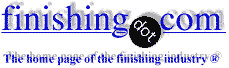
-----
Nickel diffusion barrier between copper and silver
Q. Currently we have a problem requiring the use of a nickel diffusion barrier between copper and silver plating in the internal surfaces of flexible waveguide. The configuration of flexible waveguide is a rectangular cross section using full radius for the narrow walls, a bellows shape where the depth of the convolution is approximately 5 times the width of the opening and the entire structure is seamless. Does anyone have information or experience concerning the use of pulse plating and/or pulse-periodic-reversed plating with sulphate and sulphamate nickel baths where internal throwing power into recess cavities has been demonstrated? Conventional DC and standard periodic-reversed plating works well with cyanide silver and copper baths, but does not seem to work with the nickel baths. I need a bath composition to provide low deposit stress and high ductility to avoid peeling and cracking when the flexguide is formed. Comments?
Richard V. Basil, Jrantenna product center
1998
A. Richard,
As soon as you say low stress, you have nearly specified sulfamate
nickel. I have never used pulsed on sulfamate but have read that it changes the nickel deposit. Some pluses and some minuses. You will need to do a literature search to determine its suitability for you.
You have not said the size of the part. I have seen them under 3" to over 5'. Makes a huge difference. You might be able to use an internal anode with standoffs. Platinized titanium works beautifully, BUT destroys the bath with sustained use. Pure nickel wire might be used if it were done very carefully. I have heard of people using 400 nickel for anodes in critical spaces. Your end user probably will have to agree to whatever you do.
James Watts- Navarre, Florida
1997
A. Richard:
If your waveguide is electroformed, it is usually much easier to deposit the entire required coating system (silver/nickel/copper) onto the mandrel and then form the waveguide. After the mandrel is removed, you get your waveguide with the coating system in place.
I've done things like that in the past and know a few vendors capable of doing it today.
E-Mail me if you need specifics.
All the published data on PR or pulse plating with sulfamate nickel I ever saw showed a diminished rather than improved throwing power.
Good luck from PlaterB
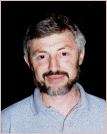

"PlaterB" Berl Stein
NiCoForm, Inc.

Rochester, New York
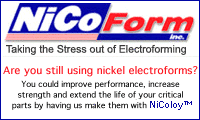
1997
A. Richard,
I agree with Mr. Watts with respect to stress and ductility: Ni Sulfamate is the was to go. I can't contribute to the pulse plating aspect of your question. However your problem in throwing power is not unlike that of plating high aspect ratio through holes on PC boards ( refer to my paper in the reference section of finishing.com ) . You might check with vendors providing this kind of plating chemistry.
Paul Stransky- Putnam, Connecticut
1997
1997
A. I have been using reverse-pulsing in nickel sulphamate for about six months now. In my experience, the throwing power is improved significantly in comparison with dc. I am using plating equipment and cycle info from a company named Dynatronix.
Chris NenovQ, A, or Comment on THIS thread -or- Start a NEW Thread