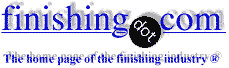
-----
Plate Wear with Web Offset Printing Plates
Q. We are a directory printing company that uses kodak CTP printing plates for use on Harris Heidelberg N9000D presses. We are currently only getting 200,000 per plate on the lower decks before we have to replace all the lower plates due to wear & splitting. Our colour sequence is KCMY. The concern is that we are getting what we call a tram track effect from the leading edge to the trailing edge these scratches cut into the non image area first the start into the image but mainly the non image area is effected by this. We are currently run G.N.P Paper 36 gsm. (Uncoated) We use Kodak chemistry. We use a CreoScitex 5080 Trendsetter with an Auto loader to make plates.
We would appreciate any assistance you can provide.
Thank You,
Andrew T [last name deleted for privacy by Editor]- Sydney, NSW, Australia
2003
A. Please tell me more about your press. What dampening system do you have. What blankets you are using, gauge, packing etc. And, what your fountain Solution you are using, please include the conductivity and pH. I would also like to know if you are using tap or RO water, and please let me know the dosage per gallon of you fountain solution is set up for. It would also be useful to know what are the running water temperatures are in the mixing tank and in the water trays.
Thanks,
Ken Anderson- Buena Park, California, USA
2003
A. Normally, the wear you discussed, sounds like it could be a couple of things. Definitely it is some sort of mechanical wear. First, I would check the grind of your ink to ensure it is as smooth as possible. Second, I would check the durometer of your form rollers to make sure they are <28. Next, as a test, I would flip the roll so that the wire side is printing on the upper instead of the lower units, to see it the problem follows the side of the web.
Randy Stewart- Los Angeles, California
2006
A. When I was on the Harris, I found it was the way we put the plates on, If the back edge of the plate was too slack we would get a split Plate all the time.
Edward PalmerWeb offset Printer - U.K.
2006
A. You don't say if you are running different products from top to bottom and the way I am getting this is the problem is only on the bottom. First - assuming all is equal its sound mechanical. Second - Check blanket gaps. Third - check plate centering - move to 0 - or plate cocking devices. Fourth - are the plates punched or bent on different equipment. Fifth - make should plate cylinders have no ink build in. Sixth - tap plates after mounting across an listen for hollow sound. Seventh - check plate bender for dirt or tape across bend.
Terry Allen- Elgin, Illinois
October 8, 2010
A. I would check your roller settings and blanket type as well. I wouldn't rule out plate manufacturer as well. Check out a test done on non-baked plates as well.
offsetpressman.blogspot.com/2011/04/plate-wear-how-it-affects-quality.html
- Toronto, Canada
April 7, 2011
? Did anybody ever figure this out?
Terry Ainsworth- Allen, Texas
December 18, 2020
A. Hi Terry. There were five excellent responses that firmly bounced the question back into the inquirer's court, such that more feedback is needed from anyone still having a problem rather than the responders suggesting even more ifs, ands, & buts. Yes, I wish Andrew had come back with an update after so many people tried to help him :-)
Luck & Regards,
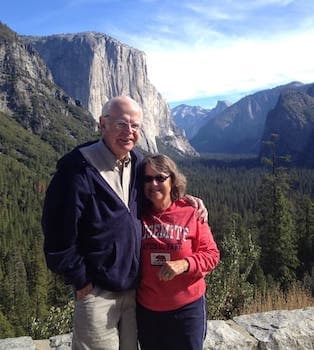
Ted Mooney, P.E. RET
Striving to live Aloha
(Ted can offer longterm or instant help)
finishing.com - Pine Beach, New Jersey
December 2020
Q, A, or Comment on THIS thread -or- Start a NEW Thread