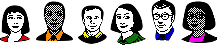
Metal finishing Q&As since 1989
-----
Bubbling, blistering, blackening of tin plating on brass

this text gets replaced with bannerText
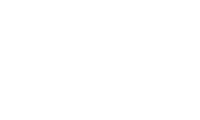
Q. We manufacture some small tin plated brass terminals for a particular customer. They are experiencing for the first time, bubbling of the plating during their plating operation. Does anyone know the possible cause of this?
Scott Niggemann1997
A. It could be lead in the brass which is causing adhesion problems if the pretreatment step is incorrect. Could it be that the material has changed?
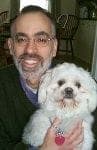

Tom Pullizzi
Falls Township, Pennsylvania
A. There are a number of factors which could lead to the bubbling of tin-plating. First of all, full surface cleaning is essential. Any oily spots or other dirt will definitely cause the bubbling problem. Organic or metallic contaminants in the plating both are another case resulting in the bubbling. Overplating also causes the bubbling. Poor connection leads to bad current distribution which results in partial bubbling. If acid bath is used, the low pH will bring about the bubbling.
Ling Hao- Grand Rapids, Michigan
Q. Correction: They are experiencing bubbling during their soldering operation. Sorry about the mistake.
Scott Niggemann [returning]A. It could still be the same problem, only the adhesion problem doesn't manifest itself until a severe test such as soldering. The precleaning cycle may be correct, but temperatures, concentrations, impurities, might be out of control.


Tom Pullizzi
Falls Township, Pennsylvania
A. You cannot plate tin directly on brass, it will cause adhesion problems. You need a nickel or copper layer between the brass and tin. The problems if you skip the underlayer might not be observed immediately, but they can come out with time.
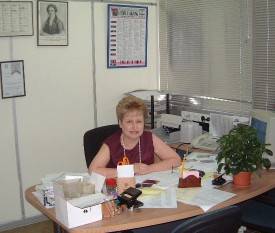

Sara Michaeli
Tel-Aviv-Yafo, Israel
A. Several causes possible:
- Bad pretreatment; should be visible after the acid dipping in principle with the atomizer-test or the water-break test.
- What Tom says about the lead; dipping in HF and using a cyanide copper strike should overcome this problem.
- Too much brightener or brightener decomposition products in your electrolyte. If they exceed a few tenths of a percent in the deposit, they will cause "outgassing" during soldering. However, this should be base-material independent. (Can be current density-related).
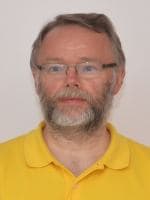
Harry van der Zanden
- Budapest, Hungary
Tin plating on brass turns black
Q. We make buttons made of brass.We do tin plating after plating the brass buttons with copper. But after plating of tin, plating gets tarnished that is it turns blackish. Please suggest solution.
Parvesh Dewan- Mumbai, India
2003
Dear Mr.Dewan,
A. Make sure that you have enough tin deposit on your buttons first, if not, try to increase the time of deposition. The main problem with tin plating over copper is the migration of tin onto the copper producing a kind of intermetallic compound (a bronze like) due to a low thickness of tin. If you still have problems after that, I would apply a very soft Watts Nickel strike - couple of microns only instead of copper, with as little as possible brightening agents, then tin plate the buttons. By doing this, the possibility of migration of Ni through Sn is practically zero.
Domingos J C Spinelli- S.B. Campo SP, Brazil
A. Mr. Dewan:
Normally you can plate directly in this way.
First electrolytic cleaner 30 seconds anodic
60 seconds cathodic
rinse
rinse
Acid dip ( nitric acid 50% volume) 30 seconds
rinse
rinse
Acid tin
rinse
rinse
potassium stanate 7 gr/lt
rinse
hot rinse
dry
We used this method without problems.
I hope this helpful.
Gabriel Ramirez Nuñez- Toluca, Mexico
Tin plating for Alloy 260 Brass
Q. I am a development engineer working on new product develop, and the material that we have chosen to use is a brass alloy 260 70% cu 30% zinc and .020" thick. We have specified a tin plating to ASTM B545 which requires a 100 microinch of copper underplate. We are being pushed to overlook the 100 microinch of copper underplate from our part mfg who will provide us stamped parts that are post plated. I do not want to deviate from the specification, but I would like some additional insight as to the purpose for the copper underlayment. I have read that it prevents zinc migration to the tin plating, and I am concerned that we could experience solerding plroblems down the road if we do not have the copper underlayment. What are your thoughts?
Jeff VerkleerenEngineer - Uniontow, Pennsylvania, USA
2005
A. You are going have a high potential for soldering issues if you do not get at least 40 microinches of Cu plating under the tin plate. I have been in the plating industry for 17 years and always recommend the use of Cu underplate on 260 alloy. If you don't then you are right you will get metal migration into the tin surface and soldering issues will arise
Fred W.- Indianapolis, Indiana, USA
June 21, 2012
Tin plating on brass is blistering
Q. Hello all,
We have a problem. We have some brass cans of size 40 mm x 50 mm. this already plated with tin. The can's surface have started bubbling leading to oxidation on the surface. Surface has become rough. Is there any way of smoothing the surface, strip the plating, and re plate it again with tin? Any suggestions, answers are welcome.
jobs outsourced and used - India
April 23, 2009
A. Sight unseen, I think that the material is a leaded brass and require a fluoboric acid dip to remove the surface lead.
James Watts- Navarre, Florida
A. Before re-plating you have to ask yourself why did this happen.
You should not plate tin directly on brass because you will have migration which causes bad adhesion.
You need a barrier of a nickel or copper layer between the brass and the tin.
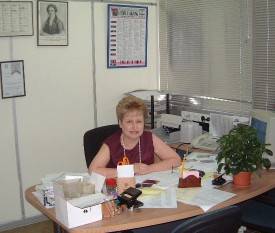

Sara Michaeli
Tel-Aviv-Yafo, Israel
Yes Sara,
You are 100% correct.
Tin plating on Brass we need to do nickel or copper under coating for better adhesion.
at least we need to do minimum 2.5 microns on any one of the under coat.
and after tin plating also do the thermal shock test for better confident.
- Salem, Tamil Nadu
Q, A, or Comment on THIS thread -or- Start a NEW Thread