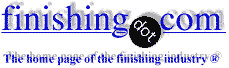
-----
Ion vs. Gas nitriding of H13 Tool Steel
Q. I currently work for a warm forging company. Currently, all of our H13 dies used for warm (1600-2000 degrees) of carbon steel are ion nitrided. We experience good tool life, but when our furnace is down, we have tried gas nitriding and find the dies wear even faster than if we had not used a surface treatment at all. What differences between the two processes would cause this extreme difference in tool life? Should we avoid using gas nitriding on H13 tool steel?
Laura Brink- Canton, Ohio
2001
A. Hello Laura!
What kind of white layer are you getting with the ion nitriding, and how does it differ from that given by the gas nitriding? That's the first question I'd focus on, as I suspect the compound zone created by the ion process is giving you the wear resistance you want.
Good luck!

Lee Gearhart
metallurgist - E. Aurora, New York
2001
A. Hi Laura,
There are a few reasons for the poor life of gas nitrided H13 dies.
1. Gas nitriding is much slower than ion (or plasma) nitriding and hence requires longer time of treatment for getting the same nitrided case depth. If the die had been gas nitrided for the same duration as in ion nitriding, the case depth would be lower and hence the wear resistance would also be lower.
2. In gas nitriding, ammonia ⇦ on eBay or Amazon [affil link] gets dissociated catalytically on the surface of the workpiece to release nascent nitrogen which gets into the surface. There exists a possibility that dissociation may not be effective at some isolated pockets within the retort due to poor circulation and in these regions nitriding would not effective.
3. Another possibility is that the white layer may not have been suppressed during nitriding or may not have been removed, if it had formed, after nitriding. In such a case, the layer would crumble and cause wear.
4. Yet another reason for the superior performance of ion nitrided case is that the case is a monophase layer of either epsilon nitride or gamma prime depending on the application. Such tailoring of the case microstructure is not possible in gas nitridin.
Dr N KrishnarajFree lance Consultant - Chennai, India
2001
![]() |
Q. We electro-spark deposited a superalloy on H-13 mandrels used for extrusion of superalloy tubes. Without the surface treatment we get from 8 to 30 extrusions per mandrel. With the superalloy coating we get from 30 to 100 extrusions per mandrel. The variation is due to the different alloys extruded, the size of the billet, the reduction ratio, the wall diameter etc. Does the ion nitriding give better result than say 100 extrusions per mandrel? Dr. Ram K. Iyengar- Huntington, West Virginia 2002 |
A. There is a very distinctive difference between the gas nitride and the ion nitride. The difference is in the resulting metallurgy from gas nitriding. With gas nitriding, the process is reliant on the decomposition of ammonia. The decomposition relies on the surface o0f the steel acting as a catalyst during the reactionary period of the process cycle. As a result of the decomposition ,and because of fixed gas the surface metallurgy is fixed. This means the surface will consist of the compound layer which is a mixture of two phases (Epsilon and Gamma Prime) underneath which is the diffusion zone, and under that, is the core material. The compound layer can be reduced by a two stage process involving a higher process temperature. The danger of this procedure is the potential for nitride networking and the risk of cracking, particularly on sharp corners. The ion nitride process on the other hand uses the same elemental gases of nitrogen and hydrogen, but no catalyst. The process relies on the almost infinite variability of nitrogen to hydrogen and vice versa to control the surface metallurgy (depending on the steel analysis). Therefore the surface metallurgy is variable. I am very familiar with the nitriding of both forging and extrusion dies with both gas or ion.
Best Regards to you,
David Pye- Meadville, Pennsylvania
2004
A. Hi Laura,
The temperature is 1000 °C? The problem is the generation of a diffusion zone with defects (due to interstitial nitrogen in the structure) which affects the high temperature performance (according with oxidation theory in metals). This problem you can find it in plasma and gas nitriding. My PhD work is related with high temperature sliding wear on H13 plasma nitrided and plasma nitrided + PAPVD coating.
Marlon Cruz- Caracas, Venezuela
2004
Q. Hi,
My question is that we use nitriding with nitrogen and ammonia for H13 steel dies, so what are the possible reasons for over-nitriding, and what are the possible reasons for not building nitriding on the dies.
industrial engineer - Westbank, Nablus City, Israel
May 24, 2008
Q. Dear Plasma Nitriding experts,
Does anyone know the role of Hydrogen in plasma nitriding? I am trying to do a duplex treatment (PN+TiN), but can't get any wear improvement compared to a pure PVD TiN.
