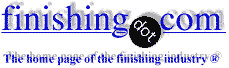
-----
Protection for steel screws - high temp/humidity
Q. What are the best corrosion protections for cold-rolled steel screws (small)? It must withstand high temperature and high humidity for thousands of hours and be compatible with Magnesium.
We've tried .0002" Zn plating with Yellow Chromate and also Blue Bright Chromate. Both are severely damaged after several hundred hours. We've also seen good results from some Japanese screws that are specified as .0002" Zn galvanized with Yellow Chromate.
Any general insight would be appreciated.
- Carlsbad, California, USA
2001
A. You've tried zinc plating and chromating and not found it successful; yet you have observed Japanese parts that are zinc plated and chromated and are satisfactory. I would therefore say that the difference lies in a post-dip lacquer or wax.
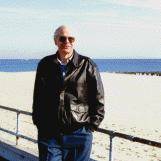
Ted Mooney, P.E.
Striving to live Aloha
(Ted can offer longterm or instant help)
finishing.com - Pine Beach, New Jersey
A. Section samples from the Japanese parts and the failed samples. The specification is the same, so the problem is probably thin zinc on the failed parts. Also check if the chromate is hexchrome based.


Tom Pullizzi
Falls Township, Pennsylvania
Thank you for your responses.
Q. Tom,
Can you be a little more descriptive please. I know very little about finishes. Section the samples and do what exactly? Examine under a microscope? I thought that ALL yellow chromate WAS Hexavalent Chromium based. If not, then what effect does it have (other than the negative environment effects).
Thanks again.
- Carlsbad, California
A. Hello, Del Doty,
Some of the factors that affect corrosion resistance needs of "Several Hundred Hours" are given below.
1) Tom Pullizzi's statement on uniformity of zinc thickness is an extremely valid point. ("Thin zinc" is what was stated, in comparison to what was thicker zinc deposited on the rest of the screw.)
2) The yellow chromate requires a topcoat of the " Non Organic " type. There's a lot of Professional nomenclature . Some call it Inorganic Topcoats, others , sealers, and a lot of Brand names prevail. These materials are available from almost plating chemical vendors in the USA. The ideal sealer will be a self healing type that repairs itself after torque is applied while being tightened.
3) The choice of a Zinc plating process acquires importance where uniform zinc distribution is a critical factor. The industry has accepted ACF ( Alkaline Cyanide Free ) Zinc as a norm when even ( Read "Uniform " ) zinc metal distribution is a key factor to good corrosion resistance. The ACF process puts even amounts of zinc in threads, the shank and head of the screw.
Parts to be ACF plated will need Anodic Electrocaustic conditioning treatment for 6 to 10 minutes at 15 to 30 ASF at 50 to 60 °C in a 125 to 150 gram per liter Caustic solution if the parts are hardened or High carbon steel. Parts then go direct to the ACF bath and zinc will then deposit normally - and evenly all over.
4) The choice becomes wider when you begin to consider the Alkaline Zinc Iron alloy baths , where the life to red rust is within the " Hundreds of hours " capability you expressed a desire for. Regular zinc lasts much less than Zinc Iron alloy. The Japanese use Zinc Iron alloy a lot and I will not be surprised if you eventually confirm this is a Zinc Iron alloy plating case. Unfortunately in the USA, the current trend towards zinc iron alloy use is very limited and availability appears limited to a couple of manufacturers .
5) Other alloys ( Zinc Nickel, Zinc - Cobalt )deposited from Acid baths do provide nearly comparable / good corrosion resistance values, but when metal distribution and the economics of obtaining a given level of corrosion resistance, or matching a stated standard ( JIS, ASTM, DIN . BSS ) are the benchmark, Zinc Iron alloy plated out of an Alkaline bath is a worthy contender for position one scoring good points in both departments . Cost and Corrosion resistance. And the user friendly part.
Regards
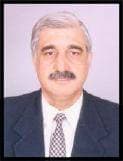
Asif Nurie [deceased] [deceased]
- New Delhi, India
With deep sadness we acknowledge the passing of Asif on Jan 24, 2016
Q, A, or Comment on THIS thread -or- Start a NEW Thread