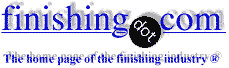
-----
Anodize voltage for 7075 aluminum
I work in the aerospace industry, and I have a problem with a couple of parts. They are 7075, and they were anodized to type 1 as opposed to type 1b (40 volts as opposed to 22 volts). Did the 40 volts damage the parts, or can they be stripped and anodized properly?
Ryan Andersonaerospace - Halifax, N.S., Canada
Although I have seen MIL-A-8625 / MIL-PRF-8625 [⇦ this spec on DLA], I don't think it explains the origin or reason for Type 1b coatings. I do understand from the AESF intensive training course that cast alloys tend to generate a higher current density than wrought alloys at the same voltage and may tend towards burning. So I am guessing that you are working with a cast alloy for which Type 1b has been specified to minimize the chance of burining. I don't immediately see any reason that the coating could not be stripped and reapplied, as long as the part has not been damaged; but if the coating is not burned, why strip the coating?
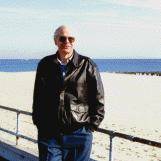
Ted Mooney, P.E.
Striving to live Aloha
(Ted can offer longterm or instant help)
finishing.com - Pine Beach, New Jersey
We are contractually obligated to anodize to MIL-A-8625. It states that any material with nominal alloying elements in excess of 7.5% shall not receive type 1 coatings (40 volts). We have to anodize the parts using 22 volts, it's just a question of wether or not the part was damaged by the original 40 volt supply. I read that cast alloys are damaged by 40 volts, and I've also read that 7075 material fails to develop a coating at 40 volts, so I've sent the parts to be stripped and re-anodized at 22 volts. I've still got time to scrap the piece if I find anything further to suggest that the material was affected.
Ryan Andersonaerospace - Halifax, N.S., Canada
Just a note to say check the sizes when they come back as the strip and re-process will have taken some of the base metal away.
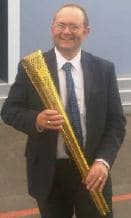
Martin Trigg-Hogarth
surface treatment shop - Stroud, Glos, England
Q, A, or Comment on THIS thread -or- Start a NEW Thread