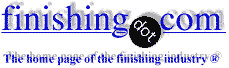
-----
Anodized Aluminum Coating Weight Testing ASTM B137
Q. We are adhering to anodising MIL-A-8625 / MIL-PRF-8625
[⇦ this spec on DLA]F for Type 1 and Type 2.
For ASTM B137, measurement of coating weight, it mentions the steps "Remove the specimen, wash in distilled or deionized water, dry, and weigh." May I know how to determine duration of drying? Is it until no change in weight?
Does the drying have to be carried out in an oven or any equipment possible? We have a drying tank but it is at 70 °C. ASTM B137 also mentions one of the steps in preparing test sample is drying at approximately 100 °C. This has to be adhered to?
Thank you for your help.
- Singapore
January 7, 2021
Multiple threads merged: please forgive chronology errors and repetition 🙂
Q. I am reading a specification and have some questions regarding the specified criteria for the clear anodized coating for a curtain wall on a project in Hong Kong.
1. Finish thickness specified for exterior aluminum surfaces is 40 microns (0.040 mm). First, can this thickness of clear anodizing be applied? Second, are there any negative results from applying this thickness (other than increased cost)? Third, Is there any benefit to having this thickness of anodizing over a normal 18 to 30 micron thickness?
2. How can I determine the density of the coating thickness? Specifications say "density of coating shall not be less than 2.72 gm/cc". This obviously varies with the coating thickness so how can it be calculated?
3. What is a Nitric Acid wash to seal the finish? I have never heard of this. It sounds like a pretreatment to me rather than a seal. Specifications say "Nitric acid wash to seal is mandatory." I thought all seals on anodized coatings were done with deionized boiling water. Thank you for whatever help anyone can offer.
Ronald K [last name deleted for privacy by Editor]- Hong Kong
2001
![]() |
A. Ronald, I can answer a couple of your questions rather easily. In reference to determining the coating density, the first step is to determine the average coating thickness of a test panel. The next step is to determine the coating weight of the panel by stripping the coating with a Chromic/Phosphoric acid mixture. The stripping process should be performed on a test panel that has not been sealed. Using the beginning and ending weights of the panel and the surface area, the coating weight can be determined. Use the thickness of the coating to determine the average density of the coating. I have not heard of a nitric acid seal. It seems to me that sealing with this type of solution would leave a corrosive residue in the pores of the coating. As far as the clear coat, could you please provide the specification you are conforming to so I can provide an adequate response. Best of Luck. Ira Donovan, M.S.F.Kansas City, Missouri A. 1) The thickness you are mentioning looks like a tad high for a normal sulfuric acid anodizing, as per MIL Spec MIL-A-8625 / MIL-PRF-8625 [⇦ this spec on DLA]F Type II. In fact 40 microns corresponds to about 1.57 mil, which is almost about the thickness for a hard coat instead of an architectural anodizing! You need first to establish whether is it a hard coating or a regular sulfuric acid anodizing! 2) Density of the coating The density of the coating thickness can be determined in the same way you determine the coating weight! You anodize at least 2 test panels (same alloy as your load), with a known geometric area (let's say 10 by 10 cm) Measure your coating thickness. This would give you the volume of your coating: Volume [cc] = 2 x Thickness (cm) x 10 (cm) x 10 (cm), accounting for both sides Weigh you panels with the coating on (Winitial) Strip, dry and reweigh stripped panels (Wfinal) Coating density = (Winitial ñ Wfinal) [gr] / Volume coating [cc]. 3) Seal Test and ' Nitric acid wash to seal' Here, it looks like they are talking about the Acid Dissolution Test (ADT), ASTM B680. Normally, the ADT is carried out without any pretreatment. However, new European standards require a pre-dip in a 65% (v/v) nitric acid for 10 minutes and then followed by the ADT! Hope this would help or someone else would comment. Hocine Djellabanodizing shop - Montreal, Quebec, CANADA |
Q. In answer to Ira Donovan's question, the clear anodizing should conform to AAMA 611-92 and AAMA 607.1 and meet test requirements of ASTM B136, ASTM B137, and ASTM B244.
Thanks for your help so far.
Ronald K [returning]- Hong Kong
2001
Multiple threads merged: please forgive chronology errors and repetition 🙂
ASTM B137 and ASTM B680 - Prevention of Poorly Sealed Anodize
Q. I have read many great inquiries on this site into MIL-A-8625 / MIL-PRF-8625
[⇦ this spec on DLA] Type II, Class II black dye fade issues. I had a rather disastrous similar occurrence. I am now in the process of preventing future occurrences.
How do I call out a good requirement for meeting a quality seal confirming to one or both of ASTM B137 & ASTM B680. I want to make sure vendors can realistically meet my requirements.
Engineer - Albany, New York
2006
Treatment &
Finishing of
Aluminium and
Its Alloys"
by Wernick, Pinner
& Sheasby
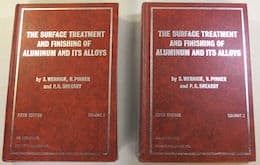
on eBay or Amazon
or AbeBooks
(affil link)
A. Black is a pain, requiring thick anodizing for saturation of color. Typically, shops do 0.0005" to 0.0007" anodizing thickness for black anodizing.
After you think you've got it, check it in different light too! Black dyes are often actually very very dark blue, but sometimes very very dark red, and the two will contrast almost comically in certain types of light as at least one manufacturer of audio systems for darkened public stages found out :-)
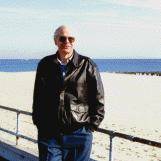
Ted Mooney, P.E.
Striving to live Aloha
(Ted can offer longterm or instant help)
finishing.com - Pine Beach, New Jersey
A. Anodizing shops are notoriously negligent in controlling their seal tanks. Many do not even use D.I.water. Few control pH. Nobody realizes that a seal is a very weak solution, and as such, is therefore more prone to contamination than the solutions back up stream, yet it is a very important step in the process to give maximum corrosion protection.
A seal should be made up with D.I.water. dragged into with D.I.water, evaporation replenished with D.I. water,and because of the low concentration, titrated and pH adjusted daily.
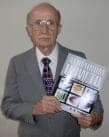
Robert H Probert
Robert H Probert Technical Services

