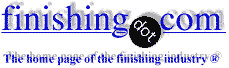
-----
Suggested cathode material for chromic acid anodizing
Q. Good morning everyone,
I'm looking for some suggestions on materials to be used for cathodes in a chromic anodizing process tank and for anode/cathode surface ratio.
I would be more than happy to hear your suggestions and or your experiences.
Best regards,
Canada
1996
A. Hmmm--never really thought about that one. But the The Canning Handbook [on eBay, Amazon, AbeBooks affil links] says stainless steel cathodes with a surface area of 1/10 to 1/5 of the anode area.
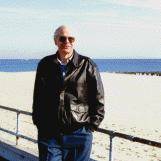
Ted Mooney, P.E.
Striving to live Aloha
(Ted can offer longterm or instant help)
finishing.com - Pine Beach, New Jersey
1996
A. Typically the tank serves as the cathode in chromic acid anodize. Very often tanks are constructed of steel. In order to prevent the build up of excessive amounts of trivalent chromium, the tank walls should be shielded to reduce the effective cathode area. The cathode area required to produce satisfactory anodic coatings is only about 5 percent of the anode area.
Reference: American Electroplaters Society illustrated lecture series -- "Anodizing Aluminum and Its Alloys", M. Schwartz, 1985.
aerospace - Windsor Locks, Connecticut
1996
A. I used strips of 300 SS with a ratio of 8 to 1 part to cathode and 22 volts and it worked fine as long as the normal analysis was done. Virtually idiot proof. If you have not done chromic anodizing, be ready for the first few loads to produce green colored parts, until it gets some aluminum in it and then they will turn the normal grey. Do not let your temperature get high. Anodizing generates a lot of heat and it is a tight temp range for optimum results. Remember to calibrate your pH meter with a 1.0 standard. You are on an asymptotic tail at that pH. Make sure your probe will work at that pH and use a double junction probe or one that you can refill because you will contaminate it very fast with a normal probe. There are some good cheaper ones on the market. Doing a little homework on that will save several hundred dollars a year on replacement probes. P.S. do not leave it in the sample any longer than is necessary.
James Watts- Navarre, Florida
1996
Q. Just some thoughts on this thread.
I am wondering if there is any benefit to using stainless steel plates rather than the tank itself as the cathode as far as bath longevity is concerned?
Our setup uses a mild steel tank as the cathode. We run a porous pot to keep the trivalent levels in check, and cation exchange the bath to remove other impurities.
I have also read about hanging stainless steel plates as the anode for "activating the acid" when mixing a new bath. I have no idea what this is supposed to do (it was written in a spec from Hartzell Propeller Products). I have never tried it. Maybe someone else has.
Regards,
propellers - Tucson, Arizona
1996
A. We processed Chromic Acid Anodize using lead coils for the cathodes and they also served as the cooling coils, a very ideal situation that we were very happy using for many years. Cathode/Anode ratio 1/8.
With the changing environmental regulations, about a year ago we switched to aluminum cathodes with a Cathode/Anode ratio about 1/6. We find that the higher conductivity of the aluminum could have allowed easily for a 1/10 cathode/anode ratio. We are very pleased with the aluminum cathodes and even if there was not an environmental concern, aluminum cathodes would be our choice. The higher conductivity of the aluminum permits a very efficient Chromic Acid Anodizing process that we process everyday.
anodizing shop - Philadelphia, Pennsylvania
1996
A. Re: Dennis' comment. Why end up using a porous pot more than is necessary by using a great excess of cathode. I have seen steel tanks that they put glass that has wire on the inside and covered the bottom and sides of the tank with it. The glass cracks and exposes "the right amount of tank". Not my cup of tea, but it worked quite well. I can see dummying the bath with aluminum part to break it in and avoid the green startup color but do not see what a SS anode would do other than put chrome, nickel and iron in it.
Re: Joe's comment. I had always wondered about using aluminum as it is outstanding in sulfuric tanks with its superior conductivity. I was afraid that it would dissolve in the chromic acid. Had not heard of aluminum when I was doing chromic. Lead works, but puts lead chromate in the tank and my preference is to keep dirt and trash out if at all practical. Also the disposal site was excessively interested and wanted more money.
- Navarre, Florida
1996
A. Hello,
Just to tell you that your cathodes can be made of titanium, lead or stainless steel. Well I hope you have success, greetings from Mexico by the way.
- Mexico City, Mexico
2001
Multiple threads merged: please forgive chronology errors and repetition 🙂
Q. We are working to install a MIL-A-8625 / MIL-PRF-8625
[⇦ this spec on DLA] Type 1B Chromic Anodize bath.
1. Are Teflon heaters generally used during cold weather?
2. Are Aluminum Cathodes recommended?
3. Are Titanium coils OK, or are plate/frame heat exchangers more common. We have heard that both could leak acid into the chiller fluid.
What are your thoughts?
- Oldsmar, Florida
2003
A. Teflon heaters sound fine but, because the anodizing process usually runs at 68 to 72 °F. (room temperature), and the rectifiers provide plenty of heat in operation, few installations actually have heaters.
Many, but not all, people feel that aluminum cathodes are the way to go because of energy savings.
Titanium coils are okay, as are external heat exchangers; both are widely used. But because both localized cooling & localized agitation are required, I believe that external heat exchangers are gaining dominance.
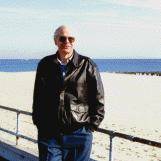
Ted Mooney, P.E.
Striving to live Aloha
(Ted can offer longterm or instant help)
finishing.com - Pine Beach, New Jersey
2003
A. You can use steel cathodes in chromic acid anodizing, you can even use the steel tank for the cathode. I have never heard of using aluminum cathodes in chromic anodizing.
The titanium might introduce a bipolar or galvanic stray current -- so if you do use titanium, tie it (connect it) to the cathode side. Teflon would be better.
Like Mr. Mooney said, especially in Florida, you do not need a heater unless you are somewhere around the latitude of Jacksonville, and then only on Monday morning.
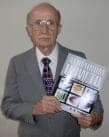
Robert H Probert
Robert H Probert Technical Services

