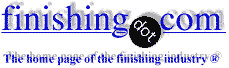
-----
Do-it-yourself anodising
1997
Q. I commenced my internet "life" specifically to find out the pros and cons of anodising. I build and race my own drag racing vehicles and as a consequence make many brackets and parts from aluminium to keep weight to a minimum. Where I live in Queensland in the northern part of Australia puts me about 1200 kilometers from the nearest anodiser, hence my new found "love" of anodising.
Treatment &
Finishing of
Aluminium and
Its Alloys"
by Wernick, Pinner
& Sheasby
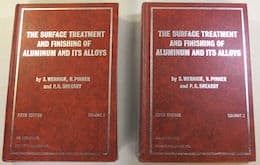
on eBay or Amazon
or AbeBooks
(affil link)
I have anodised most of the aluminium bits and pieces on my car with a good deal of success, so much so, friends have asked me to do their parts, which brings me to the point of this letter.
While I have been happy to do my own bits, I need a few questions answered before I'd be confident enough to put friends parts in a bath of acid.
Currently I am using a bath with about 30 liters of electrolyte, and some sample dyes from Clariant (Australia). I anodise at about .1amp / square inch for about 40 mins. I agitate the solution with a fish tank air pump and maintain the temp at about 25 °C - 30 °C.
I mix the dyes as per manufactures instructions, and leave the work in the dye till the desired color is achieved. I then boil work in clean water for 10 mins. and at least till now, I end up with a nice piece of colored aluminium.
My concerns are:
- All information that I have gleaned from the net gives the sulfuric acid ratio of 10% up as much as 25% / volume of acid to water. What is the correct amount or doesn't it matter ? What strength sulfuric? I can buy acid of 30% strength with s.g. of 1.25 or 98% with s.g. of 1.85. (I am using the 30% strength at a ratio of 2:1 water:acid)
- When has the electrolyte "gone off" and needs replacing?
- The Clariant dyes, do they ever "go off". ( I am aware of the ph requirements)
- What, other than hydrogen is given off during the oxidising process?
- The dyes, do they present any hazards to the user?
- Chemical brightening, prior to anodising, are there any commercial "potions" available?
- I wash the work (after immersion in the electrolyte), in clean water, then in a sodium bicarbonate solution and then clean water, then into the dye. Can the sodium bicarb have any lasting effects on the finish?
- Are there any simple tests I can do to test the quality of my anodising, considering that it is strictly decorative and non structural?
I realise that these questions are of a somewhat basic nature, but I would be grateful if you could clear up some of my concerns. I have tried to purchase some of the references that are listed in finishing.com, but alas, no go, at least in Australia.
I must admit that since I started my foray into anodising, I never had more fun, but I am still "spooked" by the chemistry side and the dangers or problems that may exist with some of these "potions".
Regards.
Rory MClaughlin- Australia
1997
A. I have 30 years experience in anodizing and will try to help answer some of your questions and you are welcome to pose other questions. I may be able to be of help or not.
Sulfuric ratio ideal is 16-18%
98% with 1.85 S.G.
electrolyte coating should not wear off
most organic dyes are not good for outdoor exposure, they will fade in sunlight
Dyes do not present a hazard to user
Chemical brightening prior to anodizing is called a bright dip
Ideal solution of 80-85% phosphoric acid and 3% nitric acid
Specific gravity should be approx. 1.710 to 1.720
Temperature range 200-220 °F
Sodium bicarb should not have any lasting effects on finish.
This should give you a very bright part.
Hope this is of some help.
Raymond Hendrix Troy, TennesseeA. One other consideration for you regarding anodizing parts for your friends race cars is the affect of anodizing on structural components --
-- anodizing significantly decreases fatigue strength, sometimes by up to 50%. This means that anodized structural components will be much more susceptible to fracture over time than components without anodizing. This may or may not be a factor in the components that you are anodizing, but is something to keep in mind.
