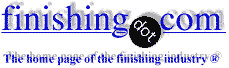
-----
Water quality / chloride contamination in anodizing

Q. I use R.O. water in the rinsing baths that I have, and I also use it to prepare the anodizing and coloring baths, as well as the hot rinse bath, and this water contains 111.8 micro-Siemens per centimeter.
My question is divided into two parts:
1- What are the correct specifications for water to use in these processes?
2- What is the difference between R.O. water and D.I water and which is better to use?
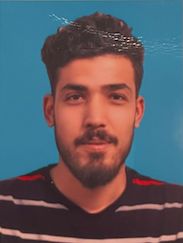
mohammed alzwey
chemical engineering - Bengahazi, Libya
October 5, 2023
A. Hi Mohammed,
Using clean water is of course the right thing to do, the lower you can get the conductivity the better.
Specifications and audit authorities often call for the rinse water to be below 20µs from the R.O. machine or ion exchange columns. It will go higher than that as the water is used in the rinse tanks, but as long as you have several tank volume changes per day relative to the amount of work that runs through the tanks, then you should be OK.
As a rule of thumb, the conductivity, in this case will generally remain low. Hot rinses should be kept below 100µS, and dumped once they rise above that.
The R.O. will remove chloride. A turbidity test of the water with silver nitrate
⇦ on
eBay or
Amazon [affil link]
will confirm its absence.
As to R.O. / D.I., R.O. produced water is de-ionised, (DI).
There are, as you will know a number of ways to de-ionise water, so the the difference is just down to how you made it. As long as the conductivity is low enough for your purpose, by what ever method of de-ionising you use, then you are good to go.
I hope this is of use to you.
Best regards
Mark
- A dull, cloudy rock in the Irish sea
October 6, 2023
⇩ Related postings, oldest first ⇩
Q. We are in the process of developing quality control limits for the water used in surface finishing of aluminum alloys, including 7075, 6061 and 2024. One of our primary concerns is to avoid the formation of chloride induced pits in various processes such as cleaning, anodizing, fluorescent penetrant inspection and wet blasting. Is anyone aware of an established "threshold" or safe chloride ion activity that will not induce pits on brief (4 hour) exposure ? A reference from the literature would be much appreciated.
Thanks in advance for your help,
Blair Smithaerospace - Windsor Locks, Connecticut
1996
Treatment &
Finishing of
Aluminium and
Its Alloys"
by Wernick, Pinner
& Sheasby
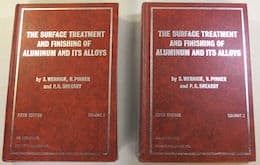
on eBay or Amazon
or AbeBooks
(affil link)
A. Hi,
Call the Materials Laboratory at the old Bendix plant in Teterboro, NJ, It is now Allied Signal Aerospace. Ask for Fred, tell him I said hello.
There used to be a limit on the chromic acid anodizing solution for aluminum and Beryllium of Chloride, 0.2 grams/liter as NaCl and sulphate, 0.5 g/liter as H2SO4. There was also a chloride spec for Martin Hard Coating, but I don't remember what it was.
We did not have any reference to chloride contamination for fluorescent penetrant inspection, we used tap water for all, including the plating shop, for many years.
I was unsuccessful in proving that chloride alone caused etching of aluminum parts, there might be an interaction, or there might be some metallurgical reason why, in the same tank load, we had some parts destroyed by etching, and the others without a trace of a problem.
But I can tell you this, in almost every case, the etching started in a blind, threaded hole. We used to wash out the holes with a jet of water, but I am not sure how effective it was. Once the etching started, there was no stopping it.
References which may help:
Techniques for Plating on Aluminum I and II , Nov and Dec, 1969, "Products Finishing" magazine (has quite a few other references). The Dec article mentions hypodermic needle hubs, isn't that your business?
MIL-A-8625 / MIL-PRF-8625
[⇦ this spec on DLA] rev.E, paragraph 6.4 mentions chloride as a contaminant, no level.
Strategies for electroless nickel plating aluminum, Surfyn, 90, Yarkosky, et al.
Hard anodizing of aircraft fuel metering components, Wiesner and Meers, 45th annual technical proceedings, 1958, AES.
Good Luck!
P.S.: The Canning Handbook [on
eBay,
Amazon,
AbeBooks affil links] gives chloride limits for anodizing solutions similar to the ones we used at Bendix, since you were looking for references.
-tom
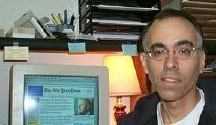

