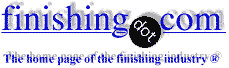
-----
Vacuum compatible coatings for max thermal radiation
(2001)
Q. Hi,
We've got Turbomolecular vacuum pump, where the impeller, i.e., the bit that spins at 50,000 RPM(!), has no way of losing heat other than radiation (due to magnetic bearings, etc., therefore no physical contact).
Therefore, were looking for two coatings: One Emissive, and one that Absorbs.
The Emissive coating is for the impeller, this must be able to withstand the loading of the high rotational speeds.
I guess we would ideally like the emissive coating to have a low absorption value, and vice versa, the absorbent coating to have a low emissive value. I assume this would maximize the heat transfer.
And the absorbent coating is for the stators and static parts of the pump that obviously don't see much stress.
They must be compatible with vacuum applications. I.e. very low out-gassing and very low water absorption (both enemies of vacuums!). And contaminating the system the pump is connected to is a BIG NO-NO!
The materials are:
Impeller: Aluminium 7075-T6 (temperature: 80 °C)
Static parts: Aluminium 6082-T6 (temperature: 30 °C)
TIA,
Rich Horner- Burgess Hill, England
A. You may want a surface that has high emissivity and low absorbtivity, but you're not going to find it. The laws of physics are against you -- a surface that has high emissivity also has high absorbtivity. You would probably be better off having high emissivity surfaces all around. Because the stator is cooled, it will absorb more heat than it emits, and vice-versa.
One method is to deposit a dark coating. Because of the stresses, I would think a PVD coating would be best. You can add to the effect by depositing a poor coating -- open columnar structure, known as a Zone 1 coating. The open structure creates a black body effect. While such a coating is worthless for wear or corrosion resistance, it is ideal for your application.
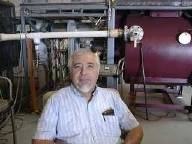
Jim Treglio - scwineryreview.com
PVD Consultant & Wine Lover
San Diego, California
A. Update. Jim's claim that absorbtivity and emissivity are equal is correct, but might be misleading to some readers for their purposes. While it is true that at any given temperature the absorbtivity and emissivity are equal, many designs take advantage of the fact that the temperature that 'matters' is often not just the temperature of the item in question, but the temperature of something else as well ...
For example, consider a chrome plated flat plate thermal solar collector. At visible wavelengths it may appear quite reflective, like it ought have little absorbtivity. But at infrared wavelengths it offers excellent (high) absorbtivity to absorb the sun's heat (as we learn if we touch a chrome bumper on a sunny day). Finally, because of its polish, it offers low emissivity at the temperature of the collector itself, to surrender as little heat as possible back to the atmosphere.
Regards,
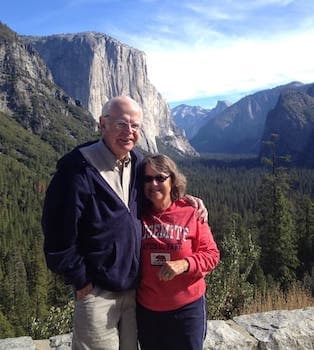
Ted Mooney, P.E. RET
Striving to live Aloha
(Ted can offer longterm or instant help)
finishing.com - Pine Beach, New Jersey
February 2020
A. Anodize. Opt for a dark dye if you like; in any case, you should be able to find a local technical anodizing job shop nearby. Aluminum oxide has good thermal characteristics and is virtually non-outgassing. Certainly anything you throw at it which is presently compatible with aluminum will be compatible with the oxide layer.
Dale Woika- Bellefonte, Pennsylvania, USA
Q. Hello Jim,
RE: emitters & absorbers...
I've done a little research on the values of Absorption/Emittance and some surfaces do offer different values for each. I think the Solar Heating industry make use of these properties a lot.
Please see here: fridge.arch.uwa.edu.au/materials/
RE: Anodising... I've experienced a lot of negative responses when suggesting using anodising in a vacuum pumps/chambers some anodising tends to absorb moisture... which is a killer for a vacuum system. Does this depend on the anodise method/process?
Cheers again,
Rich Horner- Burgess Hill, England
A. Aluminum oxide does not absorb water, per se, but it does adsorb water. Also, most metal oxides have relatively high surface energies, so wettability is a factor with many common liquids. However, the surface energy of aluminum is high, and most clean aluminum surfaces quickly form a native oxide layer from the interaction with atmospheric oxygen and water vapor. So, it stands to reason that a deep anodized layer might adsorb more water than a native oxide. As you mentioned, it is hard to get really deep vacuums with aluminum components.
How efficient is your TM pump design?
You may have to go to stainless steel to get ultrahigh vacuums. As far as high emissivity coatings, there are quite a few black surfaces that come to mind (SiC, MoS, et al.) but getting these to stick to T6 is going to be an issue and you are going to have to select for compatibility with your gas streams. In addition, the low temperatures involved with processing aluminum alloy components pretty much eliminates CVD coating methods & dictates PVD or PECVD; PECVD is tricky with aluminum and PVD is line of sight, which is problematic when there are sharp angles and recessed channels.
I am not trying to re-design your apparatus (we have several of them in house!) but there are many more available coating choices for steel than aluminum. A thought: have you considered ceramics?
Dale Woika- Bellefonte, Pennsylvania, USA
Q. We have a similar application that requires high emissivity coatings for rotor cooling purposes:
* Neutron chopper for neutron scattering experiments
* 7075-T6 Al rotor that spins at 600 Hz(36,000 rpm)
* 304 SST static parts
* In vacuum
* Rotor cooling by thermal radiation
We have concern with anodizing as it puts a hard surface on the rotor which, as result of design constraints, is a highly stressed component. We have been told by a reputable forensic engineering firm that such a coating is a source of cracks that are transferred to the base metal and result in premature failure. The example cited was aluminum alloy automobile wheels. Comments?
We are interested in as soft high emissivity coating for 7075-T6 Al. Comments?
We are also interested in a high emissivity coating for 304 SST. Comments?
Thank you,
Ralph Niemann- Argonne, Illinois, USA
High emissivity, vacuum-compatible coating for copper
March 15, 2014Q. I came across this interesting discussion while searching for high emissivity coating for copper. Jim Treglio's comment that emissivity and absorption are equal is true. But the rider is that they are equal at a given wavelength (or temperature). This makes solar collectors possible. Solar collectors are good absorbers at high temperatures, i.e., at lower wave lengths corresponding to incident solar radiation and high reflectors (same as low emitters) at lower temperatures, i.e., at longer wavelengths corresponding to the black body radiation of the absorber at, say, 100 °C.
Coming back to copper, I am looking for an emissivity of about 0.8 at 400 °C. The coating should be compatible with high vacuum. Any suggestions?
Bangalore Plasmatek - Bangalore Karnataka India
Q. In reference to H.R. Prabhakara question...
"Coming back to copper, I am looking for an emissivity of about 0.8 at 400 °C. The coating should be compatible with high vacuum. Any suggestions?"
I'm looking for the very same solution. Does anyone have any viable solutions? We'd prefer to use e-beam deposition. Are there any known high emission materials that can be deposited by e-beam?
optics - Santa Clara, California US
February 23, 2016
Q, A, or Comment on THIS thread -or- Start a NEW Thread