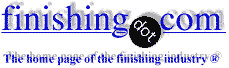
-----
Proper temperature and humidity level for storing steel & EG
Q. What is the proper temperature and humidity level to keep steel from rusting? We buy large quantities of steel tubing and sometimes get flash rust on the steel.
Bryan Lepley- Kalamazoo, Michigan
A. I don't believe you can prevent steel from rusting to some extent in almost any ambient atmosphere, where temperature makes diurnal moves and there is some moisture in the air. Maybe in Death Valley, CA for certain parts of the year.
You will need a rust preventative coating for MI.
Here is an old formula:
200 gal. tung oil
⇦ on
eBay
or
Amazon [affil link]
; heat to gelatinous stage
add:
20 gal. sardine oil
cool;
add:
60 gal. whale oil
sardine oil, 200 gal.
1/2% b.v. manganese cobalt drier
If whale oil is too pricey, you could probably find other proprietary formulas:-)
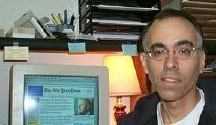

Tom Pullizzi
Falls Township, Pennsylvania
A. Hi, Tom. Must this be sperm oil, or will any whale oil do? Next time I'm on Nantucket when the whalers come in I'll check what they're getting for it these days :-)
If not a proprietary rust preventative, maybe we should race forward in time to WWI and cosmoline?
More seriously, if the warehouse can be maintained at as low humidity and temperature as practical, rusting can probably be limited. Still, flash rust is more a function of the surface condition than the storage conditions. A clean, pickled surface can flash rust in hours -- before it hits the shipping dock, let alone the receiving dock.
Regards,
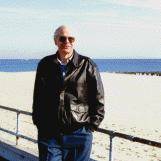
Ted Mooney, P.E.
Striving to live Aloha
(Ted can offer longterm or instant help)
finishing.com - Pine Beach, New Jersey
February 19, 2009
2007
Q. EG metal brackets parked in our warehouse for 6 months are found rusty at bend areas & spot weld areas. I suspect this is because of my warehouse environment.
I would like to know the following:
1.Recommended temperature & humidity of storage area to store this galvanised steel.
2. Recommended temperature & humidity to test the e.g., parts inside the chamber. (My objective is to inspect the part upfront to confirm that the part cannot rust if stored in good environment for at least 6 months.)
Appreciate your valuable advise.
Thanks
Frank
Supplier Quality Engineer - Marsiling, Singapore
2007
A. Is the bending & welding performed before or after plating?
Is the zinc plating chromated? Chromating is essential in a humid environment.
To what specification is the zinc plating and chromating performed?
What material(s) are the storage racks?
The (hot dip) galvanizing societies have information on storing zinc-coated material to avoid white corrosion. Also, on touch-up of damaged zinc coatings.
American Galvanizers Association (AGA) https://www.galvanizeit.org
Galvanizers Association of Australia (GAA) http://www.gaa.com.au/
Galvanizers Association (UK) http://www.hdg.org.uk/
- Goleta, California

Rest in peace, Ken. Thank you for your hard work which the finishing world, and we at finishing.com, continue to benefit from.
A. Hi Milton.
EG is not actually galvanized, it is zinc electroplated, and offers far less corrosion resistance than actual hot dip galvanizing because of the greatly reduced thickness.
While it is good to store the stuff properly, as dry and as cool as practical, it is also vital to know the plating specs and to assure that they are maintained -- because all your efforts will be to no avail if the vendor reduces the plating thickness/quality, and all your expensive efforts may be unnecessary if they increase it.
But very important, regardless of temperature and humidity, is air circulation. Zinc reacts with the air to form very stable, impervious, and corrosion resistant zinc carbonate surfaces. This depends upon good exposure to the carbon dioxide in the air, and is one reason that accelerated corrosion testing of galvanized materials is not very indicative of their actual corrosion resistance. You may wish to do a search for "white rust" or "wet storage stain" on this site or on the internet as a whole for further information. Good luck!
Regards,
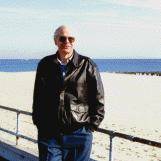
Ted Mooney, P.E.
Striving to live Aloha
(Ted can offer longterm or instant help)
finishing.com - Pine Beach, New Jersey
November 21, 2012
Q, A, or Comment on THIS thread -or- Start a NEW Thread