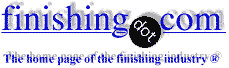
-----
Polishing 99 gsxr-750
Hello,
I have a 99 gsxr-750 and was wanting to know if you have any type of hints to polishing the frame and swingarms.
Thanks,
Matt Persinger- Red House, West Virginia
2001
A. Polishing your bike can be easy if you follow the correct steps to make it simple for yourself. I will detail the steps and equipment needed to polish your frame and swingarm. I will also give you a list of materials needed to complete the job. Good luck with your project.
MATERIALS NEEDED: You will need a buffer. I recommend a Sears/Craftsman 6in. Sander/Polisher model 91052. This is a very inexpensive buffer. The buffing process can be rather harsh on a buffer so I don't recommend using a $200 Porter Cable. The Sears buffer is only $50 and does the job very well.
Spiral Sewn Buffs, Loose Section Buff, Emery Compound ⇦ on eBay or Amazon [affil link] , brown tripoli buffing compound ⇦ on eBay or Amazon [affil link] , white buffing bar ⇦ on eBay or Amazon [affil link] , Buff Rake, Easy Off Heavy Duty oven cleaner ⇦ on eBay or Amazon [affil link] , Ear Plugs and Safety Glasses, Mothers Mag and Aluminum Wheel Polish.
The Process: We are now ready to get started on our polishing. The first thing we need to do is to remove any body panels that we do not want to get broken, screwed up, or polished. I removed everything from my bike including the rear subframe. I did, however, leave the swingarm on the bike when I polished it. You can remove it if you like. It will not make a difference.
The next thing that we need to do is to mask off everything that will not be removed from the bike. We do not want to get any overspray onto the remaining parts of the bike. I just used masking tape and newspaper. I suggest putting several layers of newspaper so that the oven cleaner does not soak through. Now that our work area is clear, we are now ready to start stripping the anodized finish off of the work area. I highly recommend wearing safety glasses from here on. Start by spraying the oven cleaner on the work area. Try to spray close to the area as to prevent over wetting your newspaper. Let the oven cleaner sit on there for about 20-30 minutes. Wipe off the oven cleaner with a wet sponge. Now reapply a coat of oven cleaner to the work area. Now the work area should start to turn black. Once it has turned black, you can wipe off the oven cleaner. Check to make sure that all of the work area is black. If there are spots, then you need to reapply the oven cleaner to those areas to get the anodizing all of the way off. The areas that still have an anodized finish will not polish.
Now that our work area is free of any anodized finish, we are ready to start polishing. Install a spiral sewn buff onto you buffer. I had to use two washers on the bottom of the buff to be able to crank the buff on really tight to the buffer. You will not want the buff to spin on the shaft of the buffer. I also recommend leaving the handle off of the buffer as this will just get in your way. We will start with the Emery compound first. This is a rather abrasive compound. We will apply this to the buff. I recommend putting in earplugs now as the buffing process is quite loud. Turn the buffer on and lock it in at the fast speed. Now take the Emery compound and apply it to the buff. By holding it against the surface of the buff, it will start to melt onto the buff. We can now start buffing. Hold the buff against the surface of the work area. Use a little pressure, but not too much as we want the buff and compound to do the work. You will start to see the black disappear from the work surface. You are actually starting to buff the work material now. You will begin to see results in no time at all. I suggest moving back and forth in a slow even motion so you do not heat the metal too much and cause imperfections in the final look. If you are leaving a residue of compound on the work area then you are using too much compound. Be sure to rake your buffs every few minutes to keep them clean. Once the buffs have filled with metal, they will buff very slowly and will be gray and hard. It is time to replace the buff at that time. Continue buffing all of the surfaces until they are smooth and appear polished. Even though the work area will appear polished, it will not be as appealing in the sunlight as it will if you finish the process.
The second step is very similar to the first step except for the compound. We will now need to switch to the Tripoli compound. This is a less abrasive compound as the first and this process should not take near as long. Follow the steps as before, once again letting the buff do the work. This will help to remove most of the scratches that the first step has left in the metal. Your work area should now really start to luster. We are very close to finishing the project.
The next step is to clean any of the compounds that may have built up from the buffing process. I recommend using Mothers to clean this residue off. We do not want any residue built up that can scratch the surface again. The last step is to remove all of the fine scratches from the work surface. This process is the easiest, but the compound is the hardest to use. We will use the loose sewn buff and the white buffing bar ⇦ on eBay or Amazon [affil link] . The hard part is the fact that we are using a loose sewn buff so it is hard to get the compound onto the buff. Once it is on though, you will just lightly apply this to the work surface. This will remove any final scratches left by the first couple of steps. You will be able to keep your work looking nice by cleaning it with the Mothers. This process does not have to be done all of the time. The finish will be quite resilient once the polishing is done.
Ryan- waldorf, Maryland
Q. What about sanding from a hard to a mild grit sandpaper, isn't that one of the steps?
Eric Kay- Wallingford, Connecticut
2004
Q, A, or Comment on THIS thread -or- Start a NEW Thread