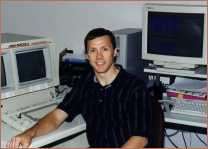
Larry Hanke
Minneapolis, Minnesota
1997
A. I am the project chemist at ACA. As to your questions:
As you treat aluminum parts, whether it is cleaning, etching, bright dipping, or anodizing, aluminum is constantly being removed from the surface. The aluminum that is removed from your part(s) stays in the bath and can affect the quality of the anodic coating, especially in the etch bath and bright dip. (BTW, premixed bright dip solutions are available [in the US, anyhow] from Albright & Wilson). Aluminum in the drag-out from the anodize bath to the dye bath can kill your dye, even if you keep the pH corrected. Also, stored organic dyes can support life (read: MOLD), so watch out.
Gerald Janssen-coil anodizing
1998
What is sodium bicarb?
Q. Dear All,
Can you advise what is sodium bicarb?
Best regards,
Alex
- Hong Kong China
May 19, 2014
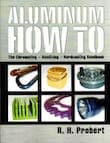
Aluminum How-To
"Chromating - Anodizing - Hardcoating"
by Robert Probert
Also available in Spanish
You'll love this book. Finishing.com has sold almost a thousand copies without a single return request :-)
A. Hi Alex. "Sodium bicarb" is just a slang abbreviation for sodium bicarbonate (NaHC03), aka baking soda. It is a very mild alkaline often used to neutralize acid. As you can read above, sodium bicarbonate is sometimes used for that purpose in the anodizing process.
Regards,
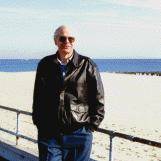
Ted Mooney, P.E.
Striving to live Aloha
(Ted can offer longterm or instant help)
finishing.com - Pine Beach, New Jersey
May 2014
Q. Hi Raymond,
Is the ideal solution of 80-85% phosphoric acid and 3% nitric acid for brighten up? Is this a process just before anodizing?
Best regards,
Alex
- Hong Kong China
May 23, 2014
A. Hi Alex. Raymond's posting was from a long time ago and he's probably not monitoring this thread but, yes, he is speaking about a chemical polishing solution there. It is used to brighten aluminum before anodizing in limited applications like the manufacture of aluminum reflectors. It is not a part of the process in most anodizing shops. This is a very nasty process, so be sure to read up on "aluminum bright dipping" and to visit at least one shop that does it before considering implementing it yourself. Good luck.
Regards,
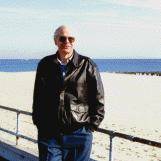
Ted Mooney, P.E.
Striving to live Aloha
(Ted can offer longterm or instant help)
finishing.com - Pine Beach, New Jersey
May 2014
It is 2015 and I am grateful for this info. I am making an acid bath, 98% sulfuric Acid and DI water but I was unsure of the mixture. I bought a hydrometer so I will gauge adding acid until I reach the 1.7 gravity.
Thanks folks!
- doral, florida usa
September 28, 2015
A. A final sulfuric anodising electrolyte density of 1.7 seems too high to me. I've read typical mix should be battery acid ⇦ on eBay or Amazon [affil link] (sg of 1.265) cut 50/50 with DI water, so density is going to end up around 1.13 or am I being stupid?
John Stokesengineering - abergavenny, Gwent, wales
January 1, 2016
A. Hi Rajiv. Hi John. You guys just need to take your time and read the page a little more slowly ... Ray's 1.7 S.G. was referring to the chemical bright dip process, not the anodizing process :-)
For anodizing he suggested 16-18% sulfuric acid (by weight), and his 16% by weight is quite widely accepted. John, I assume you are a hobbyist from your reference to battery acid ⇦ on eBay or Amazon [affil link] . Professionals dilute Electronic Grade 98% sulfuric acid rather than battery acid ⇦ on eBay or Amazon [affil link] . You can't reliably go by specific gravity because dissolved aluminum throws it off. Good luck.
