florida, USA
December 27, 2013
Tig welding post chromate coating
Q. Hello
I am after some advice on chromate conversion coating.
I am about to start fabricating a job using aluminium and needs to be chromated as a primer for powdercoat. My issue is the finished job is to big too chromate post fabrication, so it has been recommended that all the material be chromated before welding and to etch prime the welds after welding. I am worried that the chromate will effect how the material welds and the strength of the weld. Would it be just a matter of wire brushing the weld area before welding? The material grade I will be using is 5005, T5 and T6
Luke
Sheet metal worker - Melbourne, Victoria, Australia
June 27, 2016
A. I have seen cases where the chromate conversion coating makes it difficult to establish an arc. Seeing as how you will be destroying the integrity of the coating in all the welded areas, it might deserve a second look. I would recommend a good cleaning after welding and then a powder primer under the finish coat.
Ed Peters- Frederick, Maryland USA
July 13, 2016
Weld showing after MIL-DTL-5541
October 10, 2017Q. We purchase A356 cast aluminum parts that get:
Weld areas allowable per spec (minimal areas of short pours or dings, etc.)
Heat treated to T61
Machined (use water soluble cutting fluid which has been the same for years)
Chemical film MIL-DTL-5541
We just ran into a major problem with our castings and have tried multiple solutions with no resolve.
After 25 years of doing the same process with our foundry the weld is showing up in every parts after the etching process when getting the parts chemical filmed. They appear as a dark gray or even black mark after etching.
We have seen this one time in the past and the culprit was the welder used the wrong weld rod material.
We have been working with the foundry to try and figure out what the problem could be as they have not changed any process on their end. Some of the test we have done are:
Trying multiple different manufacturer weld rods (A356 just like parent material)
Different cleaning techniques prior to weld
Multiple different outside welders (one sample weld from an outside source seemed to have the weld show up as "white" in color as apposed to "dark gray".
The ingot has been tested for chemical elements and it falls in with the spec for A356.
Any thoughts or suggestions would be greatly appreciated.
We are preparing to run a test with the actual parent material being used as the weld rod material and also try different plating companies.
- Ontario, California
A. If by "etching" you mean alkaline etching, that is part of the problem. you should not alkaline etch 356 castings because it decreases the area of aluminum metal that will take the chromate and increases the area of the silicon which does not chromate and turns gray. Stay out of the etch and use nitric /ammonium bifuoride to decrease the area of silicon.
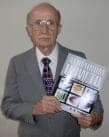
Robert H Probert
Robert H Probert Technical Services

Garner, North Carolina
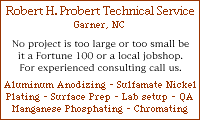
October 10, 2017
Thank you for the comment Robert. Yes our plating vendor does in fact alkaline etch. We have used the same process for over 25 years with no issues thus far.
We have since welded up more castings with different filler rods and cleanup processes to test.
We sent 2 parts to our current plating company which were alkaline etch cleaned and also sent 2 parts to another vendor who uses the nitric/ammonium cleaning you mentioned. Both processes have failed testing, meaning the weld is still showing up after chemical film, albeit the nitric acid cleaned parts did turn out slightly better, but not acceptable.
We are currently running more sample parts to test.
There seems to be so many variables which could create this issue and we need to figure out what one it is.
- Ontario, California
October 17, 2017
A. A356 should be welded using 4043 filler wire, if there are cracking issues with the welds, then 4047 is recommended, 4047 has a very high Si content, and will almost surely be quite a bit darker that surrounding material after caustic etching, it goes away if the desmut tanks can remove Si.
The "light" weld was probably due to using 5356 filler or something like it with almost no Si in it (off topic a bit, this is what I use if I need to anodize welded parts from 5xxx or 6xxx stock, if you use 4043 or 7 filler, you will get very dark looking welds after the part is anodized).
So I suggest you do some in-house testing with different filler wire to see which one matches the A356 best, then buy plenty of that very same filler wire from the very same supplier and use that for your work. If you send out those parts to be welded, send your tig wire with the parts and tell them to use only that and nothing else.
- Riga, Latvia
October 18, 2017
Thanks Janis -- a very informative answer!
Readers: Please also see thread 20304, "Weld before MIL-C-5541/chromate/Iridite/Alodine/chemfilm or after?"
Regards,
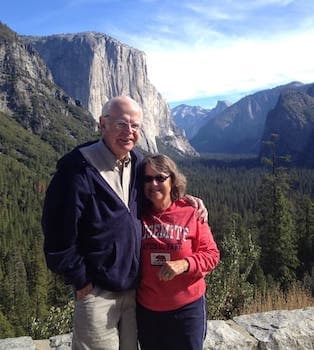
Ted Mooney, P.E. RET
Striving to live Aloha
(Ted can offer longterm or instant help)
finishing.com - Pine Beach, New Jersey
October 2017

Q, A, or Comment on THIS thread -or- Start a NEW Thread