Best,
material science student - Destin, Florida
October 28, 2008
2005
Q. The ammonia breaks to give molecular nitrogen, but does molecular nitrogen take part in the diffusion reaction.
Annada Prasad Sahooplating shop employee - Orissa, India
November 14, 2008
Q. We are using electropulse plasma nitriding. In this we have to use hydrogen and methane along with nitrogen. Can anybody suggest why we have to use both the gases and especially methane? We could not get good hardness and wear resistance after nitriding.
myil rajengineer - erode, Tamil Nadu, India
March 15, 2009
Q. Hi,
I would like to know the best time/temperature chart for gas nitriding H13 aluminum extrusion dies. I work at an aluminum extruders.
anodizing - cairo, egypt
May 15, 2009
Q. Hi,
I would like to know the best time/temperature chart for gas nitriding H13 aluminum extrusion dies. I work at aluminum extrusion plant.
- Karachi Sindh Pakistan
August 9, 2010
Q. I do Ferritic nitro carburising (Gas Medium NH3+lpg) process in fluidized bed furnace. I found scale after the process. The scale seems to be around 10 to 15 microns on the surface of the components.
Please suggest the cleaning of scale on the components; I tried using HCl and phosphoric acid but the finishing does not seems good.
- Coimbatore, Tamilnadu, India
January 28, 2012
Gas nitriding problems: no nitrided layer on aluminum extrusion dies
Q. I am using gas nitriding for extrusion dies. I am having a problem of not depositing the layer. Operation-wise I start the furnace with 350 °C temp. for half an hour and pass the ammonia 400 litres/hour. After reaching 350 °C I raise the temp. to 530 °C and pass the ammonia 800 liters/hour. Total cycle time is 12 hours but no nitrided layer is observed.
When I put the die for extrusion die becomes rough after 300 kgs of extrusion. Since most of the times I am using 0.8 mm wall thickness dies I am not able to check the layer thickness on bearing and I check hardness on the die surface. Please let me know the correct action to be taken.
With best regards,
Rao
aluminium extrusions - Jaipur Rajasthan India
January 7, 2015
Q. You put all the procedures about ammonia, but what about nitrogen? Because if you use gas nitriding you have to keep using both nitrogen and ammonia.
Abenezer assefaaluminium extrusions - adis ababa, ethiopia
October 1, 2015
Q. I am using gas nitriding process. Now we are facing problem that the dies are getting 10 hrc degrees each cycle; I think it is high. Please advise what are the reasons behind this, and whether that is good or not.
mohammed saleh- damascus, syria
May 2, 2016
Q. I am using gas nitriding process. Now we are facing problem that the dies are getting 10 hrc degrees each cycle; I think it is high. Please advise what are the reasons behind this, and whether that is good or not.
mohammed saleh [returning]- syria
October 19, 2017
2nd Request
Gas Nitride Issues: Blistering and Flaking on Nitrided H-13
Q. We manufacture parts out of H-13 forgings. A typical dimension is 18"L x 11.5"W x 4.5"H. Parts are machined and heat treated to Rc 44/47. They are then rough ground in several areas, allowing .002 per surface for final grind after gas nitride. They are then nitrided to a case depth of .012". On several recent occasions, the parts are received back from nitride with considerable blistering on surfaces that had not been rough ground prior to nitride. However, not all parts in a nitride run will exhibit blistering, and of the blistered parts, the blistering may be scattered, with perhaps one or two sides blistered, but the others clean. Our last nitride run was the worst we've experienced, with not only blistering, but with flaking as well. Our long time heat treat source is at a loss to explain the issue, as runs for other customers, done before and after our parts, have no problems.
Jerry Van- Howell, Michigan USA
October 15, 2018
Q. For white layer 3 to 30 micron meter and total case depth 300 micron for HDS H13 material, which process is correct plasma or gas nitriding ?
Material hardness is 46 HRC (Before nitriding).
- Pune, Maharashtra, India
September 3, 2019
Q, A, or Comment on THIS thread -or- Start a NEW Thread