Regards,
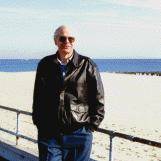
Ted Mooney, P.E.
Striving to live Aloha
(Ted can offer longterm or instant help)
finishing.com - Pine Beach, New Jersey
February 2016
Yes sorry you are correct I should have read the post fully from the outset. 16% as you say is stated as the sulfuric to water electrolyte ratio by weight. I do use Electronic grade sulfuric Acid concentrate with a density of 98% I was referring to an article that based it's starting mix using battery acid that is already supplied with a lower density initial density.
skirrid engineering - abergavenny, Gwent, wales
February 4, 2016
Storage of Anodizing Acids
Q. Getting started Anodizing and I am wanting to know how to store the various chemicals. Not a full time hobby so leaving in the tank is not an option. I also understand that what may work for short term, may not be suitable for longer storage. Obviously the original container would be preferred, but as I will be diluting, my storage volume will not be the same.
My Battery Acid came in a plastic container. Can the diluted Sulfuric Acid anodizing bath be stored in a standard 'Home Depot' 5 Gal bucket? If not, suggestion for ~5 Gal storage.
My 67% Nitric Acid also came in plastic and instructions to transfer to glass asap. The website stated that concentrations over 30% must be stored in glass, but makes no mention for concentrations under 30%. Can 10% Nitric acid be stored in the 'Home Depot' bucket? I've searched but can find no references to Nitric Acid storage at lower concentrations. This is the one that I am most concerned about.
Frustrated because I just gave away all my 5-6 gal carboys (was beer making).
I do not foresee an issue with Dyes in the 5 gal buckets. Let me know if I am wrong on this point.
Thanx
Getting Started with Aluminum Anodizing - Oklahoma City, Oklahoma
February 4, 2016
A. Hello Sterling, I have only used polypropylene tanks or buckets for storage of acids. With the acid concentrations that you described a white polypro with a lid should be fine.
Mark BakerProcess Engineering - Phoenix, Arizona USA
February 9, 2016
A. You would be just fine storing either or both of the chemicals you mentioned in a 5 gal Home Depo plastic bucket. If you happen to splash some on the metal handle, you'll want to rinse that off, as it will corrode.
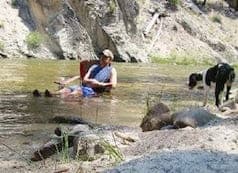
Marc Green
anodizer - Boise, Idaho
February 13, 2016
Is it possible to anodize heavy duty aluminum foil?
February 10, 2018Q. First I would like to say thanks to everyone who contributes their knowledge and experience here. I have no background in finishing of any kind, and have only recently began researching these processes. I've been reading many posts & responses on this forum and have learned so much. I will be attempting amateur anodization with a 12V supply rated for 20A continuous. For the current project I'm working on, I'm curious to know if it is possible to anodize heavy duty aluminum kitchen foil, approximately a 12" square foot.
Here's what I've learned from y'all:
The 720 rule yields a result of a 1 mil coating for a square foot, taking 36 minutes at 20 ASF. It would most likely be Type II or 'decorative' anodizing with Sulfuric Acid, as Chromic seems to be unusual for home brew anodizing.
Here's what has me scratching my head.
Household 'heavy duty' Aluminum foil is on average 0.94 mils thick, but the above calculation is for a 1 mil thick anodized coating. Could I simply reduce the time the foil is submerged to achieve a very thin coating?
Intuitively it seems plausible, but then why is there a clear distinction of coating thickness ranges between all three Types?
Additionally, the military spec (not sure if that's what it's called) states that for Type II a 67/33% ratio thing occurs, which confuses me a bit more about how that plays a role with these processes a thicknesses of materials to be anodized.
I am genuinely interested in conceptually and practically understanding this process, and what the military standards of differentiating processes of anodizing have to do with what is actually possible, say Type II anodizing thin foil.
