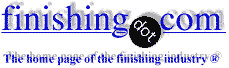
-----
Anodise vs Alodine vs zinc chromate
Q. I am constructing a homebuilt aeroplane in my garage. I want to treat the metal parts (particularly aluminium alloys) so as to minimise future corrosion problems, but without compromising structural integrity. Some alum. parts will be painted, so I want the treatment to be compatible with later paint coats; others will have an epoxy resin/glass fibre layup covering them, so I want to ensure a good bond there. What are the relative merits of anodising, Alodine and zinc chromate coating in each of these scenarios? I don't expect to do anodising, but I understand that Alodine and Zinc Chromate treatments can be done in a home workshop environment. Thanks for any informed comment about any of these processes.
I'm operating in Gloucestershire, England, so local knowledge would also be useful!
Rowland Carson- Cheltenham, Gloucestershire, England
A. Hello Rowland. Conventional sulfuric acid anodizing would not be applicable to airplane parts due to its effect on fatigue life and the potential corrosion from entrapped acid. Chromic acid anodizing is used on airframes, but is probably not applicable to a hobbyist. Boeing offers a proprietary boric-sulfuric anodizing process as an alternative to chromic acid anodizing, but it would probably be impractical for an individual to license it. Phosphoric acid anodizing is sometimes used as a substitute. Please see our FAQ "Introduction to Anodizing".
Alodine is a brand name for chromate conversion coating per mil spec MIL-C-5541. I question whether you would want to work with chromic-acid based chemicals in a workshop environment, but physically, yes, it can be done. Today there are proprietary trivalent chromate conversion products called TCPs that will meet the Mil spec., and that's what you probably would select.
In this context, zinc-chromate probably refers to a paint rather than zinc plating followed by chromate conversion coating. Where parts are not fitting against and rubbing against other parts, paint can be an alternative.
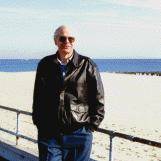
Ted Mooney, P.E.
Striving to live Aloha
(Ted can offer longterm or instant help)
finishing.com - Pine Beach, New Jersey
Q. So chromic conversion and Alodine are the same thing? What about application, I have applied a chromic conversion solution with a carbon tipped electrode at 0.5 - 1.5 amps what is the difference? application? Is there an advantage to one or the other?
Scott Chadwickrotor craft - lodi California
February 3, 2011
February 3, 2011
A. Hi, Scott
Alodine is a Henkel trade name for chromate conversion coating; they are the same thing in the sense that Pepsi and cola drinks are the same thing.
I don't know what you are talking about with the carbon tipped electrode, through. Chromate conversion coating does not usually require or use electricity, it's usually a simple immersion process. Hexavalent chrome is toxic and carcinogenic and not suitable for electrification experiments like that (if you are experimenting rather than carefully following directions). Good luck.
Regards,
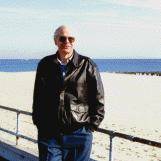
Ted Mooney, P.E.
Striving to live Aloha
(Ted can offer longterm or instant help)
finishing.com - Pine Beach, New Jersey
Q. Is there any problem or advantage to replacing old chromic acid anodizing requirements with chem film? Perhaps chromic acid has better salt spray test performance?
Rob Marinmetal finishing shop - Rancho Cordova, California, USA
March 5, 2011
A. Hi, Rob. Approvals are required for any substitutions in aerospace work, so you can't unilaterally make such a substitution anyway. Generally, 'chem film' (yet another name for chromate conversion coating) is conductive while anodizing is not; anodizing does indeed have better corrosion resistance than chem film.
Regards,
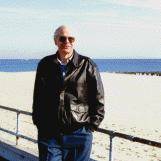
Ted Mooney, P.E.
Striving to live Aloha
(Ted can offer longterm or instant help)
finishing.com - Pine Beach, New Jersey
March 6, 2011
May 14, 2013
Q. Hello,
I am working as an airframe engineer at a DOA. I have some concerns regarding usage of Alodine and Anodising on aluminium alloys. We get often in discussions whether to use Alodine or Anodizing. The structures in question are small brackets and doublers mostly on secondary structures. So far we have referred to the SRMs which usually state Alodine. However, since we are producing a new design, perhaps we should use Anodizing instead of Alodine where conductivity is not required?
Some examples:
1. Antenna doubler (if conductivity is not required) should it be Anodized or is it sufficient with Alodine (SRM states Alodine for repair doubler).
2. Pressure bulkhead doubler for connector feed thru (if conductivity is not required) should it be Anodized or is it sufficient with Alodine (SRM states Alodine for repair doubler).
Materials are mostly 2000 series alloys (2024-T3)
When using 5000 and 6000 series alloys, is there any reason to use Alodine or Anodizing, or is it sufficient with just some primer or primer+topcoat.
Our primary cause of wanting to use Alodine is time saving and cost reduction.
I hope someone can advise me in this matter despite its complication.
Aircraft engineering - Nykoping, Sweden
A. Hi Igor,
If you are uncertain what to do you must ask the airframe manufacturer for advice. Trying to second guess the manufacturer's design intent and whether repair schemes are acceptable on new product is a dangerous sport that I would not recommend. If you get a response from the manufacturer you know that you are on safe ground.
Aerospace - Yeovil, Somerset, UK
May 16, 2013
Q. Thank you for your answer Brian.
Sure it would be the best if we could get all the answers from the manufacturer. However there is not always time to wait for an answer and sometimes it is very hard to get an answer, than one has to make his own decision.
So I would appreciate if you have some general advice when to use Alodine and when to use Anodization, e.g. ,"use anodization on critical parts outside of cabin".
Regards,
Aircraft engineering - Nykoping, Sweden
May 20, 2013
A. Hi Igor,
I know that some airframe manufacturers can be slow to respond, I have worked both for and with various manufacturers for a number of years now and some can be very frustrating.
The advice I give here is my opinion and cannot be used as a justification for actions taken if the airframe manufacturer then advises differently.
Alodine will not be as durable as anodizing in external environments, assuming the anodizing has been sealed. There are various grades of Alodine as well, so for an airframe make sure that you use a hexavalent chromate version.
Alodine will look markedly different from the anodize layer so if aesthetics are important you will need to paint to match the current color scheme. This will improve corrosion resistance as well as improve the appearance. Use a chromated epoxy primer followed by the appropriately colored top coat.
Aerospace - Yeovil, Somerset, UK
May 23, 2013
Q, A, or Comment on THIS thread -or- Start a NEW Thread