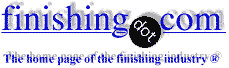
-----
Mechanical polishing vs. electropolishing of stainless steel
Q. Electropolishing of stainless from our customers' responses are overrated. Our customers never tells us about the cost of electropolishing their products ( I suspect it's a lot). They rather buy our products then have it electropolished.
We do mechanically polished stainless and according to recently lab reports, we now can produce a double-sided True #8 mirror polished sheet (note: NOT A #7 mirror with all the polishing lines) with 0.774-0.997 microinch. This compare to electropolished finishes which typically range in the 2-5 microinch, is a cleaner and superior finish.
In fairness, we have fittings products that are mechanically polished and the labs results were 5.95 microinch higher than electropolish materials, but our materials looks nicer. More or a mirror finish than hazy mirror look.
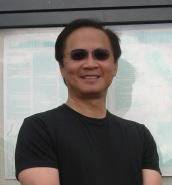
Michael Liu Taylor
specialty stainless steel distributor - Dallas, Texas
A. Dear Mike:
There is a lot of misunderstanding about proper applications for electropolishing.
Electropolishing simultaneously cleans, smoothes, deburrs, passivates, and improves corrosion resistance of stainless steels. Electropolishing offers excellent decorative properties, but its principal strength lies in the other properties it offers for the aerospace, food, dairy, medical, pharmaceutical, bio-pharmaceutical, semiconductor, and other high tech industries.
In general, we agree that mechanical finishing can produce better "mirror" finishes at a lower cost, but mechanical finishing alone cannot match all of the surface enhancements available from electropolishing. Electropolishing competes with mechanical finishing in some areas, but its most important applications are those which are beyond the capability of buffing and other mechanical finishes. Of course, any added cost must be justified by the enhanced properties obtained from electropolishing.
Metal Coating Process Corporation - Charlotte, North Carolina
1996
Q. Dear Ed,
I'm sorry if I sounded too blunt, but I was faxed an electropolisher's brochure by my customer.
In the brochure, it stated that mechanical mirror polished stainless ranges in the 4-10 microinch whereas electropolished surface can reach 2-5 microinch. This may be true a few years back, but not today. Our double-side mirror polished sheets actually went below 1 microinch in a recent surface roughness lab report.
Since stainless steel alloy has a self oxidation layer that prevent corrosion & rust and the self oxidation layer is best when surface of the metals is at their cleanness. I questioned whether electropolishing actually adds anything to the natural corrosive resistant properties of the stainless steel alloys.
Perhaps the Specialty Steel Industry of North America or the Nickel Development Institute can shed some light on this subject.
I sent samples to several electropolishing companies for their tests and evaluations, so far we haven't got anything back.
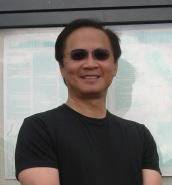
Michael Liu Taylor
specialty stainless steel distributor - Dallas, Texas
1996
2001
Q. I am using phosphoric acid and sulfuric acid solution for electropolishing of 316 L /LS stainless steel.But the result is very bad, I can't get the bright surface but dull surface! I have already try all the setting (voltage, current density), still can't get the polishing effect!
Why the result is like that?Is that the solution problem?(150 ml water, 300 ml phosphoric acid (85%), 550 ml sulfuric acid)
- Penang, Malaysia
1996
Q. We want to improve the surface finish of ss-304,ss-409 fabricated equipment of having 800 mm diameter to 3000 mm diameter vessel. How can I do electropolishing in such type of vessel of 800 mm to 3000 mm diameter. kindly guide us
Santosh kumarbuyer - baddi, H.P. , India
2007
A. You can learn a bit of what you want to know about electropolishing from such sources as the
Electroplating Engineering Handbook ⇦ this on
eBay,
AbeBooks, or
Amazon [affil link]
, gentlemen.
Chong: the two most likely problems are excessive water in the solution and inadequate current density. The etching range is large, the electropolishing range is small :-)
Santosh: It's not impossible to do electropolishing yourself, but it's not easy, and generally after some hands-on training one would practice their skills on expendable parts for a while. You may etch these vessels, which could be a big risk to take. There are companies specializing in on-site electropolishing for situations like this, and you may wish to contact one of them instead. Good luck.
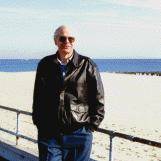
Ted Mooney, P.E.
Striving to live Aloha
(Ted can offer longterm or instant help)
finishing.com - Pine Beach, New Jersey
2007
A. Hi.
Only with the correct amount of chemicals can electropolish be achieved. make sure that you are using the correct current density (it depends on the formula), temperature, distance between anode and cathode and enough area in the anode (two times the area of the piece to electropolish)
- Medellin, antioquia, Colombia
January 16, 2008
Q. Dear Diego,
I'm a novice at electropolishing and I'm trying to understand the theory.
Can you please give the formulae for calculating the current density?!
I have seen the current density-voltage curve showing the 3 regions of operation in many scientific papers, but I'm not sure how they arrived at it. What is the formula that has been used?
- Ann Arbor, Michigan, USA
November 10, 2010
Q. We would like to electropolish 400 series ss please advice chemical formulation
Shushil Tripathiemployee - Ghaziabad, UP, India
October 31, 2011
A. Hi, Sushil.
There are at least a half-dozen non-proprietary formulas in use, and each has specific advantages. There are also at least a half-dozen proprietary formulas available. But as mentioned, electropolishing is a reasonably difficult operation to do successfully and posting one of those non-proprietary formulas here probably won't get you any closer to success as you will need to simultaneously control many factors including proper mechanical prep, proper cleaning an pretreatment, water content, local current density, local temperature, dissolved metals, racking so hydrogen bubbles do not interfere with polishing, etc. Can you please describe which, if any, finishing books you have available and exactly what problems you are having so that we can try to steer you towards a solution? If you are starting new, and an experienced electropolisher is not available to help you, you will probably need to go to a proprietary supplier like Metal Coating Process Corp. or Russamer Lab [a finishing.com supporting advertiser] to guide you through the maze. Best of luck.