Again, I truly appreciate the time y'all dedicate to helping the community and even new learners like me. Thanks!
Student designing a product - Dallas, Texas, USA
A. Hi Nathan. Please start with our "Introduction to Anodizing" if you haven't yet seen it.
Although the 720 Rule is called a Rule, it probably really ought to be called the 720 Relationship because you are right that it's just about the relationship between thickness vs. time & amperage; it's not a "rule" saying that you should anodize to a full .001" thickness; in fact, regular Type II anodizing is almost never that thick. It's usually more like .0002" thick, although it might be .0004-.0005" for fully saturated black color and .0007" for architectural applications.
You mention a 67/33 'ratio', but 50/50 is more commonly quoted, and what that means is that the anodized film is generated from the aluminum of the article itself, such that some base metal is consumed in making the anodizing. If you do .0002" anodizing, you'll consume about .0001" of the aluminum. So if you anodize only one side of the foil to .0002" thick anodizing, it will only be about .0001" thicker after anodizing.
Regards,
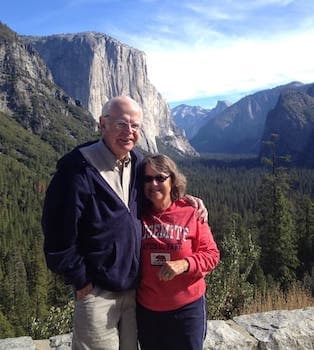
Ted Mooney, P.E. RET
Striving to live Aloha
(Ted can offer longterm or instant help)
finishing.com - Pine Beach, New Jersey
February 2018
A. Nathan
A 12" x 12" square will yield 2 sq ft of surface area; 2 sides.
At 1 mil thick you will need multiple contact points to keep from burning/arcing. There is little material to carry the current. And you will lose the ability to carry current as the aluminum is replaced by anodize.
After anodize the foil will be quite brittle. Handle with care.
- Green Mountain Falls, Colorado
February 13, 2018
Q. Can anyone tell me: if I don't want to use DI water in sulfuric bath, then what chemical can I insert in the bath to clean the water and sulfuric mixture?
Amber Azamazam cnc machining - daska Pakistan
May 6, 2018
A. Hi Amber. I don't think that will be practical. Although it is relatively easy to remove trace contaminants from the makeup water via de-ionization (aka demineralization), once you've added the sulfuric acid and dissolved aluminum from the anodizing process, you probably have no practical way of removing the contaminants. But please tell us what contaminant you suspect or wish to deal with.
Regards,
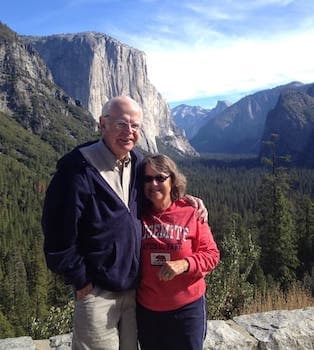
Ted Mooney, P.E. RET
Striving to live Aloha
(Ted can offer longterm or instant help)
finishing.com - Pine Beach, New Jersey
May 2018
May 7, 2018
Q.
I have started a small anodizing setup in Pakistan, and here there is no help me to do better and learn better. So I post here and got answer faster.
I had made sulfuric acid bath with gravity of 15 or 1.13 and mixing it in water with 20% ratio and its temp is 22 °C.
So I actually ask: can I use azelaic acid or boric acid to clean my sulfuric bath?
----
Q. What is best method to shine aluminum before sulfuric acid anodizing bath.
If anyone knows, than tell me about mixture and its value with %'s.
azam cnc machining - daska Pakistan
A. Hi again Amber. You are certainly welcome to research your idea or to experiment with it, but I have personally never heard of anyone cleaning contamination out of an anodizing bath in this way. Most of us cannot afford the time to re-invent a new method of anodizing with azelaic & boric acid in solution, and then develop a technology based upon it, thus the famous quotation often attributed to Newton: "If I have seen further it is by standing on the shoulders of Giants."