Garner, North Carolina
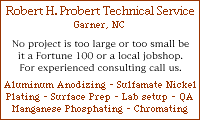
Re: "How do I call out a good requirement for meeting a quality seal?"
A. Simple: MIL-A-8625 / MIL-PRF-8625
[⇦ this spec on DLA].
All anodize per MIL-A-8625F (except Type III, Class 1) must be properly sealed. If not, it won't pass the corrosion or light fastness requirements. Good color is only difficult with die castings.
An anodizer with the solution control problems described by Robert isn't meeting MIL-A-8625F requirements. Cheapo dyes lack light fastness and have color issues as mentioned by Ted. Suggest that you print out MIL-A-8625F, highlight the testing requirements, and then QA survey the anodizer & potential new ones. Ask for the salt spray ( ASTM B117) & coating weight (ASTM B137 or MIL-A-8625 para. 4.5.2.1) monthly results and the process solution records for at least the last 12 months. Also ask for the Taber test results if they do hard anodizing. Examine their QA manual and other QA records such as Shop Travelers, Discrepancy Reports & logs, Corrective Actions, approvals from big-name customers, etc. Get the dye name and its light fastness per the dye manufacturer. Have they ever had a light fastness test done? Ask for a demonstration of their thickness tester (calibration & measurement).
ASTM B136, the anodize stain resistance test, is a quick and easy seal test for either you or your anodizer (requires handling a bit of nitric acid safely). Not for alloys > 2% Cu or 4.5% Si, though.
Light fastness testing per MIL-A-8625F, paragraph 4.5.4, is only performed when required by the customer. It takes time & money. Do at least once, after verifying that a suitable dye is being used and that other parameters are under control. ASTM G23 & G26 have been superseded by ASTM G153 & ASTM G155, respectively, but are still usable. ASTM G154 is for fluorescent light exposure. A longer test is given in UL 746C Ultraviolet (UV) Light Exposure, 720 hours of twin-enclosed carbon or 1,000 hours of xenon-arc weatherometer conditioning [omit the additional testing in this spec.]. I've heard that SAE J1960 and SAE J2527, Accelerated Exposure of Automotive Exterior Materials using Xenon Arc radiation, are standard for vehicles.
- Goleta, California

Rest in peace, Ken. Thank you for your hard work which the finishing world, and we at finishing.com, continue to benefit from.
Q. What is the normal thickness of the sealing layer on an anodized aluminum? Is there a way (ASTM method?) to measure the thickness of the seal?
Also, ASTM B680 does not specify any quantitative pass/fail criteria to test seal efficacy. Is there any rule_of_thumb pass/fail criteria for it or any other standard that we can use to test the anodic seal efficacy?
Regards,
Student - Palo Alto, California
February 15, 2010
Multiple threads merged: please forgive chronology errors and repetition 🙂
Q. I am very new to all of this and I am trying to do the coating weight based off ASTM B137. My calculations do not match that of my laboratories. I am not sure how to do this calculation. Please Help.
Amber SpellmanPlating Shop Employee - Denver, Colorado
February 25, 2010
Q. I have a question about the procedure for stripping coating weight on ASTM B137. What is the purpose of swabbing surface with 10% NaOH in the section of Test Specimen (Sec 5)?
Steve Chien- Auburn, Washington
September 24, 2010

Q, A, or Comment on THIS thread -or- Start a NEW Thread