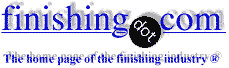
-----
Difference between SnPb 90/10 and SnPb 60/40
I'm working for the connector industry and someone was asking the difference between plated SnPb 90/10 and SnPb 60/40 soldertails.
Is there a difference in melting point, solderability, application or whatever? Can someone help me?
Thanks in advance.
- Hertogenbosch, The Netherlands
60/40 solder is what is known as eutectic composition. Although it is an alloy of two metals, it solidifies at one temperature as though it was one metal (strictly speaking, the eutectic is at 61.9 percent Sn, but 60 percent is the usual industry standard). Solidification temperature is 183 degrees C.
90/10 is well away from the eutectic. It begins to solidify at 300 °C, and the first metal to solidify has composition 97Sn 3Pb. Solidification then is progressive as the temperature is allowed to fall, with the last bit of metal to solidify being 65Sn 35Pb at 250 °C.
60/40 is the usual electrical solder. Can't help you with application for 90/10.
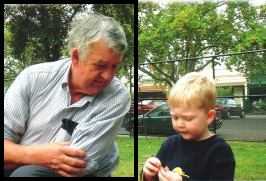
Bill Reynolds [deceased]
consultant metallurgist - Ballarat, Victoria, Australia
We sadly relate the news that Bill passed away on Jan. 29, 2010.
I don't know about the solderability, but the melting point of the 90/10 alloy will be higher than 60/40. The eutectic point for tin/lead is 63/37.
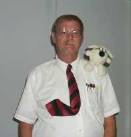
James Totter, CEF
- Tallahassee, Florida
Both are industry standards and the terminology simply means that there is 60% by weight tin & 40% by weight lead in 60/40. As said above, 60/40 will solder - melt, as in when soldering - at a lower temperature than 90/10. This may be important in assemblies where higher temperatures will damage some components and will also have energy saving implications. The 90/10 alloy is often called out to get that little bit of lead in the deposit. The lead is believed to halt or slow the formation of tin whiskers.
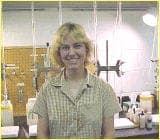
Megan Pellenz
- Syracuse, New York
90/10 is used in some electronics for its higher melting temperature than eutectic solder. Using 90/10 inside a component will allow the component to then be soldered into its next higher assembly (such as onto a PWB) without the worry of solder joints inside the component reflowing and creating a defect. Sometimes the reflowing of solder inside a component may be a worry, other times it is not.
Dave Laidig- Chandler, Arizona
Thanks Dave. Couldn't think of why anyone would deliberately make a soldering job more difficult by using 90/10 instead of 60/40, but your explanation makes one smack one's forehead and mutter about things that should have been obvious!
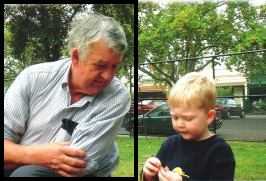
Bill Reynolds [deceased]
consultant metallurgist - Ballarat, Victoria, Australia
We sadly relate the news that Bill passed away on Jan. 29, 2010.
Thanks a lot guys for your response on my question. It helped me to understand the difference between 90/10 and 60/40 solder alloy.
Best regards,
- Hertogenbosch, The Netherlands
90/10 Sn/Pb solder balls are typically used in high-speed applications such as BGA packages, pc-board type stuff. I don't know if that aspect has come out already, but I hoped it might be helpful.
Have a great day.
Electronic Products Magazine - Garden City, New York
can I simply replace an 80/20 finish with a 90/10 finish. my concern is that the 80/20 finish is too soft and tend to be scraped during trim and form. since 90/10 is a bit harder, it might be able to address the scraping issue.
manny ramos- Philippines
The basic difference you face in 60/40 and 90/10 is the composition of Sn and Pb by weight. The lowest melting point in the eutectic is reached at a composition of 63/37. Addition of Sn increases the hardness of the alloy and so as the melting point.
I have read a paper stating the preference of 90/10 over 60/40 is the formation of dendrite during aging. When maintained at high humidity conditions or with some potential difference the dendrite formation (needle like growth) is more prevalent in 90/10 then 60/40. These dendrites can grown to extent of short circuiting and causing failure.
60-40 has the advantages of melting at lower temperature so in reflow soldering (SMT Components) the whole board along with the components is brought to the melting point of the solder. Some manufacturer prefer that the temperature not be raised above 200 ' c,in this case 60/40 is preferable while manufactures who doesn't mind about high temperatures prefer 90/10 who's melting point is
220-225 °C. If your requirements can match these criteria you can change from 60-40 to 90-10 or 80-20. Those who don't want to go to
90/10 range but prefer a low temp soldering stick with 80/20.
Good luck...
- Singapore
I see in the letter above where the 90/10 SN/PB melting range is higher than the 60/40 but can anyone give me the melting range of 80/20?
Regina J Huffelectronics - St. Petersburg, Florida, USA
2005
September 15, 2008
Hi,
I have come across slivers in bandolier terminals, which is an insertion process of plated terminals.
This has the potentiality of causing short circuit between the adjacent terminals.
Can this slivers be avoided in bandolier process. If yes, how?
machine shop employee - Cochin, Kerala, India
Hi, Pradeep. I understand what a bandolier plating process is, but I don't think you've given us quite enough to go on. I, for one, don't have a good picture of what you mean, so no idea of how to prevent it :-)
Regards,
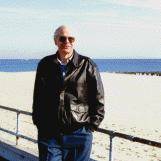
Ted Mooney, P.E.
Striving to live Aloha
(Ted can offer longterm or instant help)
finishing.com - Pine Beach, New Jersey
September 15, 2008
I want to find out which solder (tin/lead) composition like 60/40, 63/37, 75/25, 80/20, etc. is the brightest, shiny, lustrous.
G S ARORABUYER - DELHI, INDIA
March 16, 2009
March 27, 2010
We often used 97/3 solder to solder copper conductors to the commutator of small traction motors. Those electric motors used on fork lifts.
They are subjected to severe overloads quite frequently and standard 60/40 solder would liquify and be thrown out by centrifugal force.
Todays technology has replaced solder with TIG welding.
- Tallmadge, Ohio, USA
Q, A, or Comment on THIS thread -or- Start a NEW Thread