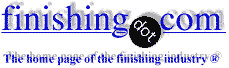
-----
Anodes keep eroding off the hangers
Hello,
I work for a company that makes buttons for the clothing industry. We have several drum type plating lines. Unfortunately our newest is giving us a bit of a problem. Because of space constraints caused by a low hanging hoist system we use titanium anode bars that hook on either side of the tank but are completely submerged through the width of the bath. This has not been a problem and in fact has worked quite well, until recently. We have had a bit of trouble plating in our tin bath. Repeated tests showed that the bath was ok. Finally I discovered that most of the anodes had fallen off the anode bar. When we drained the bath to recover them we discovered an interesting problem. The anodes are mounted on a hanger that is set about one and a half inches deep into the anode. The anode is (pardon my lack of knowledge) disappearing around the top 1.5" where the hanger is inserted. This continues until there is not enough material left around the hanger and the rest of the anode then falls off the bar and sinks to the bottom of the bath.
Now for the questions.
Why does the anode erode (?) at the point nearest the hanger first?
How do I prevent it?
Does anyone know of a mfgr. of anodes that uses a hanger that goes all the way through the anode.
And last but not least.
Should I quit scratching my head and just hang the anodes from the bar inside of a wire mesh cage like in a nickel strike operation?
Thanks everyone for your insight and help in educating this ignoramus.
Bryan Denton- Lawrenceburg, Kentucky, USA
Your problem is fascinating, but it sounds as if it is to do with a pure and simple galvanic couple. You do not say if the tin bath is acid or alkaline. Are you sure the hanger is titanium, or could it be another metal? I haven't any experience of titanium as a cathode, but I know it can be useless as an inert anode if it passivates and forms its non-conducting oxide layer!
I presume the electrolyte covers both the tin anode and the titanium hanger and that the hanger screws into the tin.
I suspect that, since titanium is not attacked by either hot alkali or strong acids, the electrolyte is attacking the tin and inducing a current onto the titanium that then creates a galvanic cell. If that is the case, it will happen when the bath is not in use, as the electrolyte completes an electrical circuit between the tin and hanger; the tin being anodic to the hanger then dissolves away until it falls off. When the bath is in use, both the titanium hanger and tin electrode are anodic and the tin will freely dissolve.
Try lifting the hanger out of the electrolyte or dropping the electrolyte level. Better still, if you can take the anodes out of the bath when it isn't in use, do so.
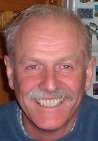
Trevor Crichton
R&D practical scientist
Chesham, Bucks, UK
The anode corrodes in proportion to the current density, and the current takes the shortest path from anode to cathode. Usually, with above-tank anode rods, the top of the working area of the anode ends up at about the same height as the top of the work, but the bottom of the work is lower than the bottom of the anode. The result of this is that the bottom of the anode is feeding "extra" surface area on the parts and it corrodes first. In your case, the top edge of the work is probably closer to the surface than the topmost working section of the anode. So the top of the anode feeds extra surface area and corrodes first. My feeling, sight unseen of course, is that shorter anode hooks would help, but switching to titanium baskets is probably the best solution.
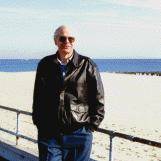
Ted Mooney, P.E.
Striving to live Aloha
(Ted can offer longterm or instant help)
finishing.com - Pine Beach, New Jersey
I have seen this first hand and switching to titanium baskets is not the solution you may be looking for as they will probably dissolve the same as the hooks. The first solution we found that worked the best is to simply pull the anodes out of the solution so that just the tin is in the electrolyte. Removing the anode when not in use works well also. We have followed all these other answers before to no avail at times as we have lost titanium before within our bath. If interested to speak further contact myself and we can discuss further conclusions we found at our shop which would be to long and difficult to properly explain here. Trevor has an interesting new viewpoint/answer to this problem as I have heard just about every other explanation of this.
Lee Moss- Alberta, Canada
There are two solutions to the anode corrosion problem. First, keep the top of the slab, star or oval anode out of the solution so the tin doesn't dissolve around the hook. Second, you can go to a zirconium basket and use tin anode balls. Titanium baskets will dissolve in acid sulphate tin baths.
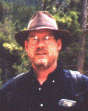
Bill Vins
microwave & cable assemblies - Mesa (what a place-a), Arizona
Bill Vins has a good answer - zirconium will last a long time in this type of application. For an answer to what you are seeing, however, you need to go to the electrochemical properties of titanium.
Titanium can be used as either an anode substrate (or basket) and also a cathode (its how they make copper foil). The inherent issue that you see, however, is its ability to withstand both chemical and mechanical corrosion in applications. As an anode, chemically, it is okay to use at a wide pH range and in the presence of several different anions, but with limitations in quantity. Fluorides attach titanium quite readily, as does some amounts of chlorides and the electrochemically generated by-product chlorine. Excessive concentrations of sulphates, usually in the form of sulfuric acid in excess of 20-25% or better will also result in high levels of corrosion.
Titanium usually forms a non-conductive oxide layer when applied in non-halogen electrolytes, which will keep the anode safe under a variety of normally incompatible conditions. This layer all but disappears, however, when the voltage (NOT current) exceeds 20-25VDC, which is the breakdown voltage of titanium (and its suboxides). This voltage limit can be shifted by other conditions - temperature, pH - too many things to list here. Since you are barrel plating, it should be safe to say that you are likely using a voltage greater than 20-25 VDC, so this may be a root cause of the condition.
One of the other items that speed or shift the reaction to the lower end is current density, which for lack of abetter term, is an accelerant to the process. This can work in several ways, but one of the interesting shifts it does is that it causes excessive gas evolution at the electrode interface (oxygen), which as it evolves, acts to concentrate the solution around the anode. In an acid sulphate tin bath, this can result in localized areas of sulfuric acid well in excess of the maximum concentration of acid resistance for titanium. This is usually why the anode hangers and such corrode closer to the top, and not at the bottoms.
From your space limits, it sounds as if you may have the anode baskets spaced very closely to the sides of the tanks, and this can result in poor agitation around the anodes, which in turn can aggravate the situation. You might look to see if you can improve your solution agitation and ever so slightly move the baskets further into the solution to allow free circulation. Removing this boundary layer is as important on the anode side of the equation as it is on the cathode to ensure good plating.
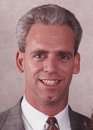
Tom Baker
wastewater treatment specialist - Warminster, Pennsylvania
As other responders have pointed out, the anode current will follow the path of least resistance, and the current distribution leaving the anode will depend upon the geometry of the cathode and how it is situated with respect to the anodes.
That being said, you are not the only person to experience this problem. At one of my former employers, we plated acid and alkaline tin and tin-lead alloys. We also recast our own anodes, and intentionally tapered the diameter of the anodes so they were larger at the top than they were at the bottom (it also made them easier to get out of the mold!) If not for the taper, they would have all dissolved away near the top and fallen to the bottom of the tank, even though the hook was not exposed to the solution. We used Monel hooks, but I don't think that changing hook materials will solve your problem.
Lyle Kirmanconsultant - Cleveland Heights, Ohio
Q, A, or Comment on THIS thread -or- Start a NEW Thread