So if you want to get on with practical anodizing rather than engaging in raw research, I think you must start with standard methods. You'll need to devote hundreds of hours to the subject, and no one will teach you one-on-one in that fashion, so you must somehow obtain books on anodizing or resign yourself to trying to learn on-line by becoming highly proficient with search engines. We have hundreds of threads about anodizing on-line on this one site alone, and dozens about brightening aluminum before or after anodizing. Books are a much better way to go, but if you absolutely can't find them in Pakistan's libraries, you can start with our "Introduction to Anodizing of Aluminum". Best of luck.
Regards,
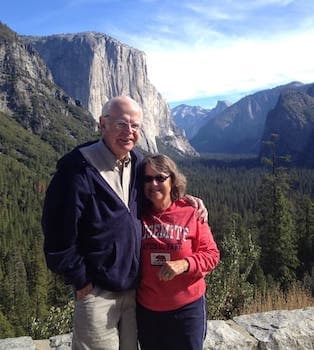
Ted Mooney, P.E. RET
Striving to live Aloha
(Ted can offer longterm or instant help)
finishing.com - Pine Beach, New Jersey
May 2018
Q. Can you tell me again how I brighten aluminium parts before sulfuric bath anodize process?
I talk about bright dip tank and talk about its ratio to mixing chemicals.
What are the chemicals used and what process to do to brighten and shine parts.
Thanks again!
azam cnc machining - daska Pakistan
May 7, 2018
A. Hi again. Please search the site for "aluminum bright dip", read the threads, and after that I will try to answer your question. Presumably by then you will have a vessel on hand, built of type 316L stainless steel, and double walled for containment for when the inner tank eventually leaks? You will have this tank and at least its first rinse completely contained in a ventilated "garage" with proper exhaust ventilation and fume scrubbing. You will have an automated hoist carrying the parts to it, and a plan for under what conditions people can safely enter that area. And you will have researched dealing with NOx fumes.
Bright dipping is difficult and risk-prone; only a small percentage of highly experienced anodizing shops perform it. I have only seen three such installations in my whole career and been involved in the design of only one in a whole lifetime of work as a plating & anodizing equipment engineer. The idea that a person who says they can get no hands-on training in any of this wants to start a bright-dipping operation is quite frightening to me.
Have you considered trying to get a work visa and a job for a year in an anodizing shop which does bright dipping to learn this process, or to offer your anodizing services to customers who do not require bright dipping? Your life is priceless but possibly at risk if you try to offer bright dipping services with no knowledge of them. Good luck.
Regards,
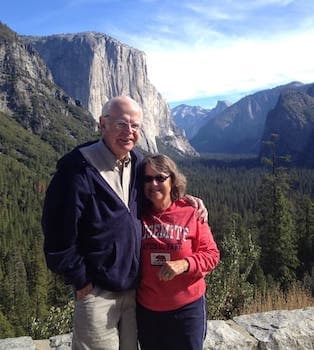
Ted Mooney, P.E. RET
Striving to live Aloha
(Ted can offer longterm or instant help)
finishing.com - Pine Beach, New Jersey
May 2018
Q.
I have made a mixture of 85% phosphoric acid 2.5% nitric acid and aluminum trihydrate and the rest is water and its work is good. But in Pakistan it's difficult to find aluminium trihydrate.
Here is my question: can you tell me difference between aluminium oxide and aluminium trihydrate?
Or can I use aluminium oxide at the place of aluminum trihydrate?
Thanks
azam cnc machining - daska Pakistan
May 8, 2018
A. Dear Amber,
I would suggest to use nitric and sulfuric acid mixture at 50 °C for brightening the parts before anodizing.
- Abu dhabi
November 5, 2018

Q, A, or Comment on THIS thread -or- Start a NEW Thread