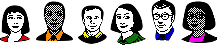
Metal finishing Q&As since 1989
-----
Interference coloring and two-step (electrolytic) coloring of anodized aluminum

Q. I'm looking for some people that have experience with "interference color anodising".
Who can help me?
Pierre Raes
1997
Belgium
A. Are you possibly referring to "two step anodizing" of aluminum?
What is the question?
James Watts
- Navarre, Florida
A. If you are talking about anodizing aluminum, then most probably you want to know about multicoloring -- a 2-step process of treating freshly anodized parts. We are presently installing an automated line, and one of the processes here is this multicoloring. The process is capable of producing (and reproducing) greys, greens, blues, violets.
Max Stein
captive metal finisher - Montreal, Québec, Canada
![]() |
|
A. Both processes exist, a one step and a two step electrocoloring on aluminum. Both process produce "interference colors". Contact Pinakin Patel at Clariant, he has large experience with this kind of procedures. ALCAN also has a patented process and they might also help.
Guillermo Luna
- Mexico City, Mexico
A. Interference coloring of anodized aluminum has been introduced to the market since 1984. It is a process which is different from the conventional 2-step electrolytic coloring process. The color effect is due to the interference of visible wavelengths rather than light scattering. Interference colouring is by either a 2-step or 3-step process. There are basically two methods for interference coloring :
1) "2-Step Interference Process": This is a new process.The conventional anodizing bath and Sn-electrocoloring bath are used. But, a different power supply and close control of anodizing parameters is required. The function of the power supply is to widen the pores of the anodic film (This is called modification of the film). Anodizing solution temperature is maintained between 17.2 and 17.8 °C., sulfuric acid concentration between 175 and 200 gpl. The power supply for anodizing is a DC-and-AC device with current density controller. Normal anodizing is done to get the required film thickness and then the interference (modification) step is performed in the same tank. Thus anodized load is then colored in a tin-based electrolytic process.
2)"3-Step Interference Process": This process requires a second anodizing process in a phosphoric acid solution to widen the pores of the normal anodic film obtained in the first sulfuric acid anodizing bath. The first anodizing bath is conventional sulfuric acid solution, temperature controlled at +/- 0.5 °C, concentration controlled at +/- 5 gpl. In the second anodizing tank, a special power supply and phosphoric acid based solution is used to modify the pores of the anodic film. Thus anodized load is then coloured in tin-based coloring electrolyte to have bluish grey, blue and green colors.
Timur Ulucak
- Istanbul, Turkey
1997
A. S. Kawai & M. Yamamuro's article, entitled "Interference Coloring of Dual-Anodizied Films on Aluminum Containing Electrolytically Deposited Thin Metal Layers" and published in the May 1997 issue of Plating & Surface Finishing, may interest you.
Ling Hao
Can nickel sulphate be added to tin based electrolytic coloring solutions?
Q. Hello Sir,
I'm an Architectural aluminium Anodiser. I am in this field not a long time. During anodising process sometimes, in reduction of coloring salt in electrolyte coloring bath, I cannot match perfect color ... there is need of adding Tin sulphate. So my question is can I add Nickel sulphate instead of Tin sulphate in coloring bath?
My coloring bath is made of
1- Tin sulphate
2- sulfuric Acid and
3- Stabiliser
Please Sir Guide me. Thanks.
Gohil Manoj
anodize - Surat, Gujrat, India
March 26, 2012
A. Architectural anodising is a little out of my field, but I would be surprised if you could replace tin sulphate with nickel sulphate. Why do you want to substitute one with the other? Is there a tin sulphate supply issue?
Brian Terry
Aerospace - Yeovil, Somerset, UK
Q. Yes, supply is issue.
And also lowering plant running cost!
gohil manoj [returning]
anodize - surat gujrat India
A. Hello Mr. Manoj ... hope you are fine.
I read your question and comments.
I can help you: yes, you are right, you can add nickel sulphate into tin-based electro-coloring solution.
By adding nickel sulphate you can earn two major benefits:
1. low cost of nickel sulphate because when nickel sulphate is added, then you can do color process with 8-10 g/l of tin sulphate instead of 12-15 g/l
2. you can get more red and shine in coloring of aluminium profile.
I'll come to India after Eid; so if you say, then I'll feel happiness.
Best regards.
Azeem khan
anodizer - Karachi Pakistan
----
Ed. note: Apologies, but we can't put readers into personal contact. Thanks for your understanding.
Q. Hi,
We are trying to install and connect an AC power unit to a tank containing tin salt in order to make a 2-step electrolytic anodise (1st anodizing step is running already).
What are counter electrodes made of? Size?
Bath capacity 1000 L.
Cheers
Sanad Hassan
- New Zealand
September 27, 2012
A. Hi Hassan,
Counter electrodes are usually 316 stainless steel. The useful area should be a large as possible and a least the area of the work load. By "useful", I mean that the general good practice of keeping counter electrodes (and anodes) slightly shorter and less wide than the work load should be followed. Failure to follow this rule, while increasing the area, has an adverse effect current distribution.
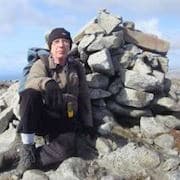
Harry Parkes
- Birmingham, UK
Q. Dear sir,
I would like to know about stabilizer used in anodising -- its purpose with tin sulphate and contents used in stabilizer
Mitesh Bhayani
- Mumbai, India
December 27, 2012
A. Hi, the stabilizer performs two roles.
1) To lessen the rate of oxidation of tin II to tin VI. in the bath.
