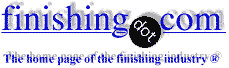
-----
Should Galvanic Corrosion be a concern in computer chassis?
1998
We manufacture equipment used in the computer industry. The question that I have relates to plating sheet metal parts with Electrolysis Nickel verses using a Zinc (ASTM B633 Type 3) plating. We have an engineer that has specified Electrolysis Nickel on a chassis with complex bends because he feels that the process used to plate Zinc does not yield acceptable coverage (special electrodes would be required). Because of a concern about galvanic corrosion parts that come in contact with the above part are also specified as electrolysis nickel rather than zinc. Some venders seem to prefer to work with Zinc. In some cases the plating is then covered with paint.
Where can I find more information on galvanic corrosion and its relative importance in our market. (I can understand that concern to equipment that has a long life cycle exposed to the weather but I need help assessing the issue as it relates to computer assemblies.
Is Galvanic corrosion a concern when designing a computer chassis (typical office environment) using parts in contact with each other that have been plated with less Nickel and Zinc? Is there any reason to specify that all of the parts be either one or the other type of plating? Thank you
Phillip HoglandRimage Corp
Zinc plating is the usual approach, and I am not familiar with any computer chassis being electroless nickel plated, although I can't say it isn't done.
The zinc plating solution should be alkaline, and preferably cyanide, due to its far greater throwing power. Acid zinc is probably inappropriate for chassis work. Yes, auxiliary anodes are beneficial and sometimes mandatory for good coverage; but so what? It will still probably be much less expensive to zinc plate the chassis than to electroless nickel plate them.
There are some environments where electroless nickel exhibits superior corrosion resistance to zinc, and some where it doesn't. It is important to recognize that nickel is cathodic to steel and accelerates its corrosion if the coating is breached. Zinc is anodic and protects steel even if there are scratches or pores.
Consider the screws. They are small in surface area, and thus will corrode rapidly if anodic to the chassis. Will they also be electroless nickel plated?
I'm not looking at the chassis, and I don't know the full story, but my first thought is that switching from zinc to electroless nickel, in an application where it isn't necessary and may be detrimental, to avoid the use of auxiliary anodes, which aren't that big a deal, isn't the right approach.
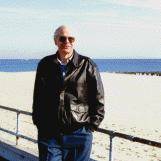
Ted Mooney, P.E.
Striving to live Aloha
finishing.com - Pine Beach, New Jersey
Ted is absolutely correct about using internal anodes. Properly designed, zinc plating coverage can be quite uniform, especially if you can find a plating supplier using a cyanide electrolyte. Even with the extra tooling costs it will cost much less than electroless nickel plating.
Have you considered using precoated sheet steel? Coverage is guaranteed and you can avoid plating costs entirely. Galvanneal and electrogalvanized sheet stock work well in many cases for computer frames and chassis. Many computer manufacturers are now using precoated steels for some or all of their sheet metal parts. Pop the top on your PC and have a look inside. Chances are it's precoated steel inside. In a benign office atmosphere, precoated steels can provide adequate corrosion protection, even on cut edges. It may not work for everyone, but it's well worth considering.
Gary Krech- Brighton, Colorado
1997
1997
I am a believer in electroless nickel, but it is probably an overkill for a chassis. New Alkaline nickels work well and are not as expensive as EN.
From a practical point, I would find a plater that would do one for you in Alkaline zinc with a yellow chromate. You can take this unit and use an instrument with a small probe to see what coverage the plater got in the corners.(Well, very near the corner)
Any contract based on the demo part should have very specific thickness in the corners specified.
Quality zinc is the way to go. The cheapest plater is rarely the best and the most expensive is not always the best. Look for a good one that will take the time to understand your problem and offer some guarentees of quality and delivery.
James Watts- Navarre, Florida
As a very slight clarification of what James said, because it is important to get good coverage in the corners but difficult to measure, the ambiguity is often resolved by specifying the minimum thickness at 'any spot that can be touched by a 3/4" diameter ball' (or some other diameter).
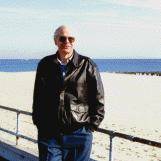
Ted Mooney, P.E.
Striving to live Aloha
finishing.com - Pine Beach, New Jersey
1998
Many job shop operations throughout the US plate zinc onto computer chassis and alkaline non-cyanide zinc plating is the process of choice for computer chassis. Cyanide zinc plating is no longer an economically viable option in the United States. Commercial alkaline non-cyanide zinc systems have better throw, are brighter, are more efficient, and are cheaper to operate.
Richard PainterCleveland, Ohio
1998
Mr. Painter might be right about the advantages of non-cyanide, but as late as last year, I know of at least one plater who was still using cyanide zinc for chassis. He did have a non-cyanide zinc recently added to the line, and the operator preferred the latter, while the owner liked the cyanide zinc better. I can't recall the reasons.
