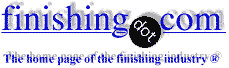
-----
Chromic acid anodize too light
Q. Chromic acid anodize too light. The process goes as follows:
1. Alkaline clean for 15 minutes.
2. Initial rinse 3 minutes.
3. Final rinse 3 minutes.
4. Oakite 160 [Chemetall] Etch for 2 minutes.
5. Initial rinse 3 minutes.
6. Final rinse 5 minutes.
7. Deoxidizer LNC for 5 minutes.
8. Initial rinse 3 minutes.
9. Final rinse 5 minutes.
10. Chromic acid anodize for 48 minutes.
11. spray rinse
12. Initial rinse 3 minutes.
13. Final rinse 3 minutes.
14. Warm water rinse 1 minutes.
15. Dilute Chrome seal for 26 minutes.
16. Warm water rinse for 1 minute.
- Seattle, Washington, U.S.A!
Treatment &
Finishing of
Aluminium and
Its Alloys"
by Wernick, Pinner
& Sheasby
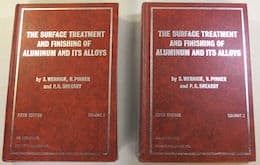
on eBay or Amazon
or AbeBooks
(affil link)
A. First, what is the question?
Then I have some for you:
1) Since chromic acid anodize is mainly used for aerospace industry, I don't know to whom spec you're working and whether they tolerate the alkaline etch.
2) What voltage you're anodizing at? Is it the 22 Volts, 40 Volts or the European 50 Volts?
3) What is the alloy you're using?
4) What do you mean by too light?
If you mean coating weight, then it would be interesting to have your average CW results. In any case, if you're having a trouble to build up a good anodic layer, then you might consider looking at your power (rectifier), especially the RIPPLES (Volts AC / Volts DC). The ripple should not exceed 2.0%.
Hope this would help.
Regards,
Hocine Djellabanodizing shop - Verdun, Quebec, CANADA
A. If by too light you mean it is not grey colored this can be due a lack of sulphate. sulphate kills the anodising solution: get to about 0.5 g/l and the solution gives up anodising. Smaller amounts give the grey color. If you make a anodise solution with analytical grade chromic acid you can get clear anodise from chromic. As most technical grades contain a small amount of sulphate you get a grey coat. If you buy the cheap flake chromic the sulphate is so high the bath does not anodise. So if the color is the problem check the sulphate.
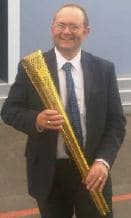
Martin Trigg-Hogarth
surface treatment shop - Stroud, Glos, England
Q. I am wondering if there is any information on to what degree ripple affects the Chromic Acid Anodize process. What is the min/max? Would 20% ripple at 40 volts be problematic?
Joel ClemonsQ.A. Manager, Plating Shop - Oxnard, California
March 11, 2011
A. Joel,
20% ripple will be a problem, the usual industry maximum you find in specifications is 5% and as you can see from an earlier post it can be recommended to be as low as 2%.
Remember that the higher the ripple the greater the effects of the AC current will be on your anodising process.
Aerospace - Yeovil, Somerset, UK
March 16, 2011
![]() |
A. Assuming that you are using a single phase power source, you would have to be using 100 amps or less on a 500 amp power supply to have a 20% ripple. If you know that you are going to use it a 40 V, you can have a local/regional shop that repairs or makes power supplies add a choke for your exact use. - Navarre, Florida March 16, 2011 A. Are you measuring the ripple at full anodizing voltage? Is it an SCR rectifier? If so, a 20% ripple reading at full voltage output would make me suspicious that something is wrong with the rectifier. ![]() Jon Barrows, MSF, EHSSC Kansas City March 16, 2011 |
Color of chromic acid Anodizing
Q. Hi,
I am actually finding out a way to be able to get a dark grey chromic anodized aluminum without dyeing.
The sample given to us has a color of Hard anodized aluminum. On our trials, we're consistently getting a light grey color. We tried changing the concentration of the anodizing bath as well as the type of jig used (titanium and aluminum), however, we are getting the same light grey color. Can you please help me find out the correct adjustment/s so that we can achieve our target color?
- Manila, Philippines
July 31, 2015
finishing.com is made possible by ...
for Chromic Acid Anodizing [Detroit, MI]
Q, A, or Comment on THIS thread -or- Start a NEW Thread