Garner, North Carolina
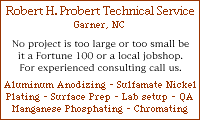
2003
Q. We have an existing process line and chromic anodize per MIL-A-8625 / MIL-PRF-8625 [⇦ this spec on DLA]. We presently use lead cathodes on aluminum hooks which are suspended along the sides of the tank from bus bars. The connections between the hooks, cathodes, and bus bar require extensive cleaning to maintain conductivity. Is there a better type of cathode that would be more reliable and less labor intensive.
Michael DalleoAerospace - Bloomfield, Connecticut, USA
2004
A. Throw the aluminum hooks away. Bend the lead cathodes over and then under the tank lip and make contact with copper bolts thru copper lugs to copper cable or buss. Note: You can use steel cathodes. Also a very high ratio of anode to cathode is favorable, even as high as 20/1. Repeat, that is high anode and low cathode.
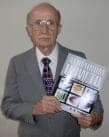
Robert H Probert
Robert H Probert Technical Services

Garner, North Carolina
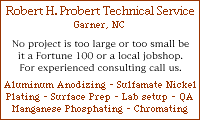
2004
A. Although we have never recommended it before our information now says that aluminum cathodes may work in chromic acid anodizing and possibly save electricity. We would very much like to work with you to try our aluminum cathodes on an approval basis.
Drew Nosti CEF
Co-chairperson AESF Light Metal Committee Member AAC Hard Coat Committee
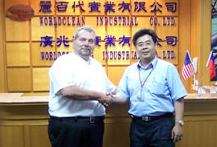
Drew Nosti, CEF
Anodize USA

Ladson, South Carolina
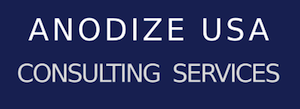
2004
Multiple threads merged: please forgive chronology errors and repetition 🙂
Eroded Tank Walls in Chromic Acid Anodizing
Q. Recently our chromic acid anodizing process has shown signs of pitting on the tank. The system that we use is the tank (mild steel) serves as the cathode. We have been using this process for 40 years and not till recently have we seen pitting on the tank. We have plastic bumpers around the inside of the tank to prevent the parts (cathode) from touching. Our tank is about 750 gallons; the makeup is 31/52 g/l free acid about 0.3 to 1.0 pH. Any insights would be appreciated. Thanks.
George Hemmingerpropellers - Kent, Washington, USA
2005
?. What is the chloride content of the make-up water?
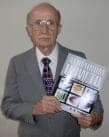
Robert H Probert
Robert H Probert Technical Services

Garner, North Carolina
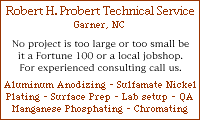
2005
A. I have discovered that the problem that you mentioned is actually pretty common for chromic anodizing baths where you use the tank as the cathode. Our shop did this for many years also without failure, then all of the sudden we went through 3 tanks in 3 years. We did not have chloride contamination. I would be willing to bet that the pitting you see is near the solution level and within 6 inches on either side of the corners. I think that the problem has something to do with how the tank distributes current and imperfections in the steel. Your tank will eventually fail. The ultimate solution is to install a PVC or polypropylene liner. You will then need to use steel sheet as the cathodes.

