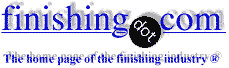
-----
Corrosion Protection Value of different of zinc plating solutions
Is zinc plated parts plated by cyanide or acid chloride type solution with the same thickness provide the same corrosion protection via ASTM B117 salt spray test ? or which type of zinc plating solution is better for the corrosion protection ?
Lawrence Chiu- Hong Kong
1998
My opinion, not necessarily fact.
If you use a standard panel as a method of comparison, you probably will get similar answers. If you use a part that is complex in the salt spray, you probably will get better results out of the cyanide as it normally has better throw in the low density areas so will be thicker there. I feel cyanide zinc takes chromate easier so may be slightly better. The real answer is how that particular plater runs his line. Either one could be superior to the other based on numerous factors of the plating process.
James Watts- Navarre, Florida
1997
I'd agree with James. There have been occasional articles over the years, which we could dig out, where a supplier claimed better corrosion performance for one or another. I vaguely recall the cyanide purveyors making that claim, as I recollect, in the letters section of Plating magazine. Later an acid zinc supplier made a published claim for superiority. But I think the operative phrase remains "zinc is zinc".
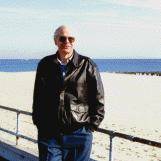
Ted Mooney, P.E.
Striving to live Aloha
(Ted can offer longterm or instant help)
finishing.com - Pine Beach, New Jersey
Some time ago, I had cause to ask the same question to some platers in the Far East. The reply that I got, and it was unanimous, was in favor of Alkaline Non Cyanide Zinc. The reason given is explained as follows: Superiority of plated zinc is influenced by a tiny co-deposition of iron with the zinc. If we use a cyanide type zinc, the iron complexes with cyanide and will not co-deposit. With acid zinc, we add hydrogen peroxide periodically to oxidize and precipitate the iron, or we oxidize it by air agitation. It then is typically removed by filtration, and does not co-deposit with the zinc. The Alkaline Non Cyanide on the other hand will co-deposit a small amount of iron with the zinc. The net result is a form of zinc iron, although the amount of iron is very small. When a chromate is applied, and allowed to stand for 24-48 hours, and then salt spray tested, you should see approx. 24 - 36 hour advantage for the non cyanide.
Anyone who has heard of this belief, please log on.
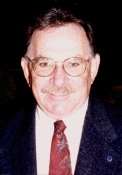

Ed Budman [dec]
- Pennsylvania
With deep sadness we advise that our good friend Ed passed away Nov. 24, 2018
1997
Co-deposit a small amount of iron with the zinc , have a better salt spray test result ? How small amount of iron is ? Is the amount of iron controllable ?
Lawrence Chiu- Hong Kong
1997
1998
I believe that these people in the "far east" may have been grasping with this co-deposition theory. The physical differences between acid chloride and alkaline zinc could be the reason for the small difference in salt spray protection.
The acid chloride zinc is deposited in a columnar fashion. The zinc is like telephone poles standing tightly packed in a field. The salt spray can work it's way down the columns.
The alkaline zinc is deposited in a laminar fashion. The zinc is like sheets of metal overlapping each other . This is the same reason that it is more difficult, or challenging to chromate alkaline zinc. The flat zinc, or sheets if you will, must have a more reactive chromate than the columnar zinc to penetrate the surface. The acid zinc, or columnar, has a capillary action with the chromate.
Regards,
Mike McDonald- Jefferson, Wisconsin
In my opinion there are only minor differences in corrosion resistance to the neutral salt spray test as long as we speak about alloying elements as iron and cobalt under 1% ww of the zinc coating. The main advantage of the alloying element lies in the improvement of the chromate containing passive layer in the post-treatment stage : the occurrence of white rust can be postponed considerably using zinc-alloys of iron or cobalt , especially the black passivation treatment.
Cesar A Boose- Netherlands
---
Q, A, or Comment on THIS thread -or- Start a NEW Thread