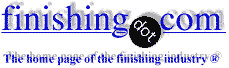
-----
Nickel underplating thickness
Dear Sir,
What is the optimum nickel plating thickness over phosphorous bronze?
I have read some articles about the nickel under-plating. However, one of them claim that the nickel thickness should be around 2.5 - 5.0 micro-meter.
On the other hand, one actually claim that it performs best at a thickness of approximately 50 micro-inches (which is equivalent to 1.27 micro-meter), regardless of the thickness of the gold. He also mentioned that additional thickness of nickel could be detrimental as it increases the roughness of the surface due to the decreased wear resistance.
We understand that the gold over nickel is a dominant plating technology in Asia. Hence, our Company is also using this type of coating for our motor parts (phosphorous bronze). However, the surface finish is quite rough and we are still trying to improve the surface smoothness.
Therefore, I am in dilemma, as I did not really know which thickness is more relevant to my situation. Currently, our company is using a nickel plating thickness of 2 ~ 4 micro-meter. I hope you can enlighten me regarding this question. Thanks.
With Best Regards,
Lau Shir Ling- Singapore
What is the optimum nickel plating thickness over phosphorous bronze? What is the application? Marine hardware, electrical contact, etc.
I have read some articles about the nickel under-plating. However, one of them claim that the nickel thickness should be around 2.5 - 5.0 micro-meter. That sounds like 0.0001 to 0.0002 inches, which is little more than a strike plate, it may be enough for a barrier to copper diffusion.
On the other hand, one actually claim that it performs best at a thickness of approximately 50 micro-inches (which is equivalent to 1.27 micro-meter), regardless of the thickness of the gold. He also mentioned that additional thickness of nickel could be detrimental as it increases the roughness of the surface due to the decreased wear resistance.
You can plate 0.002 inches of bright nickel and still have a smooth plate, but you need good filtration and a properly balanced bath. I don't know what you mean by decreased wear resistance. Plating deposits of columnar structure tend to get rougher as the thickness increases, so this may be what is happening in your case.
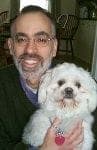

Tom Pullizzi
Falls Township, Pennsylvania
Q. We are doing plating of brass cases with nickel base coat by electroplating process followed by titanium nitride and flash gold by PVD Route. On usage pitting corrosion noticed on brass components within a short period. What is the minimum thickness of nickel is required to avoid this corrosion ? Or any other under coat is required to protect brass ?
Ramasubramanian Sankarabhatter- Bangalore, Karnataka, India
January 29, 2013
A. Hi Ramasubramanian.
Yes, gold is far more noble than brass, so galvanic corrosion is a given if the nickel layer is not pore-free. Tom Pullizzi has offered his opinion on nickel thicknesses above, but of course an exact answer on minimum thickness depends on the geometry of the parts and the quality of the plating.
I'm not sure what these "brass cases" with titanium nitride and gold plating are, but if they are watch cases or jewelry, you might want to consider white bronze as an underlayer in place of nickel. Good luck,
Regards,
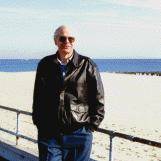
Ted Mooney, P.E.
Striving to live Aloha
(Ted can offer longterm or instant help)
finishing.com - Pine Beach, New Jersey
January 30, 2013
Q. Dear Mooney,
Thanks for your reply.
Why do you recommend white bronze as a base coat before nickel?
Is it OK if I do copper undercoat instead of white bronze?
Any other metallic coating is applicable to reduce corrosion?
Ramasubramanian
- Bangalore, Karnataka, India
February 14, 2013
A. Hi again. Sorry for the confusion. I wasn't suggesting white bronze in place of copper or as an undercoat for the nickel, but in place of nickel because of European standards regarding leachable nickel in jewelry.
Regards,
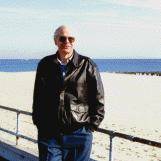
Ted Mooney, P.E.
Striving to live Aloha
(Ted can offer longterm or instant help)
finishing.com - Pine Beach, New Jersey
February 14, 2013
Q, A, or Comment on THIS thread -or- Start a NEW Thread