Jon Barrows, MSF, EHSSC
Kansas City
2005
Chromic acid anodes catch fire when dry
Q. George, Robert, Jon, or anyone else who is familiar with chromic acid anodizing ...
A large facility that I am familiar with has had people burned on two occasions now while doing maintenance on their drained chromic acid tank because the cathodes suddenly "flared up" after a spark or a mechanical scrape.
Perhaps the presence of aluminum fines of some sort, and/or the chromic acid acting as an oxidizer, makes this surface very ready to ignite at some particular dryness range after draining (probably the drier, the more prone, but that's supposition so far).
The most important part for us is trying to figure out a protocol for prevention in the future. Have you ever heard of it? Do you exercise any particular protocol to prevent it? If you haven't heard of it, let this be a heads up, it's real.
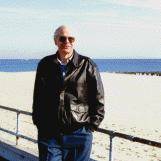
Ted Mooney, P.E.
Striving to live Aloha
(Ted can offer longterm or instant help)
finishing.com - Pine Beach, New Jersey
2005
A. Is it unthinkable that the flammable metal is plated-out chromium? Although, even porous iron and chromic oxide could flare. I'm surprised if full-density iron could do this, regardless of surface condition. I'm curious how much visible crusty deposits were on surfaces nearby. Was it near the bottom, middle, or top?
James Swenson- Los Angeles, California, USA
2005
Q. "Crusty" may be as good a word as any. I would say that the surface of the cathodes had a relatively thin "crust" of foreign material, that looked about like medium to course sandpaper, with the coating perhaps no thicker than the largest "grain". I don't think there was a particular top to bottom distribution, but it was all below solution level.
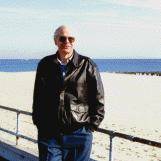
Ted Mooney, P.E.
Striving to live Aloha
(Ted can offer longterm or instant help)
finishing.com - Pine Beach, New Jersey
2005
Multiple threads merged: please forgive chronology errors and repetition 🙂
Q. Customer is using Aluminum Cathodes in their Chromic Acid Anodize. Large tank - 55,000 Liters. Application is for aircraft / aerospace parts. Problem they are having is when power is turned off the aluminum is attacked. They have a recovery system that is working overtime to clean up the aluminum in the bath. Aluminum cathodes are replaced more frequently than they would like.
What might be other option for cathode material? I am guessing Lead. Has anyone information on other materials besides aluminum or lead that would "work" in this application? I was asked about Titanium for Cathode material - not a very good conductor and probably a worse choice than aluminum - yes? When power is turned off the titanium probably would hold up pretty well. Negative charge on Titanium in Chromic doesn't sound good. Any information would be appreciated.
Vulcanium Corp. - Northbrook, Illinois, U.S.A.
2006
A. British defense standards advice the use of mild steel or stainless steel for cathodic materials in chromic acid anodizing.
Arnoldo CastroStudent - San José, Costa Rica
2006
Q. Please let me know if some company uses stainless steel cathodes for chromic anodizing process.If yes, which one (304, 316, ...) is recommended for chromic anodizing?
Meggie-Thuy NguyenBombardier Aerospace - Montreal, (QC)
2006
A. Hi all. Looking at all these merged threads, it seems that every common metal has been successfully used: steel, stainless steel, titanium, aluminum, lead. On the basis of poor conductivity, high cost, and no particular need, it's probably safe to strike titanium off the list. For environmental reasons, I'd probably personally strike lead.
Regards,
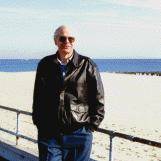
Ted Mooney, P.E.
Striving to live Aloha
(Ted can offer longterm or instant help)
finishing.com - Pine Beach, New Jersey
January 2006
Carbon/Soot buildup on chromic acid anodizing cathodes
Q. Type 1/1B Chromic Acid anodize tank per MIL-DTL-8625.
Replaced cathodes, and old cathodes have extremely heavy buildup of black soot. I pulled them and cleaned them eight months ago, prior to that it had been a few years since they were cleaned. There is more buildup on them now in eight months than there was from four or so years. They are steel but we do not know what specific steel they are. We have been having an ongoing issue with high currents, 50% higher than normal. All concentrations are within spec.
What could cause the buildup?
Precision Protective Coatings - Savannah, Georgia, USA
January 21, 2020
! I just noticed the comment from Terry about aluminum cathodes in chromic acid anodizing. I have always warned customers who are looking at using aluminum in this application that it is actually against the Aerospace specification unless there is a variance given for each operation. I can see many problems with using aluminum and would not recommend them. I would love to sell them but stay with Stainless.
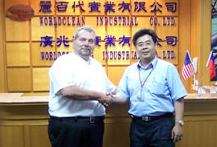
Drew Nosti, CEF
Anodize USA

Ladson, South Carolina
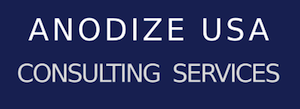
February 20, 2020
A. One of my clients has used aluminum cathodes since 2005. He does aerospace and other work for Boeing, Bell, et al -- absolutely no problem.
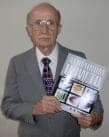
Robert H Probert
Robert H Probert Technical Services

Garner, North Carolina
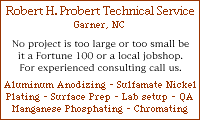
February 20, 2020

Q, A, or Comment on THIS thread -or- Start a NEW Thread