2) To act as an oxygen scavenger at the work piece. This increases significantly the rate and depth of coloring.
Harry Parkes
- Birmingham, UK
Q. Dear Sir,
Can you tell me about the analysis for the stabilizer in coloring over the anodized part and what is the function of the above said?
manu sharma
- solan h.p. India
March 15, 2014
A. Hi, Mitesh; hi, Manu. Per Wernick, Pinner and Sheasby the contents can be materials aromatic carboxylic acids, cresol sulphonic acid, thiomalic acid, pyrogallol, resourcinol, and ferrous salts. In view of the many possibilities and the fact that they tend to be proprietary, your options seem to be to either buy them or do a lot of detailed readings of the literature followed by extensive experimentation. Best of luck.
Regards,
Ted Mooney, P.E.
Striving to live Aloha
finishing.com - Pine Beach, New Jersey
Fluoride accidentally added to electrocoloring bath
Q. Hi,
Salam to all of you :)
Dear friends, I want some help from you, I am an anodizer.
By mistake, a worker put 2 kg hydrogen fluoride in tin-based electrocoloring bath solution.
I don't find any problem until now, fluoride was put in 60 hours ago.
Now I want to know that what will be the effect (if any)?
I have 14000 liters of solution in the bath.
Thanks :)
Azeem Khan
- Pakistan
December 11, 2013
Q. G'day,
I'm looking for some advice on how to use the Munk IF30 interference colouring controller.
So it goes that I have a Munk controlled anode tank with:
180 g/l sulfuric acid
8 g/l aluminium
Temp range of 16 to 23 °C
With a Munk IF30 controller for interference
Then I have a Munk controlled electro colouring bath with the following:
Stannous sulphate 22.2 g/l
sulfuric acid 42.4 g/l
Stabiliser 35 g/l
I am running a 30m2 load and need a dark grey colour
Richard Williams
- Sydney Australia
June 26, 2014
![]() |
Q. Dear Sir, A. Hi Rajeev. This site focuses only on metal finishing, not the bulk manufacturing of commodity chemicals. But if you are unable to purchase tin(II) sulphate and only need small amounts for an experiment, it sounds like it's as easy as adding tin powder to copper sulphate [on eBay or Amazon]. I understand that it is also possible to add sulfuric acid to tin metal to make it, but that probably introduces some issues of stannic ions. Sorry, my background is only metal finishing and I'm personally unfamiliar with your electrolytic method for manufacturing it. Have you done a patent search? Simply pasting your capitalized phrase into Google or Bing seems to reveal a great deal of detail on the process. Luck and Regards, ![]() Ted Mooney, P.E. Striving to live Aloha finishing.com - Pine Beach, New Jersey |
Q. Hi,
I am currently producing the interference colouring using nickel sulphamate solution. I am doing 2 stage anodising, sulfuric acid anodising and then phosphoric anodising for pore modification.
Does anyone knows how to do the pore modification in the sulfuric acid tank (so all in the same tank), rather than doing the phosphoric acid pore modification?
Mani Govindan
Anodising - Uxbridge, Middlesex, UK
November 11, 2015
Q. Dear All,
What is the difference between 2 and 3 step interference coloring as to aim, cost, advantages/disadvantages, applicability as practical, etc? Could you share with us?
alaattin tuna
engineer - turkey, sakarya
June 22, 2016
A. Hello Alaattin. We appended your question to a thread where Timur Ulucak explained the basic difference. Hopefully other readers will flesh out the answer in the way that you request.
Regards,
Ted Mooney, P.E. RET
Striving to live Aloha
finishing.com - Pine Beach, New Jersey
Formula for bronze colour salt, their stabilizer and sealing for anodising of aluminium
Q. What is the detail procedure for making bronze colour salt, their stabilizer and cold sealing used for anodising of aluminium.
navnit kakade
- Pune, Maharashtra, India
June 16, 2017
A. Hi Navnit,
In addition to carefully reviewing this thread, which contains a lot of information for you, please try a literature search at surfacequery.com, and also see if Werner, Pinnick, & Sheasby helps you.
Regards,
Ted Mooney, P.E. RET
Striving to live Aloha
finishing.com - Pine Beach, New Jersey
Electrocoloring: Stannous sulphate in liquid vs. powder form
Q. We at present are using Stannous sulphate in salt (i.e., Powder) form in our electro colour bath. The problem we face is a lot of powder deposition is found especially in hollow sections and inside surfaces. How can it be reduced? Should we start using Stannous Sulphate in liquid form (i.e., stannous sulphate manufactured directly thru electrolysis process)?
Bhavishya Pandya
- Vadodara, India
August 18, 2017
2nd Request
Q. How can I make bronze colour salt, it's stabilizer, and cold sealing for aluminium?
navnit kakade [returning]
- Pune, Maharashtra, India
August 20, 2017
Q. Hi my name is Prashant as I want to know about basic Chemicals for ESTABLIZER for electrical output.
Prashant Sukhwani
Aarav surfin chemicals - Ahmedavad,Gujarat, India
June 21, 2018
Q, A, or Comment on THIS thread -or- Start a NEW Thread