Regards,
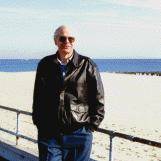
Ted Mooney, P.E.
Striving to live Aloha
(Ted can offer longterm or instant help)
finishing.com - Pine Beach, New Jersey
November 1, 2011
October 26, 2017
Q. Hello all !
We manufacture metal chairs made of SS frames (grade 202). The size of the model varies from model to model. Let's say 600 x 600 x 800 mm.
As a finishing process, we do manual buffing in 4 stages for every single product. This section is having lot of manpower and the costs are going high.
Main problem- High costs & low productivity.
In this case, is it better to go for electropolishing where I can get the finishing done in bulk? Or shall I continue with the same manual buffing ?
Aim- Mirror finish & High productivity.
Thank you.
Sushanth Reddy- Bangalore, India
A. Other than a polished finish, you never did specify the surface profile. Electropolishing will achieve good results, but you still may need to prep some areas. There are also some costly big mechanical systems that might work; however, it is difficult to recommend alternatives without knowing more

AF Kenton
retired business owner - Hatboro, Pennsylvania
October 30, 2017
A. Hi. The advantage of electropolishing is generally neither appearance nor economy but a surface with no tooth, which decreases stickiness & contamination, and improves corrosion resistance. Generally these are not very important points for chairs. If most of the welds are hidden under cushions, etc., you may wish to fabricate from pre-polished tubing instead of polishing after fabrication.
Regards,
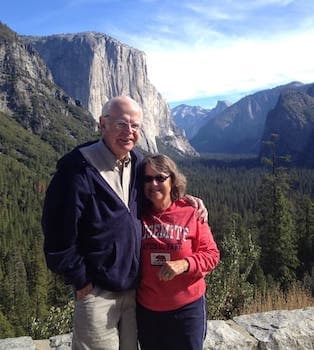
Ted Mooney, P.E. RET
Striving to live Aloha
(Ted can offer longterm or instant help)
finishing.com - Pine Beach, New Jersey
October 2017
May 29, 2018
Q. Good morning all,
We mechanically polish 316 stainless steel for the superyacht industry. The other day we came up against a management company for a 102m yacht we were quoting for.
We offered a scratch removal and mirror finish service, both were achieved on the test patch however, the uniformity (micro scratches caused when buffing) of these bannisters were different from the original finish -- result can be seen here:
(click graphic for higher rez)
The finish considering the level of scratches was more than acceptable on most yachts however, the management team stated that they all the stainless steel on board had been electropolished when the yacht was manufactured in 2017, we were amazed and intrigued.
We have since taken parts to a couple of established electro polishing companies near us and neither can achieve or even claim to be able to achieve a #8 mirror finish, much to our disappointment, would have saved us a lot of time.
Do any of you experienced e-polishers know if it is possible to achieve a #8 mirror finish? On the flip side, could any mechanical polishers tell us how to improve our #8 mirror finish so that we can get no visual signs of buffing. We currently use sisal rings and blue paste compound.
Thanks,
Luke
Marine Polishing - Cubelles, Barcelona, Spain
A. #8 is referred to as "mirror" finish, highly reflective, no directional lines from buffing at all.
Two suggestions:
1. Buff as you have been doing, clean carefully, then have an electropolisher run them just long enough to remove the microscopic scratches from your buffing - perhaps two or three minutes.
2. Polish as you have been doing, then buff with a soft loose section buff using white buffing bar
⇦ on
eBay
or
Amazon [affil link]
and working across the direction of the previous buffing. Use light pressure.
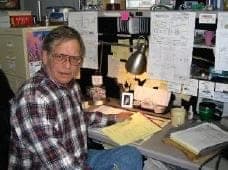
Jeffrey Holmes, CEF
Spartanburg, South Carolina
May 31, 2018
A. Your present buffing process is leaving fine scratches because the buffing wheel is too hard, and the compound probably too coarse.
Try a second buffing using a soft unsewn cotton buff and white rouge compound at low pressure.
If still not good enough, a brief electropolish of 3 or 4 minutes should get you where you want to be.
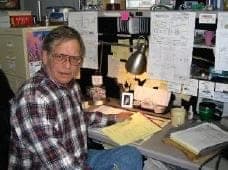
Jeffrey Holmes, CEF
Spartanburg, South Carolina
June 1, 2018
Q. Dear Jeffrey,
Thanks for taking the time to reply, greatly appreciated.
Good tips. Your 1st tip, regarding polishing and electropolishing for a short time is what we originally thought may be the key, we will carry out some tests and I will report back here. Have you ever tried this method?
As for the buffing process we are using sisal wheels (cotton), I have found last week a new supplier and he recommended felt discs for the final final buff, again I will report back if these give the desired result.
All the best,
Luke
LUMU SOLUTIONS - Cubelles, Barcelona, Spain
June 3, 2018
A. Sisal is NOT cotton. Sisal is faster cutting and will leave more visible scratches.
After Sisal, use soft cotton buffs, moderate to light pressure, white rouge.
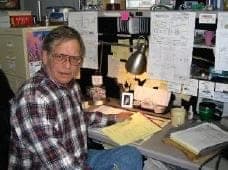
Jeffrey Holmes, CEF
Spartanburg, South Carolina
June 6, 2018

Q, A, or Comment on THIS thread -or- Start a NEW Thread