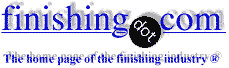
-----
Surface Treatment for Injection Molds
We are looking for essentially two things:-
1. A surface treatment to prevent seizing of moving parts within an injection mold. The steels we use are high in chrome content and hardened to 54- Rockwell HRC. The mold temperature is 80 °C when processing the molten plastic. Gases given off by the process in addition to the high temperature of the plastic 300 °C and high injection pressures 1000+ bar all contribute to the tendency of the moving mold parts to seize.
2. A surface treatment which would extend the life of mold cavities due to wear induced by the molten plastic moving over the mold cavity surface.
Any help in this area would be gratefully received.
Oy - Finland
1996
For somewhat similar applications, hard chromium plating is usually the solution. You might want to go over your specs with a supplier of chromium plating systems, such as Atotech, and see if the specifics of your particular situation match this general solution.
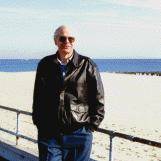
Ted Mooney, P.E.
Striving to live Aloha
(Ted is available for instant or longterm help)
finishing.com - Pine Beach, New Jersey
1996
I am interested in finding a very hard substance which can be electro plated for an invention. Can you help?
Thanks,
Bainbridge Island, Washington
1996
Well, 'very hard' is relative, and there are surely many other considerations besides hardness, but for decades the generic solution to this question has often been hard chrome plating. Our Shop Directory lists several hard chrome platers, as well as purveyors of some alternate technologies.
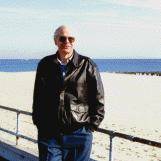
Ted Mooney, P.E.
Striving to live Aloha
(Ted is available for instant or longterm help)
finishing.com - Pine Beach, New Jersey
1996
Several possibilities come to mind; traditional hard chrome plating, electroless nickel [nickel phosphorus] plating, or electroless nickel-boron coating. Electroless nickel-boron coating is uniform, has an as-plated hardness of 700+ VHN, heat treatable to 900+ VHN. It also has unusually high wear characteristics.
-Kent
Fort Worth, Texas, USA
1996
One possible treatment that you can realize on your mould cavities could be a Chemical Vacuum Deposition (CVD) or Physical Vacuum Deposition of (PVD) of different very had substances. For example Titanium nitride is currently used for surface hardening of High Speed Steel cutting tools.The surface hardness could reach 2500 Vickers or more.
Facilities for PVD or CVD treatment with different compound could be easily found in several countries.
Best regards
- Florence, Italy
1996
A good combination would be electroless nickel (Low-Phos) and a PVD coating. Good Luck.
David M. Weaver [deceased]- Toccoa, Georgia
Ed. note: With great sadness we must advise that David passed awayt on Aug. 15, 2003.
1996
If the geometry of the cavity is not complex, a Electroless Nickel - Silicon Carbide brings a very good wear resistance.
An over-layer of Electroless + PTFE (3 microns) will extend the life of the cavity also.
Bnei Berak, Israel
1996
Q, A, or Comment on THIS thread -or- Start a NEW Thread