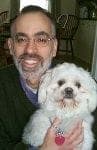

Tom Pullizzi
Falls Township, Pennsylvania
1998
I'll second that, Tom. While it is highly desirable to move from cyanide to alkaline non-cyanide for safety, to minimize hassles over cyanide in the effluent, and because the public is paranoid, I think it may be overstatement to say that cyanide plating is no longer an economically viable option.
If there is a study by Pavco that demonstrates that one of their competitor's non-cyanide baths delivers better brightness, throwing power, and efficiency than cyanide zinc, I'd like to see it. Similarly, if one of their competitors has a study showing that Pavco's system is better than cyanide, I'd like to see that too. Otherwise, with cyanide no longer having a champion with a vested interest, such studies are a bit hard to accept, and only remind me that the scientific literature had a very different cast when DuPont was still championing cyanide.
But, in the end, the fact is that alkaline non-cyanide zinc does work, and that's all that is really necessary considering the disadvantages of cyanide.
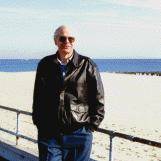
Ted Mooney, P.E.
Striving to live Aloha
finishing.com - Pine Beach, New Jersey
1998
Galvanic corrosion should be taken into consideration for the future computer design because computers are not only used in offices but also on production lines where the serious corrosion environment is often encountered. Although plated sheets will be further painted, scratching and partially mechanical damaging are unavoidable during use and transportation. Both nickel-plating and zinc plating have advantages and disadvantages. Of course, zinc plating is cheaper than nickel plating. More importantly, zinc as a sacrificial anode can provide protection for other parts while nickel as a cathode could accelerate the corrosion of other parts in a computer. Using galvanized sheet as computer chassis material is a better choice. As I know, IBM is now thinking about zinc-cobalt alloy plating with blue chromating post-treatment in computer chassis design.
Ling Hao- Grand Rapids, Michigan
1998
I am currently working for a corporation that has installed a large number of computer systems, ISDN equipment, office LAN equipment, printers, and P.O.S. terminals in Pool supply companies in the Florida area. We currently seem to be experiencing problems with rust and corrosion involving rough edges, screws, I.O. Slots, drives, and print mechanisms. Where would would a company such as ours find more information on the chemicals that could cause this problem (chlorine, acids, etc..)? We are under a near law-suit condition, and withholding of final payment, since we are unable to bring these machines to a near 100% perfection. At least twice a week a CD-ROM, power supply, or motherboard is failing. We see large amounts of rust forming around the power supply, and all screws inside and outside of the cases on more than half the machines, and discoloration covering the copper wiring on some circuit boards.
We have only been able to find one other case of this happening in a pool supply store, but most supply stores we have examined seem to be well ventilated, and are using older IBM 286/386 machines. The machines we are using are built with cheaper minitower cases, but the parts inside are quality (panasonic, western digital, diamond multimedia, intel etherexpress, intel CPU, US RAM, etc..) components. Could the older IBM machines be less effected by the chemical content of the air?
Signed.. Confused..
Alfred KnoxWinter Park Studios
1998
Sequent manufactures computer systems which are enclosed in sheet metal housings. We recently began a new project which included some cost-reductions. One of the proposed cost reductions was to change our electroless Ni plated aluminum and steel chassis parts to a pre-plated cold-rolled steel design. The previous design which used the Ni plating was chosen for cosmetic appearance, compatibility with the Au flash plating on the circuit boards, and for the best conductivity with the gaskets used for sealing the enclosure for electromagnetic compatibility (EMC). Anyway, the logistics of the chassis change to pre-plated cold-rolled steel (GALXC material) was such that the proposal included changing only the outside chassis, while the inner chassis parts (brackets, several circuit-board holders, etc) were to remain as Ni plated parts. The 1st test of this in our humidity chamber was a disaster. Several of the newer Zn pre-plated parts were covered in a white residue, which we suspect is galvanic corrosion. The EMC testing showed a significant degradation in shielding effectiveness. I would appreciate pointers to consultants, testing labs, and other resources which could help us answer the following questions: 1) Is the particular residue we are seeing from our humidity tests a result of galvanic corrosion? 2) Is the proposal of cost-savings by conversion from Ni plate to Zn pre-plated steel salvageable? 3) For galvanic compatibility, do we need to convert the entire chassis from Ni to Zn, and never let the two types of plating touch in any enclosure? 4) For galvanic compatibility, do we need to change the design of the circuit boards or the chassis to ensure that Zn plated steel never touches the Au plating on the circuit board?
Pat Chewningcomputer systems - Portland Oregon
1999
Q, A, or Comment on THIS thread -or- Start a NEW Thread