Tom Pullizzi
Falls Township, Pennsylvania
A. Why worry about it? Most references recommend using DI water in a minimum of the anodizing tank and the seal tank. Most places will use it in as many tanks as they can afford. To me, controlling it is a waste of lab time and "another tic to chase" as some of my British pilot friends would say. Avoid the whole mess, use DI and avoid the problems. Your sister company , PWA has some limits, but I will question where they got them from.
James Watts- Navarre, Florida
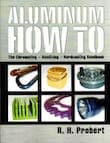
Aluminum How-To
"Chromating - Anodizing - Hardcoating"
by Robert Probert
Also available in Spanish
You'll love this book. Finishing.com has sold almost a thousand copies without a single return request :-)
James, but nobody runs a DI unit without some limits on the purity, I suppose we are trying to determine that limit. And like documentation, it's better to have wrong documentation than no documentation, at least you have a target.


Tom Pullizzi
Falls Township, Pennsylvania
A. Tom,
I have been fortunate to have worked at two places with good water and one with unbelievably great water. Also, I have NOT been fortunate enough to have worked at a firm that could afford dialysis or deionization of a chrome anodizing tank. Therefore mixed bed DI makeup water was controlled by conductivity and further analysis was unnecessary knowing input water (average) quality.
The Surface Treatment & Finishing of Aluminum and its Alloys The Surface Finishing and Treatment of Aluminum and its Alloys [adv: suggestions on AbeBooks, Amazon & eBay affil links] by S. Wernick, R. Pinner, P.G. Sheasby, fifth edition, volume I starting on page 431 lists limits of 0.20 g. as NaCl and 0.50 g as Na2SO4. I have been lead to believe that this is the bible of aluminum finishing, if you can wade thru it.
The Electroplating Engineering Handbook ⇦ this on eBay, AbeBooks, or Amazon [affil link] , edited by Larry Durney, fourth edition lists 200 ppm of chloride and 500 ppm of sulphate as limits.
Any anodizer that uses bleed & feed method of controlling aluminum content will bleed out both ions faster than they will come in, if DI is used for water adds, UNLESS you have terrible water and do not properly monitor the conductivity light. My reference is mixed bed resin, 2 to 1, with two units in tandem with a 50 K ohm warning light in between the tanks. We rarely had less than 1 meg ohm water. Obviously, bad water in the last desmut rinse could contaminate the anodize tank in more than bleed & feed would take care of. Extremely high drag out parts without proper dripping would complicate it also. In my circumstances, I did not have this, so testing was a waste of time and money that could definitely be better used in other places.
PS: Never etched or pitted a part in the anodize tank.
James Watts- Navarre, Florida
by Runge & Kaufman
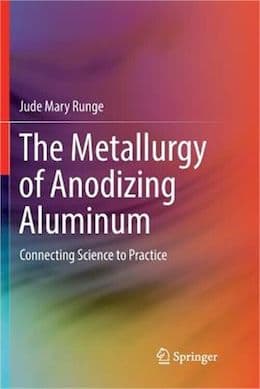
on eBay or Amazon
or AbeBooks
(affil link)
Q. Hi,
I am trying to find a fast and accurate method for testing Chlorides (ppm) in anodizing solutions, with copper and Al as contamination.
Can you help me?
Thank you.
- Beer Sheva, Israel
April 30, 2013
A. To 50 ml sample, add 10 ml 1:1 HNO3. Now add 5 ml 10% AgNO3 solution to precipitate Cl- as AgCl. Filter through a glass mat in a Gooch crucible (tared) dry the crucible @ 110 °C to constant weight, and finish via gravimetry.
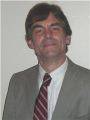
Dave Wichern
Consultant - The Bronx, New York
Q, A, or Comment on THIS thread -or- Start a NEW Thread